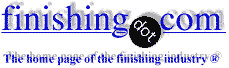
-----
Electroplating onto aluminum
Q. We need to electroplate an aluminum base plate for a client. The end use is at sea, so the corrosion protection needs to be very high. Also the client requires a conductive surface.
We have tried tin-nickel at 0.06 and 0.12 mil but it only lasted 50 and 100 hours respectively in salt spray. Not enough to make our client happy.
Our process is as follows: degrease, alkaline etch, double zincate, cyanide copper, acid copper (0.6 mil) and tin-nickel.
Can anyone suggest improvements or alternatives that will give us longer service life and better salt spray results without losing the conductivity?
Best regards,
Lars Jensen- Copenhagen, Denmark
2002
A. Have you tried chrome plating as last step? Do lab trials and evaluate for corrosion. Also try Duplex Nickel method.
Payal Mag- Charlotte, North Carolina
2002
A. Make sure the aluminium substrate is suitable grade for electroplating. You are right to use a double zincate system, or something similar. As suggested above, make sure you use a duplex nickel, but also make sure it is at least 5 microns thick, as this is about the minimum thickness needed to ensure a pore free layer. I like the idea of a chromium layer and wonder whether a hexavalent deposit would be better than trivalent; you can get thicker deposits with hexavalent chromium.
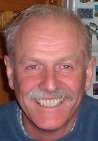
Trevor Crichton
R&D practical scientist
Chesham, Bucks, UK
2002
A. Hi Lars. You may be interested in listening to our podcast series "The Lost Art of Tin-Nickel Plating".
Just because you are not currently getting top salt spray results from tin-nickel plating doesn't necessarily mean it's the wrong process :-)
Regards,
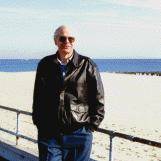
Ted Mooney, P.E.
Striving to live Aloha
(Ted can offer longterm or instant help)
finishing.com - Pine Beach, New Jersey
![]() |
!! I was looking into electroplating using aluminum and noted one response about using Hexavalent chromium. It should be noted that Hex Chromium is extremely toxic and a powerful carcinogen. It would be wise to use extreme protection when working with this chemical. I only FYI this in the event a novice should attempt to use this chemical. Robert Brandt- Franklin, Pennsylvania April 9, 2010 Hi, Robert. Yes, hexavalent chrome plating solution (i.e., chromium trioxide, i.e., chromic acid) is a strong solution of toxic hexavalent chromium and should be used only by trained people and in an industrial setting. I hate to quibble about warnings, but I would not attach the "powerful" adverb to "carcinogen", as I don't think the epidemiologists who determine carcinogeneity like to see us attach modifiers like "rather weak" or "super powerful" to their determinations. They have their protocols :-) Regards, ![]() Ted Mooney, P.E. Striving to live Aloha (Ted can offer longterm or instant help) finishing.com - Pine Beach, New Jersey August 21, 2011 |
Q. Unfortunately our client cannot accept nickel because of some high frequency conductivity issue. Otherwise we might have opted for a high phosphorous EN. But thank you for the suggestions.
Lars Jensen [returning]Galvanisk Kompagni - Copenhagen, Denmark
2002
A. Dear Friends,
Please pardon my ignorance but isn't anodized aluminum, especially hard anodized, enough for high salt spray test hours?
Just how high is your target corrosion protection? Does anybody have an idea why anodizing isn't ideal in this application?
Thanks,
Anthony Austria- Philippines
2002
Q. Thank you for the inspiration.
Hard anodize or chromic acid anodize would probably give us sufficient corrosion protection, but again our client needs a conductive surface.
We're beginning to wonder if it is at all possible to electroplate aluminum to a high corrosion protection? Without nickel?
Best regards,
Lars Jensen [returning]- Copenhagen, Denmark
2002
A. Sounds like it needs a heavy coat of gold plating, carat determined by corrosion resistance and effect of the alloy on the electronic properties.
