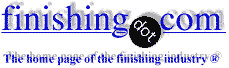
-----
Problem of white spots after Zinc Plating

Q. After plating there is a visible cloudy like on the surface and occasionally a rainbow one. We are using non-cyanide alkaline zinc. Plating parameters are 9-14 Zn 80-120 NaOH. What should be done to fix the problem?
Engineer - Calamba, Philippines
April 2, 2022
![]() |
A. Hello, Pabalan, Chemical Engineer - Nova Friburgo, Rio de Janeiro, Brazil April 7, 2022 A. The NaOH will not rinse off, causes the chromate to "rainbow", so kill it with a 1/4 % nitric acid ahead of the chromate. ![]() Robert H Probert Robert H Probert Technical Services ![]() Garner, North Carolina ![]() April 7, 2022 |
? Can you confirm if this happens after the plating tank, or when you mention "after plating", is it after the complete process, e.g after chromate and drying?
A. I can offer two thoughts based on researching similar issues
If issue happens after chromating, check that PH, solution concentration and immersion time is as per your spec on the chromate tank. Having my process off recommended spec somewhat did appear to cause some iridescence.
Plating thickness across the whole part - the way in which the chromate interacts with different areas of plating thickness may cause some iridescence to show?
It has been mentioned before on this website that contaminants inside the chromate tank from drag in can cause this issue. Simple way is to prepare a small new solution inside a beaker [beakers on
eBay
or
Amazon [affil link] and do a test run there to isolate this.
- Perth, Western Australia
April 19, 2022
⇩ Related postings, oldest first ⇩
Q. Dear Sir,
We are observing a problem of white spots after zinc plating. Can you please tell a solution for this problem? Thanking You, Yours Truly,
Pune , Maharashtra , India
2002
Q. We are also facing similar problems occasionally. Answer to this question will help us also.
Regards,
- Chennai, TN, India
2002
A. I am guessing that the white spots you are referring to is actually white rust, which means that the zinc layer has been corroded. If this happens right after plating, maybe the problem lies in the drying process (not completely dried up), leaving droplets of water on the surface of the plated parts. Other possibilities might be from poor final rinsing and poor chromate dip.
Hartarto Ciputra- Surabaya, Indonesia
2002
A. This is the common problem in White zinc. The most possible problems are in water rinses after plating & yellow passivation. First these things should be controlled. Secondly drying of the components is very important factor. Please look into that also. Very rarely there can be the problem of contaminations in the plating tank, which can be sorted out by various treatment you must be doing in your normal cleaning times. Please try & let me know.
SANTOSH ZOPEDUBAI WIRE - DUBAI, U.A.E.
2002
? Dear sir,
Before we attempt to answer your query, it is very important to know what base metal are you plating? What is the pretreatment sequence? What type of zinc plating are you doing? Lastly where does the white spot occur i.e., HCD, lcd or random? Above will give better insight into the problem.
- India
2002
Multiple threads merged: please forgive chronology errors and repetition 🙂
Non-Cyanide Zinc Plating Problem
Q. White patches seen after trivalent blue / yellow passivation in non-cyanide/alkaline zinc plating process. Please tell me that what will be root causes starting from degreasing to passivation.
Nitin KaparePlating Chemical Supplier - Pune, Maharashtra & India
January 9, 2009
A. Hi Nitin,
Do you observe the white patches after the passivations, cos many a times when the passivations parameters, like the ph, time, are not set it gives such appearance, secondly if you have a electrocleaner in the line for non cyanide zinc is preferable , cos the cleaning of components I quite important in case of non cyanide zinc, did you check the Hull Cell
⇦ huh?
for the working bath , do you observe any white patches and at last it have the zinc dissolution tank and are you maintaining the zinc content very well in the bath.
Thanks
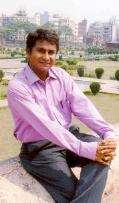
Praveen Kumar
plating process supplier
Mumbai, India
January 14, 2009
A. Is usually due to the hardness of the water and remove additives patent provider additives.
Oscar Villaoboschemical supplier - Guadalajara, Jalisco, Mexico
January 29, 2009
A. Check the Nitric Dip (activation prior to passivation).
With alkaline zinc you may need a strong (minimum 1% by volume) Nitric Acid Dip prior to passivation.
There can be many causes for patches, etc... but this seems to be the most common cause.
- Budapest, Hungary
February 24, 2009
Q. Our components after alkaline zinc plating are having white patches after 20 days even though the components are not exposed to environmental conditions in our plating shop, i.e., each component was packed with plastic cover separately and stored for 20 days. Now that we are observing white patches on the component, can any one explain the reason?
- Bangalore, Karnataka, India
September 26, 2012
A. Dear Mr. Raghavendra,
I think you are experiencing this because of a bad or absent chromating of the zinc plated parts. The white patches are zinc oxidation/corrosion. Zinc corrodes in air, so you must apply a chromate (hexavalent or trivalent, according to spec) conversion coating so it does not corrode a few days later.
Hope this can solve your issue, best regards!
fasteners manufacturer - Cañuelas, Buenos Aires, Argentina
October 1, 2012
A. The area of post water swill (even pre and post chromating) and a final hot water swill may be helpful. Packing inside plastic bag should be after proper drying.
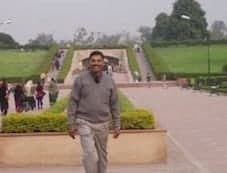
T.K. Mohan
plating process supplier - Mumbai, India
October 10, 2012
Q. Hello sir,
We are observing white patches right after zinc plating.
- Bangalore peenya, India
July 29, 2020
White Patches observed 4-5 days after Alkaline Zinc Plating (Cr6 Free)
Q. Our components after alkaline zinc plating (Cr6 Free + Top Coat) are having white patches after 4-5 days even though the components are not exposed to environmental conditions in our plating shop, i.e., each component was packed with plastic cover separately and stored. Now that we are observing white patches on the component. Can anyone explain the reason?
Digvijay Bhosale- Kolhapur, Maharashtra.
October 21, 2020
A. You are probably not neutralizing off the strong alkali from the alkaline zinc. Use a 1/4%/vol Nitric Acid between the plating and the chromate.
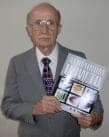
Robert H Probert
Robert H Probert Technical Services

