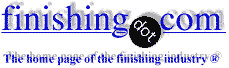
-----
Tin Plating Problems

this text gets replaced with bannerText
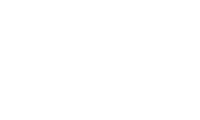
Tin is plated out of either an alkaline tin stannate bath or an acid bath (tin sulphate, tin fluoborate, or methane sulfonic acid /MSA). Each have their own advantages & disadvantages which we don't fully cover in this particular thread.
In the acid process the tin ions dissolve in the +2 valence state; whereas in the alkaline process the tin ions must be at the +4 oxidation state for the process to work correctly, but they have a tendency to dissolve into the +2 state.
Getting them into the +4 state requires careful control of the anodes, including 'filming' them. There is a lot of info on this stuff on the site, but understanding this specific necessity should help you search the site and follow the dialogs.
Q. Hi everyone! I am currently do tin plating service, and facing some problem. My tin plating product has thickness between 2 - 4 microns. It is a bright tin plating with sulfuric acid as the electrolyte.
My product is copper busbar plated with tin, the problem is rising when need to ship it to the customer in packaging inside a crate, stacked with several layer and wrapped in plastic transported using a truck. When the packaging is opened, as dark spots, like oxidation, appear at the second layer to the bottom in the period of 1 day (24 hrs).
Then, is it true that after tin plating without a passivation process, when the tin surface is rubbed with a tissue, black marks appear on the tissue? Is that normal, or should it not happen?"
Josafat MalauEmployee - Indonesia, East Java
September 4, 2024
by Larry Durney
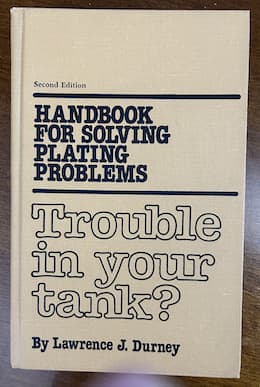
on eBay or Amazon
or AbeBooks
(affil link)
A. Hi Josafat
Fretting corrosion is certainly a very real problem with tin plating; thread 5106 illustrates terminals which turned completely black from fretting corrosion ...
Still, if parts got spots within 24 hours, it seems unlikely to me that it has do to fretting from tissue paper. I'd find at least 3 explanations more likely:
• 1. The plating is probably too thin; on the current page Lyle Kirman suggests more than doubling it.
• 2. Sulfur in the packaging is always a suspect when there is blackening, as expounded on by James Watts on thread 5106 -- and the stains seem to match the texture of the packaging, giving credence to this theory.
• 3. Tin must be properly rinsed as explained by Robert Probert on the current page.
Although you can try one thing at a time, you'll never fix it that way if there are two things wrong :-(
-- which is a good example of why this advice from Lawrence Durney in "Trouble in Your Tank" ⇨
is priceless: 'Follow the Letter of the Law' -- i.e, increase the plating thickness so it is more robust, rinse the parts properly, and carefully choose the correct packaging material. Do them all, not just one of them, and only after the problem is solved should you, one at a time, try to simplify or economize :-)
Luck & Regards,
Ted Mooney, P.E. RET
Striving to live Aloha
(Ted can offer longterm or instant help)
finishing.com - Pine Beach, New Jersey
⇩ Related postings, oldest first ⇩
Hobbyist has tin plating problems
Q. I'm presently making some little shields out of copper sheet for a printed circuit board and would like to know what I should spec for a finish. I made a box for a power supply before out of 22 GA steel and specified just a straight tin plate. I did this because I wanted to solder the box together. The plating seemed to come back fine and the box assembled well. Since I always find finishing one of the most confusing parts of any project I was hoping that this web site could be a source of information for me in the future. I have been told that maybe a hot tin plate would be better. What is the difference between hot tin and just tin? Did my steel box have to go thru extra plating steps to be tinned? Was there a better finish I could have used? As you can see, I have lots of questions and I would surely like to have a place I could get answers. My next project is using some perforated steel sheet so I will need to plate it too! Any comments or help greatly appreciated. Peter
Peter Chapman1995
A. Tin plating of electronics, and for solderability, can be a specialized field, and is one where my hands-on experience is limited, so I hope that some reader more knowledgeable on this than I will jump in and straighten us both out!
