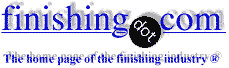
-----
Aluminum under water
I want to put assorted aluminum parts underwater; they are assembled into a 'sensor'. I have tried this previously with varying success (depending on the water I believe) with just a type II anodizing. I have put aluminum samples with a hardcoat (and seal I believe) underwater and they survive well. My problem with hardcoating is I have tight tolerance parts which don't fit together after hardcoating.
1. What is your opinion on the best coating to use on aluminum underwater (not saltwater but it could be somewhat 'hard')? I'm looking for a specific 'callout'.
2.Assuming it is some type of hardcoat, is there any way I can hold dimensional accuraccies to ±.0005" during that process? I don't care if there is buildup if it is a known buildup and doesn't easily scrape off.
3. Can I grind or machine hard anodized parts to restore tolerance without affecting the corrosion resistance of the coating?
Thanks.
Steve Kerrigan- Shoreview, Minnesota, USA
I think you were on the right track with hardcoating. Roughly one thousandth of an inch of aluminum will be consumed in building an anodizing thickness of two thousandths of an inch. So if you want a two thousandths coating, start with the part one thousandths of an inch undersize of what you want it to end up.
This question is very well answered by Sjon Westre in letter 7429; but also see letter 4212 which addresses some factors about tolerancing of holes, etc.
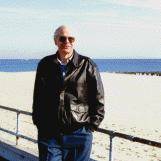
Ted Mooney, P.E.
Striving to live Aloha
(Ted can offer longterm or instant help)
finishing.com - Pine Beach, New Jersey
My company does quite a bit of work for underwater lighting & my customer has found the sealed hardcoat to hold up best.
Regarding thickness & holding tight tolerances, it is a general rule with hardcoat that we can hold tolerances ± 20%. So, if you requiired a full spec coating of .002", it would be ± .0004" thick.
David A. Kraft- Long Island City, New York
Hello Steve,
You could have the areas MASKED before hard anodize to eliminate coating those areas if they are not exposed to the environment. Frankly speaking, a reputable anodizer should be able to hold much tighter tolorances than ± 0.0005". As a matter of fact the MIL-SPEC allows for a MAXIMUM of 20% up to .002". We coat many parts for similar sea water applications and are able to provide customers with a coating that ranges from 0.0018-.0022 ( ± .0002 )consistently. Callout Mil-A-8625f type III Class I with nickel acetate seal (or other seal for corrosion resistance). Note: some significant amount of ABRASION resistance is lost when type III coatings are sealed.Be sure to specify your desired coating thickness and allowable tolorances. Hard anodize can be surfaced, but not easily. keep in mind that THREADS have TWO surfaces per side and build up that much more.
Good Luck,
Bill Grayson- Santa Cruz, California, USA
If it is a small sensor, maybe titanium or a Ti-Al alloy might be more practical than a coating. A resistant base material is always a good place to start off in a chemically active environment. However, if anodizing works, then the metrics/dimension tolerance you can live with here should not be an issue. Maybe you should look into another job shop if the anodizing you are having trouble with does not meet spec.
The alumina layer from anodizing is thin--any mechanical shaping will likely remove the protective layer. It is possible the anodizing process may be roughing the surface making connections seem more difficult to join; a bit of silicone lubricant might be indicated.
As far as coatings, tin is suitable for this application, and if the parts are small & the shapes are not complicated, maybe a PVD or CVD oxide or oxynitride might do the trick.
Dale Woika- Bellefonte, PA, US
Steve,
Here are some answers for you.
Hard coat is the answer but good quality hard coat. There are numerous shops doing what they consider hard coat by just anodizing longer . Use a top quality shop specializing in Hard coat, preferably at 30-32f (my opinion). You can spell out your dimensions ahead of time and I'm sure they can help you. You may have to take into consideration the build up of oxide prior to your machining operation. Remember for every mil of oxide you want ,you will increase your dimension by approximately 1/2 mil. And yes you can grind off good Hard coat to a dimension.
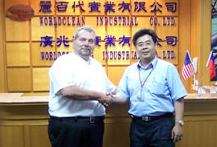
Drew Nosti, CEF
Anodize USA

Ladson, South Carolina
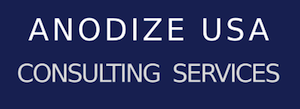
Q, A, or Comment on THIS thread -or- Start a NEW Thread