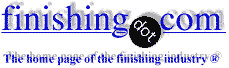
-----
Tin lead plating problems
2002
Hi...
I am a Process Engineer in a flex PCB shop. I have a problem on my tin lead plating. We are using Sn/Pb 63:37 solder anodes. The problems that I am facing are :
1. The surface finishing became discolored; sometimes the surface turns whitish, or blackish.
2. There are parts that undergo 2 selective platings. This will incorporates dryfilm. The problem that we are facing is that the parts that were initially bright turned tarnished after undergoing resist stripping.
3. Are tin lead plated parts sensitive to acidic water conditions during rinsing?
I would appreciate help from you guys out there.
Thanks,
Qairyul Elfee Md. LatipM-Flex (Malaysia)Sdn. Bhd. - Malaysia
Quite a common problem: we perform the tin lead plating as well; after plating, dip it into some water-soluble anti-tarnish immediately after plating. Gives you 6 months with no change in color, also no apparent soldering problems.
Tan Kay Leong- Malaysia
2002
Yes, an acidic dip will definitely cause discoloration of the tin. The amount varies from some to bad depending on the acidic solution, impurities in it, the qualities of the rinses and air time before the rinses.
James Watts- Navarre, Florida
2002
Discoloration in Tin-Lead Barrel Plated Parts
Q. I have a supplier who is trying to get acceptance on their latest lot of parts. These are tubular parts and roughly in the middle the part, after cure, is much darker on one end then on the other.
When EDS was conducted the Sn content of the "normal" color was 93.2-97.6 and on the discolored end 97.7-95.6.
The Pb content on the "normal" color was 2.4-6.8 and on the discolored end 4.4-12.3.
I should also mention there is a slight ridge of material where the normal and discolored area meet.
These are barrel plated. The excuse from the plater is variation in current density is root cause. Does variation in current density cause different layering of materials?
Quality Engineer - Albuquerque, New Mexico
July 27, 2015
? Hi LeAnna. So that we don't misunderstand you, I assume that one part, or some small percentage of the parts exhibit this problem, not all of the parts?
Also, what do you mean by "after cure" -- what is this "curing" operation? Thanks.
Regards,
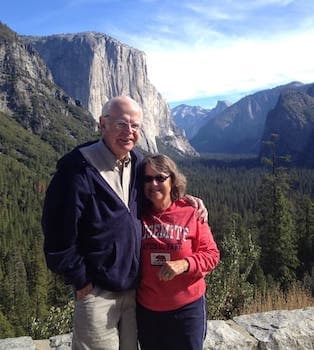
Ted Mooney, P.E. RET
Striving to live Aloha
(Ted can offer longterm or instant help)
finishing.com - Pine Beach, New Jersey
July 2015
Q. The entire lot of parts exhibit this condition. The curing is not related to the plating application. The parts leave the plater and return to the filter OEM and they temperature cycle the parts.
LeAnna Cody [returning]Quality Engineer - Albuquerque, New Mexico
July 28, 2015
A. Hi again Leanna.
Leanna, my first guess, is that this area is metallurgically different, perhaps just not as clean and active. I would suggest asking the plating shop to manually scrub a few parts with pumice and tampico brush, and see what they look like after plating and curing.
You might have some difficulty telling the plating shop that the lot is rejected unless you have some agreed upon visual standards. They might well feel that an unpolished part, full of nicks and scratches, with a dull tin-lead plating, is hardly a decorative part to be judged by variations in the darkness of the deposit :-)
Regards,
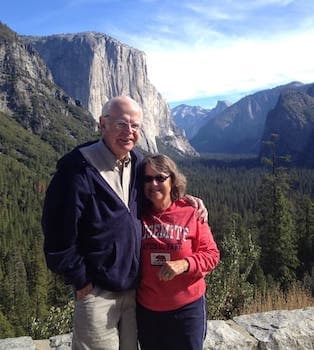
Ted Mooney, P.E. RET
Striving to live Aloha
(Ted can offer longterm or instant help)
finishing.com - Pine Beach, New Jersey
July 2015
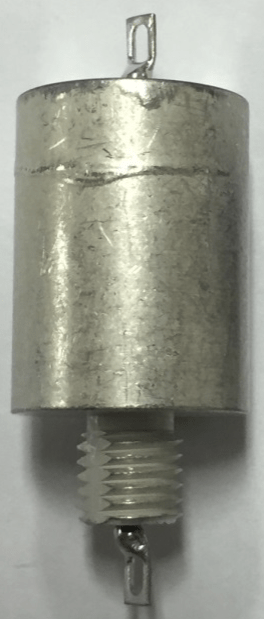
Q. The discoloration can be scrubbed off. But at the leading edge their is a ridge left over. The parts are very rejectable as we can not put pure tin parts into space. The specification is greater than 3% Pb. So, back to my question, can the difference in thickness, end-to-end, be attributed to "current density" in a barrel plated process?
LeAnna Cody [returning]aerospace - Albuquerque, New Mexico
July 29, 2015
A. Hi again. Yes, certainly you can reject parts that don't meet your specifications.
Thanks for the graphic. I'd better let another reader get "back to your question regarding difference in thickness end-to-end".