But I understand that there has been some movement in the Far East towards applying tin by hot dipping (into molten tin) as opposed to electroplating, for reduced cost and improved solderability. Another technique, I believe, is reflow--where the tin is electroplated, but then heated to the melting point for grain refinement.
Practically speaking though, electroplated tin is a fine finish, readily available, and I don't know of any job shops that offer hot dipped tin anyway. For onesy-twosy applications, if your tin solders well, I don't think you need additional steps.
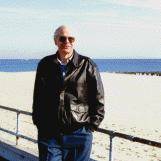
Ted Mooney, P.E.
Striving to live Aloha
(Ted can offer longterm or instant help)
finishing.com - Pine Beach, New Jersey
A. While tin electroplate is fine, electroless tin on copper usually provides sufficient corrosion resistance and solderability at reduced cost to electroplating. Hot dip tin is fine for large quantities. For onesy/twosy parts, hobby quantities of electroless tin solution (1 pt / 1 qt) can be purchased off the shelf from many electronics / project sources. There is an electronics oriented chemical company (photoresists/etchants/tuner cleaner/etc.) out of Canada that produces and markets an electroless tin solution that is available in the US
Jeff Albom- El Granada, California
1995
Ed. note: That company out of Canada is, we believe, out of business. We think their successor is dalpro.net. But you can get electroless tin plating solution in small volumes from Amazon.
and probably elsewhere.
A. Hot dip tinning of very small electronic parts was performed in a captive shop in New Jersey about 10 years ago. And it was a performance requiring skill and grace. The scrap rate was much less than 1/2 of 1%. If done poorly, you could have scrap of 10 to 15% with no problem.
Regards,


Tom Pullizzi
Falls Township, Pennsylvania
2001
Q. I'm from a company in South Africa. Tin plating is one of the new ventures that our company started and needless to say we have a few problems and I wonder if someone could shed some light on some of my questions. We are plating onto copper and brass respectively (with tin). Please try and answer the questions as laboriously as possible.
1. How do other companies get their current onto their strip of metal?
2. The top and bottom of the strip will have a different thickness of tin. Why? We use Titanium baskets, and the strip runs horizontally.
3. Our passifier discolours the strip. Are there other types that we can use?
4. We used copper cyanide in one of the baths, it was suggested to leave it out of the process. Now the plated metal discolours (goes black). Do you suggest putting the copper cyanide back into the equation?
5. Is temperature control very important? Why?
6. The 'whiskers'-issue. How, why, how to get it away?
7. What is the voltage required on what thickness of strip?
8. After plating and a few hours has past the plated metal starts to turn black. Why and how do I prevent this?
I know these questions must be elementary to you, but it will help us a lot if you could answer some of them, without getting too frustrated!
Thank you,
Aletta Renee van der Vyver- Johannesburg, Gauteng, South Africa
2002
A. Aletta,
Sounds like you having a lot of difficulties. Let me try to help you with your questions one by one.
1. Pending the type work you have your choices are to rack plate with rack to connect the work on to, barrel plate using steel media for electrical contact, or get electroless or immersion plating bath. However, electroless/immersion tin baths require very specific conditions to operate and are not widely used and may not get the plating thickness that you want.
2.Your different in plating thickness is caused by top part of your strip is a high current density area compare to the bottom. This means the top part wants to plate faster. Try increasing the distance between the anode basket and your work. This will reduce your thickness difference. A thick copper under plate and lowering your plating current may help in this area also.
3. Can't help here.
4. If you are using copper as a strike to help your adhesion, leave this step in the process.
5. Temperature control is important pending on the bath. A high operating temperature will improve your plating rate with baths that are alkaline based. However, acid tin baths do not like too high operating temperature and prefer to be operated at room temperature.
6. There is a lot information published on tin whiskers. A good book on the subject is "Soldering in Electronics" by R.J. Klein Wassink ⇨
Tin whiskers growth occurs only with pure tin under certain conditions such as long term storage with high humidity. Tin-lead alloys, bright tin, and I think reflowed tin is not prone to whisker growth.
