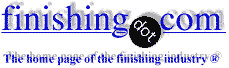
-----
Nitriding Process
Q. We are manufacturers of jobs requiring case hardening and we are doing it successfully . We wish to start nitriding process also but we don't have any idea of the process of nitriding surface hardness. We request you to please inform the nitriding process on jobs with dimensions of 100 mm max on all sides.
We shall be thankful if you could provide us the required information at the earliest.
Thanks,
- Raipur, Chattisgarh, India
A. One option for parts of that size is salt-bath nitriding as offered by Kolene. Pranchal. There is an excellent paper in our on-line library about the Quench-Polish-Quench method. But there is also gas nitriding and plasma nitriding. Good luck with it.
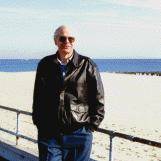
Ted Mooney, P.E.
Striving to live Aloha
(Ted can offer longterm or instant help)
finishing.com - Pine Beach, New Jersey
Nitriding process description
Q. I need the answer to this question: Nitriding process description.
raakesh tailor- Mumbai, maharashra - India
May 16, 2008
A. Hi, Rasskesh. There is gas nitriding (ammonia nitriding), and salt bath nitriding (liquid nitriding), and plasma nitriding (ion nitriding), and each can have a number of different variations and process descriptions, but the Wikipedia article we linked to may meet your needs for a very brief intro to all of them. There are also PVD processes for additive nitride layers like titanium nitride or zirconium nitride.
If the Wikipedia article we referenced, and the article on the Quench-Polish-Quench process doesn't suffice for your assignment, you can search this site for dozens of additional threads on those subjects, but I think you'd be better off going to a local or university library for good nitriding books for the particular nitriding process which interests you. Best of luck.
This public forum works quite well either at steering people in very general directions for further study, and at the other end of the spectrum it is good for helping to find solutions to highly specific questions. Unfortunately, this makes the public forum inherently rambling and disorganized; so for organized tutorial focus it is no substitute for books on the subject :-(
Regards,
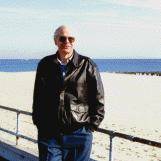
Ted Mooney, P.E.
Striving to live Aloha
(Ted can offer longterm or instant help)
finishing.com - Pine Beach, New Jersey
May 16, 2008
Q. What are the characteristics of Tuftride and each of all of the different nitrides, i.e., gas, ion, etc.
When bragging about nitriding benefits, does "improve fatigue life" mean the life of the wear surface or the entire object ? I.e., does it mean the entire crankshaft or just the journals? How can nitriding make a crankshaft less prone to breakage, or will it ?
aviation - Naples, Florida, USA
2006
A. Each nitriding and nitrocarburizing process has advantages and costs. Traditional gaseous and salt bath processes require suitable alloys and higher temperatures for thermal diffusion. Plasma-assisted ion can harden more alloys and utilize lower temperatures but requires vacuum-tight equipment.
Additional, proprietary procedures (e.g., quench-polish-quench, pre- and post-oxidation) are often used with the AMS2753 salt bath processes to minimize surface brittleness and improve other properties.
A reduction in surface-initiated cracking improves fatigue life. The surface is stronger, more wear-resistant and may have lower residual stress than other hardening processes.
The subject is vast. Many good books are available, including:
- Practical Nitriding and Ferritic Nitrocarburizing
⇦[this on
Amazon affil links], ISBN 0871707918 (2003),
- Surface Hardening of Steels: Understanding the Basics
⇦[this on
Amazon affil links], ISBN 0871707640 (2003), and
- The "Surface Hardening Treatments" chapter in Physical Metallurgy Handbook
⇦[this on
Amazon affil links], ISBN 0070579865 (2002).
- Goleta, California

Rest in peace, Ken. Thank you for your hard work which the finishing world, and we at finishing.com, continue to benefit from.
Multiple threads merged: please forgive chronology errors and repetition 🙂
Types of nitriding processes
Q. Hi I have a doubt in nitriding and gas nitriding ... first of all I have to know is there any difference between nitriding and gas nitriding?