Regards,
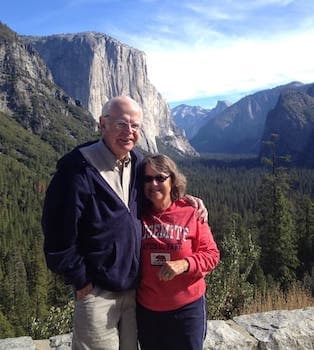
Ted Mooney, P.E. RET
Striving to live Aloha
(Ted can offer longterm or instant help)
finishing.com - Pine Beach, New Jersey
July 2015
July 30, 2015
Surely in almost all alloy plating, particularly in a barrel, the ends will get different current density from the middles and that will skew the alloy. This will be aggravated by the speed of the barrel rotation, faster is better for consistency.
Another problem here, maybe not related to alloy variation, but surely related to over all quality variation. You mentioned the part as "tubular". In that case, merely rotating in all the rinse tanks is not enough to clear the tubes of contamination - you must go in/out/in/out/completely in/completely out to flush out the inside of the tubes.
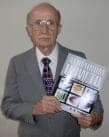
Robert H Probert
Robert H Probert Technical Services

Garner, North Carolina
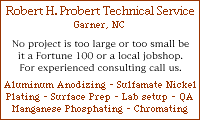
Antimony presence in tin lead solution
Q. Hello colleagues,
I want to ask you about a very strange situation that we had: How antimony element can inhabit lead plating on parts in tin-lead solution?
Thank you in advance,
- Israel
March 22, 2018
March 2018
Hi cousin Kati. I'm not sure exactly what you meant to say with "inhabit". Hopefully another reader will be more insightful than me.
Based on your several postings here, I'm guessing that English is your second language, and that you're encountering a little difficulty expressing yourself -- but that's actually a reason to be wordy rather than to be brief. Because nobody cares much if we misspell a word or if our sentence construction doesn't match the way they would write it, but we do care when we can't figure out the question :-)
You might mean "inhibit", i.e., that the antimony slowed down or stopped the reaction. To which I would have to say, where is the antimony coming from, how did it get there? Is it in the substrate which you are trying to plate with tin-lead? But you might be asking how antimony got into the plating solution in some unknown way, inhabiting it, in which case me asking you how it got there would be silly :-)
Please spend a few paragraphs trying to explain the problem in detail. Thanks!
Regards,
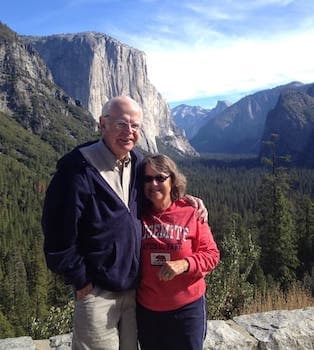
Ted Mooney, P.E. RET
Striving to live Aloha
(Ted can offer longterm or instant help)
finishing.com - Pine Beach, New Jersey
March 22, 2018
Q. Hello Ted, you are right, English is my third language.
I understood from your response that my question wasn't so clear, but you revealed what I mean by my question;)
My parts are on a base of argentum, and I plated them in a solution that is composed of SnPb in ratio 80:20.
On one of the days, Pb stopped plated on my parts. I checked Pb concentration and it was ok, but according to SEM analysis, we found antimony component and Pb was very low. Of course, I don't know what is the antimony source.
As I know from literature that antimony can cause a low tin content in the deposit. On my parts tin thicknesses are ok, but %Pb is very low.
Maybe you know additional reasons for Pb lack of plating on the parts?
Thank you again!
- Israel, Beer Sheva
A. Hi again.
I've tried off & on many times to learn Spanish, but didn't have the stick-to-it-iveness to achieve it. Thank heaven for people like you with the ambition to learn more than one language, or humanity would be divided up into isolated non-communicating islands. In the end, the word "inhabit" may be a good pun, because you mean both that it has come into the deposit somehow and you feel that it is inhibiting the deposition of lead.
Where the antimony is coming from is hard to determine except by examining the raw materials. Apparently silver-antimony alloys are not uncommon, so it could be coming from the substrate. But apparently antimony is sometimes added in small amounts to tin-lead alloy baths, and could be building up, or perhaps you just never looked for it before?
Although I know almost nothing about this subject, Brenner's "Electrodeposition of Alloys" gives some possible hints. For example, he notes that ingredients like peptone have almost no effect on the antimony content, but do drive the tin way up which means the lead has to go way down. My interpretation is that, although the source of the antimony is still an unknown, it may not in fact be responsible for the suppression in lead content.
Hopefully an experienced tin-lead plater will chime in.
Regards,
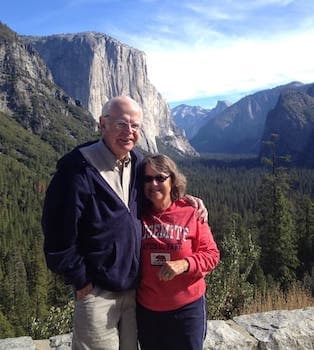
Ted Mooney, P.E. RET
Striving to live Aloha
(Ted can offer longterm or instant help)
finishing.com - Pine Beach, New Jersey
March 2018
Ted thank you again for your help! If I discover the antimony source or find the reason for the low percentage of lead, I will write here.
Kati M.
- Israel, Beer Sheva
March 23, 2018
A. I'm not sure where your antimony is coming from, but antimony will plate out preferentially to tin and lead. In fact, antimony may also immersion plate on the anodes and the tin-lead deposit. It also acts as a brightener in tin-lead plating. So, because it plates out preferentially, a one-time contamination should disappear fairly quickly, and if it persists, then it is probably not a one-time thing.
Lyle KirmanConsultant - Cleveland Heights, Ohio
March 27, 2018
Q, A, or Comment on THIS thread -or- Start a NEW Thread