7. The best method to set-up your plating parameters is current and time. Set your current per the surface area of your work. For example, 2.5 to 4.0 amps/dm2. A few trials you can determine a plating rate vs current and time. Note there are other variables that will affect your plating rate such as solution metal concentration, temperature, acid or caustic concentration, bath contamination, and so on. Also note the fast plating rate is not always the best. I seen too many people who use the maximum plus current to get the work out. In the end, they generate poor quality work, rework, and scrap.
8. What you may have is tarnishing of your work. Be sure you have good rinsing and drying after plating. The more rinsing the better.You could try an alcohol dip before drying to remove water on or in the plating surface.
I hope this helps and good luck.
Karl Weyermann- Lebanon, Kentucky
A. Hi,
Top and bottom will have different thicknesses. Lowering the Current can improve the variance. Or using shields might help. Cathode part nearer to anode basket tends to get higher thickness. Shielding some part of cathode with non-conductive material will reduce thickness.
Voltage can be calculated using Faraday's Law.
Rinsing your product using deionised water before drying using hot air will reduce discoloration.
- Lebanon, Kentucky
November 19, 2014
Q. I am also retired and would like to play around with tin electroplating some Scripto UV lighters and some very small hand size metal steel boxes--I already bought the two bars of tin and also have a 5 AMP 32 Volt variable voltage & power --DC supply with digital readouts.The plating would be done outside under a roof overhang.
What dry electrolytes should I get that do a nice job without calling in the HAZMAT people to a private house.
Thank You ,
Mark
- Staten Island, New York
October 9, 2012
Q. Hi, I'm currently looking for solution to resolve dull or black plating in barrel for tin plating. Can anyone brief or explain the aspect or reason which can contribute to this dull plating or any recommendation to solve this problem
Navaletchumy d/o Vijaya kumaran- Seremban, Malaysia
October 18, 2018
A. Hi Navaletchumy. Please try to give us some starting points :-)
Are you doing alkaline tin plating or bright acid tin? Could the dullness/blackness be fretting corrosion from prolonged tumbling? Have you done any Hull Cell ⇦ huh? testing? Do you have any photos to show us what you mean by 'dull or black'. Is this a problem which just occurred for the first time, or does it come and go, or is this a new plating line which has not generated proper parts yet.
Most plating texts will introduce you to troubleshooting the process. The Canning Handbook [on eBay, Amazon, AbeBooks affil links] says dull deposit (in Bright Acid Tin) bath may be due to excess chloride, lack of brightener, temperature too high, sulfuric acid concentration too low, anodes passive, current density too low, metal concentration too high, or suspended solids. Good luck.
Regards,
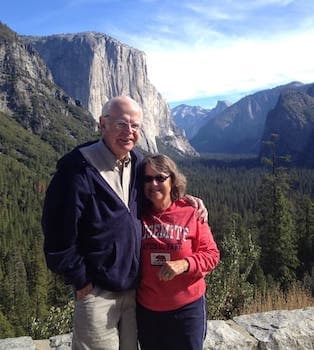
Ted Mooney, P.E. RET
Striving to live Aloha
(Ted can offer longterm or instant help)
finishing.com - Pine Beach, New Jersey
Cracks in tin plated surface
Q. We have a problem with our tin plated surface. We have cracks in the plating.
We are doing a nickel strike and nickel layer before tin plating (to avoid tin whiskers).
Meanwhile we changed already our cleaning bath, HCl bath, nickel strike and nickel bath. And now we can only change the tin bath anymore to hopefully solve our problem.
Is there a possibility to analyse our liquid to avoid this problem in the future? Tin bath is methanesulfonate bath.
May 21, 2019
HTMS - Mechelen Noord, Belgium
A. Hello Kristoff, you didn't mention if the bath contained organic brightening agents. A high level of organics in MSA tin plating will cause internal stress of the deposit. This is true with both brightened and matte baths.
Mark BakerElectronic Plating - Winston Salem, North Carolina USA
A. We are doing a MSA dip and we have Argophan Brightener T and brightener in the bath too.
Kristoff De Backer [returning]HTMS High Technical Metal Seals - Mechelen Antwerpen ,Belgium
Q. Hi guys I received water mark and stain issue continuously in my plating process. Anybody help to solve the issue?
vasan srini- Chennai, India
October 11, 2019
A. Hi Vasan. I'm sure the readers will be happy to try to help but it's still a bit vague. We don't know if this is a one-time hobbyist problem or a long-running factory problem, or whether it's acid, alkaline, or MSA zinc; or what the substrate is; or anything about your process cycle; or the quality of your rinsing. Please give us a paragraph or two of introduction & detail, and send pics for posting here to mooney@finishing.com if you can. Thanks!