James Watts- Navarre, Florida
2002
A. I plate on aluminum by zincate > copper > nickel (duplex or Tri) > coupled with chrome. For a very good finish, polish the copper lightly before nickel. The surface should come out brilliant and the corrosion resistance should be a minimum of about 300- 500 salt spray hours depending on how thick you plate the nickel.
Tan Kay Leongelectroplating works - Malaysia
2002
Hi Tan. Thanks for the informative posting which will benefit many readers even though Lars feels he isn't able to use nickel.
Regards,
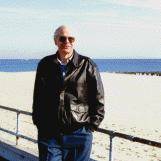
Ted Mooney, P.E.
Striving to live Aloha
(Ted can offer longterm or instant help)
finishing.com - Pine Beach, New Jersey
silly :-) You could always try a nice thick layer of platinum
Dicky MelvinsDicky Melvins' Independent Coatings - Brooklyn, New York, USA
October 11, 2017
![]() |
You can try to electroplate Aluminium from acidic ionic liquids such as [BMIM]Al2Cl7 ([BMIM]Cl/AlCl3<1). For two-electrode electroplating,you can choose Aluminum as an anode. During electroplating, the composition of electroplating bath does not change, but the setup should be kept under dry air or nitrogen condition. The dull or bright shinning finish can be achieved depending on the current densities, potentials applied or brightener used. F Qiu- UK January 30, 2008 September 2013 Hi F. Thanks but Lars wants to plate onto aluminum, not to electrodeposit aluminum. Regards, ![]() Ted Mooney, P.E. Striving to live Aloha (Ted can offer longterm or instant help) finishing.com - Pine Beach, New Jersey |
Q. Is it possible to electroplate an aluminum block on one side alone with silver?
Felix Rajstudent - Chennai, India
December 19, 2010
A. Hi, Felix. It's not only possible, it's fairly common.
You probably need to mask the side which you don't want plating on. Then you zincate, cyanide copper plate, silver strike, and silver plate. In place of the copper plating step you can alternately electroless nickel plate if you don't need nickel-free. Good luck.
Regards,
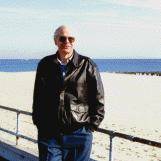
Ted Mooney, P.E.
Striving to live Aloha
(Ted can offer longterm or instant help)
finishing.com - Pine Beach, New Jersey
August 19, 2011
A. Without asking more about the details of the application or numerical limits, Radio Frequencies (RF), above a few GHz don't like ferromagnetic conductors (e.g.: Ni). Silver is not all that corrosion resistant in salt, even though it may pass salt spray, if thick enough. Also, it is soft, so it is not usually useful if there is mechanical abrasion.
The tried and true answer here in probably heavy Cadmium. It's also high on the toxicity list, probably undeservedly so, but it is available from specialized (read: expensive) electroplaters.
heavy trucks - Novi, Michigan, US of A
July 26, 2012
Q. I have aluminum gun parts I want to plate, not paint. Could I do so with copper then nickel under a DC charge? If so; in what acids do I dissolve the base metals? Would it be better to salt anodize? A little help, please.
Jon Neely- Winston-Salem, North Carolina, USA
September 24, 2013
A. Hi Joe. Anyone can do electroplating for a grammar school science project, it's dead easy, like plinking out "Twinkle Twinkle Little Star" on a piano. But robust industrial quality electroplating that will adhere and provide corrosion protection is more like "Rhapsody in Blue". And robust plating onto aluminum ... well, most professional electroplaters with years of experience have great difficulty with it.
If you want to do it yourself, I'd suggest electroless nickel plating. Go to a hobby plating site and investigate a kit for zincating and electroless nickel plating of aluminum ... and practice, practice, practice on scrap before risking your good parts. Good luck.
Regards,
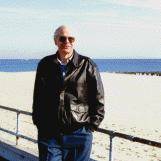
Ted Mooney, P.E.
Striving to live Aloha
(Ted can offer longterm or instant help)
finishing.com - Pine Beach, New Jersey
September 27, 2013
A. I may have found a solution to electroplating aluminium. It comes from a patent issued in 1899 to Frank S Leod:
https://www.google.com/patents/US630246
In 1895 he speaks of preparing it with hydrofluoric acid but he later patented a mercury step. I'm still looking into it but mercury does react to aluminium.