Garner, North Carolina
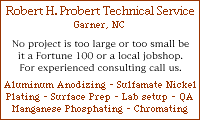
October 22, 2020
A. Please make sure that you can store your finished product at humidity [not] more than 90.
Do not pack you material immediately as after spin dry; there will be a chance of retaining moisture which may act as a SST chamber when you pack your finished product immediately in PP bags
- Pune Maharashtra
September 8, 2021
Q. Our components after alkaline zinc plating and black coating are having white patches after 4-5 days even though the components are not exposed to environmental conditions in our plating shop, i.e., each component was packed with plastic cover separately and stored. Now that we are observing white patches on the component. Can anyone explain the reason?
ANKIT SRIVASTAVAMANAGER - GURGAON
August 2, 2021
A. Hi Ankit. You copied & pasted Digvijay Bhosale's question, but then offered no comment to Robert Probert's answer to it. That seems kind of silly :-)
Please do us a favor and comment on Mr. Probert's proposed solution. Thanks!
Luck & Regards,
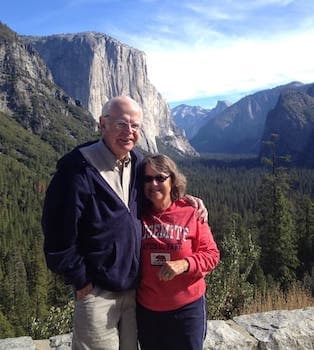
Ted Mooney, P.E. RET
Striving to live Aloha
(Ted is available for instant or longterm help)
finishing.com - Pine Beach, New Jersey
August 2021
⇦ Tip: Readers want to learn from your situation;
so some readers skip abstract questions.
Q. How to solve zinc white patches? Have any permanent solution?
- Kotture [India]
October 21, 2021
A. Hello,
We need more information about your process firstly to understand what the problem is. Is it NC alkaline zinc or acid zinc? What kind of passivation do you use? Do you have topcoat on it ?
But, by the looks of it, I would say it looks like alkaline zinc, and these spots can be easily solved by doing hull cell. Might be lack of an additive, probably the Carrier. If these white streaks appears on hull cell around MCD, then there's problem with hardness in your water you using for refill the level or you used to do the make-up. If so, you may want to use softened water in the future. Or just speak with your chemical supplier and explain the situation, they have additive for removing spots caused by hard water.
Keep in mind these things apply to alkaline zinc only.
Chemical Engineer - Bucharest
November 1, 2021
A. Ahead of the chromate, try a 1/2% Nitric Acid Dip to remove the alkali, then maybe the chromate will "take"
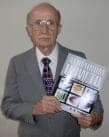
Robert H Probert
Robert H Probert Technical Services

Garner, North Carolina
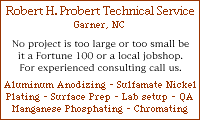
November 4, 2021
Q, A, or Comment on THIS thread -or- Start a NEW Thread