Regards,
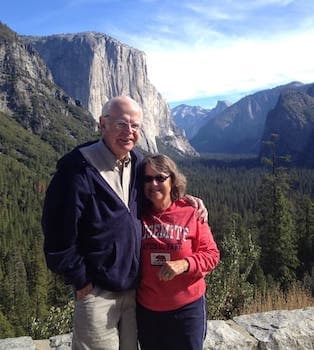
Ted Mooney, P.E. RET
Striving to live Aloha
(Ted can offer longterm or instant help)
finishing.com - Pine Beach, New Jersey
Q. We are doing bright acid tin plating process of 3-4 micron on steel and brass components with undercoat of copper 3 micron.
Within a week, tin plating turns dull & black.
Please suggest remedy.
- Nagpur Maharashtra
June 17, 2020
A. Hi Pankaj. It might be best if you describe the process sequences that you do on steel and brass substrates separately because we quickly get into confusion when they are merged...
For example: why are you copper plating the steel before tin plating, and what copper plating process are you using (cyanide, pyrophosphate, proprietary alkaline)? It sounds like it might be introducing more problems than it prevents :-)
What are these components? Are they highly polished before plating? If not, 3-4 microns strikes me as rather thin.
Regards,
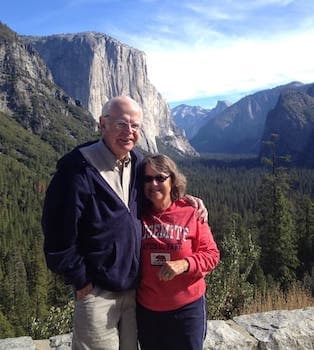
Ted Mooney, P.E. RET
Striving to live Aloha
(Ted can offer longterm or instant help)
finishing.com - Pine Beach, New Jersey
Q. Hello sir,
Thanks for response.
For steel components:
Degreasing in solvent - Rinse - Derusting in dilute hydrochloric acid - Rinse - Bright acid tin plating process consists of sulfuric acid+stannous sulphate+brighteners - Rinse - Dip in hot 1% dilute NaOH sol'n - Hot oven dry.
For brass components all same operations except Derusting (as brass doesn't need Derusting).
Proprietary alkaline copper plating (3-4 micron) as undercoat before tin plating on both brass & steel.
Components are threaded & small. Tin plating of 3-6 microns to be done.
After plating, gauge to be checked as inspection criteria.
Within a week, tin plating turns dull & black.
Please suggest remedy.
- Nagpur Maharashtra
A. Hi Pankaj. I certainly haven't seen all possible workable processes, but I've never heard of electroplating onto brass without an activating dip in mild acid, and I've noy heard of electroplating either steelwithout alkaline cleaning first. It surprises me that your plating has been exhibiting satisfactory adhesion.
As for the blackness developing in a week however, I would strongly suggest sulfur
⇦ on
eBay
or
Amazon [affil link]
in the packaging or the environment and especially because the tin plating over the copper is very thin. Thread 5106 is specifically about tin plating turning black and should offer further food for thought.
Regards,
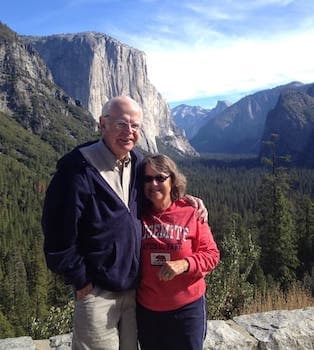
Ted Mooney, P.E. RET
Striving to live Aloha
(Ted can offer longterm or instant help)
finishing.com - Pine Beach, New Jersey
A. I routinely plated both acid and alkaline tin on steel and brass and bronze parts at a thickness of 0.0002-0.0004" [5-10 µm] with good shelf life and no darkening. I think you need a thicker tin plate.