- Clearwater, Florida, USA
September 21, 2015
September 2015
Hi John. Thanks. But readers should be warned that hydrofluoric acid is about the most dangerous thing an electroplating professional deals with. Zincating seems to be a more practical (and certainly far more widely used) way to pretreat aluminum substrates in preparation for electroplating other metals onto them than mercury pretreatment.
Regards,
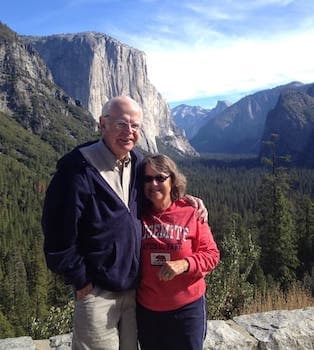
Ted Mooney, P.E. RET
Striving to live Aloha
(Ted can offer longterm or instant help)
finishing.com - Pine Beach, New Jersey
A. I would like to suggest that you should go for a Chromate Conversion Coating in combination with Anodising. Please respond to me whether I am wrong or right.
thanks
- kanpur,U.P, India
June 17, 2017
June 2017
Hi Devesh. Anodizing the aluminum or chromate conversion coating it, or partially anodizing and partially chromating it are certainly possible and are appropriate to some needs, in lieu of plating something onto it. Anodizing is insulative, chromating is sort of conductive.
Regards,
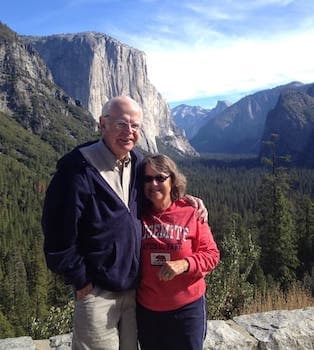
Ted Mooney, P.E. RET
Striving to live Aloha
(Ted can offer longterm or instant help)
finishing.com - Pine Beach, New Jersey
Q. Thank you for the reply sir. But please tell me, is my solution acceptable? Or you have got a better solution for the problem?.
Devesh Chawla [returning]- Kanpur, U.P, India
June 21, 2017
A. Hi again, Devesh. Yes, aluminum can be anodized and/or chromate conversion coated. But, sorry, whether that is better than the possible alternatives is hard to say unless we describe the parts and the application. You may be right that it's best for Jon's aluminum "gun parts" but I do not understand his situation clearly enough to say unequivocally. Thanks for participating and for your suggestion.
Regards,
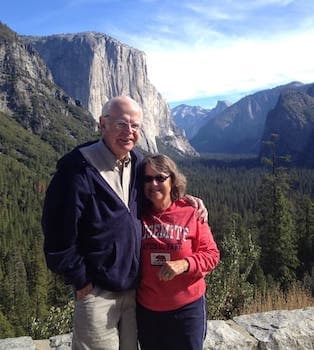
Ted Mooney, P.E. RET
Striving to live Aloha
(Ted can offer longterm or instant help)
finishing.com - Pine Beach, New Jersey
Electroplating on Aluminium
Q. I have 2 plants in India.
In my plant I process onto Aluminium only.
But there I am not using sulphate Chloride, but always density goes High and takes too much time to cover plating.
- Rajkot Gujarat India
February 25, 2019
March 2019
? Hi Bharat. I am not trying to hassle you but, sorry, I have no idea at all what you are talking about. Apologies.
Regards,
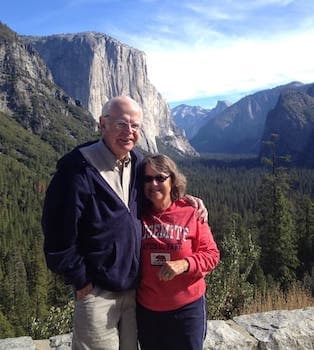
Ted Mooney, P.E. RET
Striving to live Aloha
(Ted can offer longterm or instant help)
finishing.com - Pine Beach, New Jersey
Q, A, or Comment on THIS thread -or- Start a NEW Thread