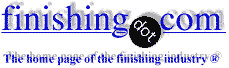
-----
Plating glass-to-metal seals, Q&As, Problems & Solutions
GTMS = Glass to Metal Seals
Glass to meal seals are generally used where hermetic sealing is necessary.
As a simple example, when running wiring to a thermostat in a freezer, you could enclose either the wires or the thermostat in a blob of glass melted around them which you can seal into the freezer wall to stop cold air leaving and warm air entering.
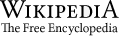
Glass-to-metal_seal
Q. Hey Michael, what temperature and duration do you bake at for testing the nickel adhesion on kovar?
Tim Martin- Beverly Massachusetts
December 2, 2021
⇩ Related postings, oldest first ⇩
Nickel and gold plated Kovar cracks at weld seam
Q. We are trying to seam-weld a Kovar lid onto a ceramic substrate on top of which a Kovar rim is brazed for hermetic sealing. Both the Kovar lid and the Kovar rim are nickel underplated first, followed by gold plating.
After the resistance seam welding, cracks are observed to propagate along the weld seam, leading to failure in achieving hermeticity. Can anybody provide suggestions of how to eliminate the cracking problem?
While the detailed plating process for the Kovar rim on top of the ceramic substrate is unknown (it is a purchased part), two different electrolytic nickel platings of the Kovar lid have been tried, but both gave the same cracking problem. One of them is semi-bright nickel (~110 microinches) followed by sulphamate nickel (~130 micro-inches). The other one is nickel strike (~30 micro-inches) followed by the same sulphamate nickel (~130 micro-inches).
Thanks for the input.
- Taipei, Taiwan
2002
A. I believe the acid bath would introduce P or S into the coating layer which later might cause solidification problem depending on the coating thickness and welding process.
Is electroless plating a better process? not to introduce S or P.
Please comment
- Wilmington, Massachusetts
2002
A. Electroless plating is typically Phosphorous or Boron based. Phosphorous nickel is used primarily for seam sealing now welding where the nickel is flowed on the seal ring (~ 700 °C). The % of phosphorous is varied from 2- 15% for corrosion purposes. Due to the stress at the higher percentages cracking occurs in seam seals.
Hope this helps.
- Allentown, Pennsylvania
October 16, 2009
A. Then let's study the deposited stress of the nickel. If it is between 5000 psi compressive and 10,000 psi tensile, then let's look for co-deposited impurities, the most common of which is copper which is in ALL nickel anodes (and must be continually dummied out).
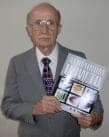
Robert H Probert
Robert H Probert Technical Services

Garner, North Carolina
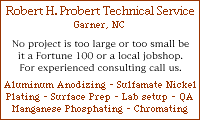
December 3, 2021
Multiple threads merged: please forgive chronology errors and repetition 🙂
Will boron EN survive laser welding where phosphorous EN fails?
2001Q. I am sealing a glass window in to a Nickel plated Kovar lid. The plating is electroplated with a phosphorus based bath and is 100-200 microinch thick. The kovar lid has to go through 3 processes.
1. Sealing glass reflow of the glass lens at up to 400 °C.
2. Resistance welding using seam sealing.
3. Laser welding in a later process.
The laser welding and resistance welding appear to be fine, but the plating oxidizes to the point of being black and sometimes blister for at extended periods [1-5 minutes] at 400 °C. I have seen this phenomena before in particular blisters with phosphorus nickel on Aluminum.
Questions:
1. Would using a much less common Boron bath help.
2. Would a gold plating of 30-50 °C acting as a barrier help? [Not a good thing for the laser welding and in some degree the resistance welding processes]
Thanks in advance for any suggestions.
- San Jose, California
A. I would examine the preparation of the material and the underlayment plating, if any. I would guess that the problem is that the nickel isn't bonded well with the substrate. We plate Kovar parts, and the customer requires a high temp bake out to test adhesion.
Michael Brewington- Salisbury, Maryland, USA
2001
A. I think the first thing I would do as an experiment is to try a thicker electroless nickel plating as a way of ensuring that porosity in the plating is not the problem.
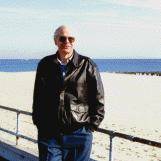
Ted Mooney, P.E.
Striving to live Aloha
(Ted can offer longterm or instant help)
finishing.com - Pine Beach, New Jersey
2001
Can we skip gold if not soldering? Will bare Kovar corrode?