If yes, explain about the process if any one could.
Heat Treatment-GM - Coimbatore, Tamil Nadu & India
August 15, 2008
A. Hi, Saba. We've appended your inquiry to a thread on the subject. I have heard of three types of nitriding: gas, plasma, and salt bath. Whether the word 'nitriding' without the use of the word 'gas' implies 'gas nitriding' is one of those difficult or impossible to answer questions, but I would say no because if a fellow has been brought up in a plant that does salt bath nitriding, he is going to start using the shorter version and call the process 'nitriding', and to him 'nitriding' implies salt bath nitriding :-)
Regards,
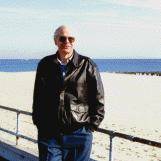
Ted Mooney, P.E.
Striving to live Aloha
(Ted can offer longterm or instant help)
finishing.com - Pine Beach, New Jersey
August 15, 2008
A. Plasma nitriding is a high tech process invented just a few years ago. Very expensive (six digit?) vacuum equipment, very clean, most controllable, superior layer, mostly used for critical items produced in large scale such as automotive parts. Low risk to environment.
Gas nitriding uses sealed vacuum reactors which are filled with gaseous ammonia
⇦ on
eBay or
Amazon [affil link] once the charge has been introduced and heated. Also very clean, but slower and less controllable, mostly used for less critical average quality items in large scale. Medium risk due to possible leaks of ammonia.
Salt bath nitriding uses a bath of fused ammonia salts where the charge is immersed. No need for vacuum or complicated electronics. Least expensive equipment, product comes out dirty, least controllable. Mostly used to process a diversity of low volume parts.
Monterrey, NL, Mexico
August 20, 2008
RFQ: We used to use a company that did some sort of two stage gas nitriding for some bending clamps we machine. This company is no longer in business and nobody knows for sure what process was being used exactly. We are attempting to find someone to duplicate this process but with no luck as of yet. Plasma and salt bath nitriding so far are not allowing the grip our clamps with serrations need to bend stainless steel tube. I am desperately looking for a solution.
Thank you
Mike
Machine shop supervisor - Portland, Oregon, USA
July 17, 2009
Ed. note: This RFQ is outdated, but technical replies are welcome, and readers are encouraged to post their own RFQs. But no public commercial suggestions please ( huh? why?).
The custom search engine will reveal dozens of detailed discussions on every nitriding process.
Nitriding vs. bluing for hoof picks
Q. I have been trying to find stats on the benefits of nitriding vs. just something like stainless steel or bluing. I am not a metallurgist, and would like some simple to understand data. I was looking at possibly treating some of my steel hoof picks so they will hold up better and not rust. Any help is much appreciated.
Ryan Geigerhobbyist - Delaware, Ohio
March 26, 2014
A. Hi Ryan. "Nitriding" covers a wide variety of processes as described above, but all would seem to be out of the range of a hobbyist. Although nitriding can impart a good degree of corrosion resistance, it's main function is hardening to reduce wear. I know little about hoof picks, but that doesn't seem to me to be a principal consideration. Bluing (black oxiding) is a process with very little corrosion resistance, used on things that are lovingly cleaned, and waxed or oiled like rifle barrels. Surely stainless steel would be the most rust resistant material. Good luck.
Regards,
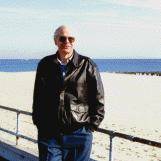
Ted Mooney, P.E.
Striving to live Aloha
(Ted can offer longterm or instant help)
finishing.com - Pine Beach, New Jersey
March 2014
A. Ryan,
My first question is, what is the hoof pick made of to start with? If it's a really nice one, just make sure to keep it cleaned and oiled. If it's going to be in storage for a longer amount of time consider applying a paste wax to it.
Blacksmith - Lenoir, North Carolina USA
May 5, 2014
Q, A, or Comment on THIS thread -or- Start a NEW Thread