LK
- Cleveland Heights
A. Just a thought. The tin thickness is very low and tin has a propensity to migrate into the base substrate to form an intermetallic compound if the base is copper or iron/steel. In the case of steel, the intermetallic compound is a grey colour and can be easily seen in tin cans, especially when the can has been opened and left exposed to the air for a day or so. If the contents are acid (say pineapples) you will see a dull grey ring around the meniscus - this is due to the tin being dissolved and exposing the intermetallic compound. I note that this enquiry is from the hotter climes and wonder if the thin layer of tin is diffusing into the base...
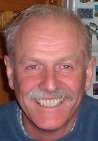
Trevor Crichton
R&D practical scientist
Chesham, Bucks, UK
A. All of the above two reports PLUS, all tin plating solutions do not "rinse" off, you must go back into a mild cleaner to remove the tin plating solution, then rinse again, then it will not turn black in two weeks.
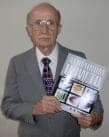
Robert H Probert
Robert H Probert Technical Services

Garner, North Carolina
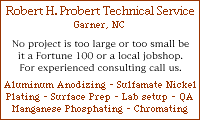
Q. Good morning,
I have been struggling for some time where steel components are copper plated and then tin plated.
The problem is that we experience random small blotches where the plating does not take on the part. This we obviously ascertain shortly after putting a charge in, we then have to scrutinize each part and ones with the blotching we wipe with 00 steel wool
⇦ on
eBay or
Amazon [affil link] /wire brush and return to tank.
The blotching is random, and small in HCD and LCD.
I can only assume that it would be a problem in the Cu. (oil on surface perhaps?) which may stick to component resulting in the blotching.
How can I regularly clean the surface of the Cu. The pre-cleaning/rinsing is meticulous, however this is my last resort.
Many thanks in advance
- JOHANNESBURG/SOUTH AFRICA
May 13, 2021
Q. We are facing problem in tin plating process. We are loading 8 copper plates in 1000 ltrs tin bath. First part and last observed dull plating in high current area. We need to solve this issue; please give your inputs.
Ananda babu- Chennai Tamilnadu India
August 6, 2021
A. Hi Ananda. Sorry but I'm not really following this description. Is one plate plated at a time, or are all 8 plates put into the tank before plating? Acid or alkaline plating? A pic to mooney@finishing.com for posting here would sure help :-)
Luck & Regards,
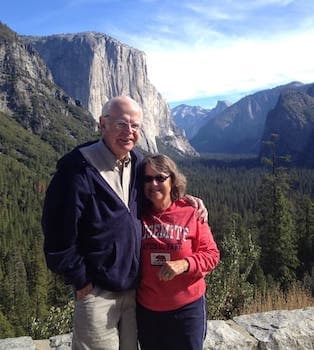
Ted Mooney, P.E. RET
Striving to live Aloha
(Ted can offer longterm or instant help)
finishing.com - Pine Beach, New Jersey
A. AFTER YOU RESPOND TO MR. MOONEY'S QUESTIONS, THEN, IF ALKALINE TIN, BE AWARE THAT THE SOLUTION IS EXTREMELY SENSITIVE TO COPPER CONTAMINATION. A SEPARATE TIN "STRIKE" WOULD PAY FOR ITSELF BY PROLONGING THE MAIN PLATING SOLUTION.
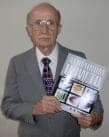
Robert H Probert
Robert H Probert Technical Services

Garner, North Carolina
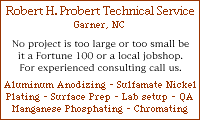
Q. While plating brass material with tin, it get curret's black spots. What's the solution?
Jay GholapElectro plater - Mumbai Maharashtra
April 27, 2024
A. Hello Jay,
"Curret's" is apparently a typo or a bad autocorrect. Please tell us what you meant.
Also please let us know what kind of tin plating process you are running -- stannate, acid, MSA -- and whether you are rack, barrel, or continuous plating, and what (if any) post treatments you are doing. The readers are probably willing to help but usually don't want to spend time introducing a dozen ifs-ands-&- buts that are not applicable to your situation.
Tin plating is highly susceptible to "fretting corrosion" and can therefore get black spots from handling when nothing is wrong with the plating. Thanks!
Luck & Regards,
Ted Mooney, P.E. RET
Striving to live Aloha
(Ted can offer longterm or instant help)
finishing.com - Pine Beach, New Jersey
Q, A, or Comment on THIS thread -or- Start a NEW Thread