Q. I am designing an optoelectronics package made out of Kovar and plated with Gold over electrolytic Nickel. This package should survive for 20 years and has to pass tests such as 85 C/85% RH for 2000 hours, etc. I have 2 questions:
1. We do not need the gold for soldering or aesthetics so I am thinking of removing the gold plating. Then the Nickel plating will oxidize. Will this oxidation, besides the package discoloration, affect functionally the package?
2. I am sealing hermetically this package with laser welding or seam seal welding. hence, there is exposed fused Kovar at the sealing area. Do you know any specific coating, epoxy or paint that will protect the bare Kovar from corrosion?
Thank you in advance,
- Woburn, Massachusetts
2003
Multiple threads merged: please forgive chronology errors and repetition 🙂
Cobalt plating solves the diffusion problem
Q. I am trying to reproduce a process that was carried out successfully many years ago (20+). I want to gold plate on Nickel Iron and then braze the plated part into a assembly at 900 °C, the problem is that the gold defuses into the nickel or the nickel defuses into the gold. Either way, the problem was overcome by plating the nickel iron with Cobalt first. The parts are very small 1 mm dia. x 25 mm long and not vast quantities.
Can anyone help?
ceramic seals - Oldham,Lancashire, United Kingdom
June 24, 2013
A. You can plate it the same way you nickel plate it, except you substitute cobalt sulphate for the nickel sulphate. If you are using EN, a couple of companies sell ECobalt.
James Watts- Navarre, Florida
June 25, 2013
Reduction in Insulation resistance after electropolishing and electroless nickel plating
Q. Dear Sir,
We are manufacturing hermetic seals and recently we are facing problem with Insulation resistance of the connectors (Which used to be in terms of Giga ohm reduces to ohms) after electropolishing or plating.
Is there any solution to this?
Thanks and regards
Vidya
- Bangalore, India
July 26, 2013
Nickel Sulfamate Heat Treatment for Solderability
September 21, 2015Q. I am a recent addition to a facility that manufactures ceramics and custom hermetic components for various applications. Many of the sub-components that are used in our hermetic assemblies are nickel-plated for our customers' use or for brazing purposes.
This question is most specifically regarding the MoMn (Molybdenum-Manganese) metallization process that we use on many ceramic parts.
Where I am, we hand-brush MoMn on to ceramic parts and bake the dispersion into the ceramic surface in a furnace. After this, they are quite easily plated electrolytically with our Nickel Sulfamate chemistry (we also strike with Wood's Nickel).
It is customary to "fire in" a layer of electrolytic Nickel plating (in many cases, we do this after electroless plating as well), and follow with a second layer of electrolytic (or electroless) nickel. This 2-step plating is often done for our own parts for better performance during brazing after mechanical assembly steps. Sometimes, it is also called out by customers in purchase agreements.
My question is this:
Is plating nickel twice a practice that is industry standard?
What does the annealing between plating steps accomplish?
The conventional thinking is that we cannot plate more than 100 micro-inches (about 2.5 microns) over MoMn metallization without plating defects showing up post-firing. Specifically, I have seen blisters after we sinter parts that have built up plating in high current density areas. Is this normal? If we plate a thinner layer of nickel, heat treat, and then follow with more nickel to meet customer thickness specifications, we usually do fine. What factors have the largest effect on blistering like this?
Any response or advice would be appreciated! I have received a lot of valuable advice from these forums but have never posted a question until now. A link to literature or some tips on MoMn-Metallized Nickel Plating would be welcome as well.
Chemical Engineer / Plating Supervisor - Laurens, South Carolina, USA
Corrosion resistance problem
Q. we are doing nickel sulphamate plating 7-10 µm (base material is MS); then glass to metal sealing at 960 °C; then electroless nickel phosphorus (10-12%) and thickness 4-7 µm; then bright tin (7-9 µm). After that we need salt spray test for 500 hours but we are unable to pass the test -- please help us.
Shruthi V Kumar- Bangalore, Karnataka, India.
October 10, 2018
Q. I manufacture GTMS Connectors and have a need to de-glass to save the shell. Can someone share the process of de-glassing GTMS connector?
Harminder Badesha- Upland, California, USA
August 4, 2021
A. If it is a silicate or borosilcate glass then dissolve the glass in Hydrofluoric Acid (HF).
Tom ReinEngineer - Albany, New York
November 29, 2021
Q, A, or Comment on THIS thread -or- Start a NEW Thread