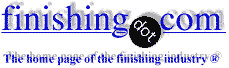
-----
Must we oil BLACK OXIDE finish?
Q. Are there any standards commonly referenced for oiling of parts after the black oxide treatment? I did not see oiling mentioned in the standards listed in the black oxide specifications & standards page. If oiling is necessary after the black oxide, I would like to give the vendor the proper amount of information. Is "... & coated with dry-to-touch oil" sufficient?
Henry Wallace- Lexington, Kentucky
September 9, 2024
A. Henry:
Oiling is absolutely required after black oxide. If you don't specify I would expect a service shop to apply their "standard" oil.
Most customers either go with an "oily" feel or as you mentioned "dry to the touch". If you have a preference I would supply that to the vendor.
A more in-depth answer may include how much protection it provides typically measured in salt spray hours or humidity chamber testing. These numbers don't necessarily guarantee performance in the real world but are useful to compare oils vs one another.
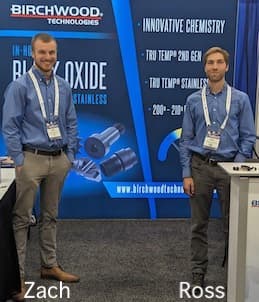
Zach Johnson
Birchwood Technologies

Eden Prairie, MN
⇩ Related postings, oldest first ⇩
Q. Our company recently started investigating the use of black oxide as a rust preventative finish on some steel pivot bushings. When we got past the one and two part sample stage, our shipments had a thick sticky oil all over them. From what I can read, the oil is what prevents the rust. Oil is what we don't want because it will attract dirt and promote wear in the steel on plastic pivot.
I'm getting cold feet. I'm wanting an oil free finish that will retard rust while the part is new. A robust long term finish is not required. Is there a black oxide variation that we need to specify? Another finish altogether? (with similar costs).
Bruce Peterson- Assaria, Kansas
2001
A. It sounds to me like your vendor used an oily finish oil. Not all oils will leave that tacky residue. Some oils are formulated to leave a dry-to-the-touch finish so as not to attract dirt once the part is in service. You may also want to look at using a water soluble oil that when mixed properly will leave a dry finish. Oh yeah, you do need to put some sort of rust prevent on the black oxide because the coating itself will only give minimal (1-2 hrs) salt spray corrosion resistance. With a good oil, you can easily get in excess of 80 hours salt spray resistance.
Dan Brewerchemical process supplier - Gurnee, Illinois
A. Hello Bruce,
I am assuming your parts are steel and yes it is the oil that provides the corrosion resistance on Black oxide coating for this material. Stainless will blacken does not require the oil, and the processing costs are similar to processing black oxide for steel. Other processes (black zinc, nickel etc..) are usually more expensive and alter the part dimensionally.
Good luck,
Bill Grayson- Santa Cruz, California, USA
A. Bruce, typically an oil is applied to black oxide coatings to enhance its rust protection. The type of oil and the amount applied will determine if the treated parts are wet or sticky. The parts you received appear to have been treated with a viscous oil that makes them sticky. I suggest you contact the shop that applies the black coating and see if they could apply less of a lower viscosity oil. This type of oil will provide less rust protection than the current material but it help you to meet your performance goal of not allowing dirt to stick.
We typically recommend applying a water dilutable rust preventative oil over black oxide. That way, by increasing or decreasing the concentration of the oil in the water, we can vary the amount of oil deposited on the parts. At low concentrations, the treated parts are dry to the touch and will not collect dirt.
Roy NussTrevose, Pennsylvania, USA
Multiple threads merged: please forgive chronology errors and repetition 🙂
Q. We are having trouble with oil residue building up in feeding tubes for auto screw guns. We are currently using black oxide screws. Do black oxide screws have an oil residue? Do black phosphate screws have an oil residue?
Dale Higdonoffice furniture manufacturer - Muscatine, Iowa
2003
A. It is common to apply an oil based corrosion inhibitor to both black oxide and phosphate parts. Without this corrosion inhibitor, it is very likely the parts would develop rust while in transit or storage. If the screws are causing an oil residue to form in the screw gun tubes, your supplier may be applying too much oil or using a material that leave the screws too oily. My suggestion would be to request that your vendor apply less of the rust preventative to the parts.
Roy NussTrevose, Pennsylvania, USA
A. Or you could request that the screws have a water soluble wax applied to them after Oxide versus the oil. I have seen this done in the past when oil is not acceptable with great results.
Chad Autrymetal finishing - Albuquerque, New Mexico
A. One more possibility is that the screws you are using have been "cold blackened" rather than receiving a true black oxide finish (see our FAQ on black oxide). Cold blackening has some advantages, but the finish is invariably very smutty because it's not a true oxide coating but a selenium smut that rubs off more readily than a true black oxide.
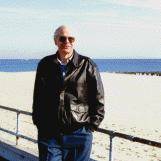
Ted Mooney, P.E.
Striving to live Aloha
(Ted can offer longterm or instant help)
finishing.com - Pine Beach, New Jersey
Multiple threads merged: please forgive chronology errors and repetition 🙂
Q. We are making a small stamping part with material 0.508 mm thick high-carbon spring steel 65Mn. The finish requires Black Oxide and parts must be dry. The part is assembled by hand, and it sticks somewhat to the fingers when assembling although the part looks dry. I don't know if this situation right, and can it be as dry as a part with finish Zinc plating surface?
Bill WangElectronics mfgr. - Dalian, Liaoning, China
2006
A. Unfortunately, that goal is questionable, Bill. It is the oil not the black oxide that provides the corrosion resistance. The oil can be very easily removed with a solvent, but the parts will rust almost instantly.
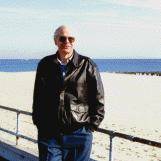
Ted Mooney, P.E.
Striving to live Aloha
(Ted can offer longterm or instant help)
finishing.com - Pine Beach, New Jersey
Q. Ted,
Thank you very much for your answer to my question.
If it is the oil only to act the corrosion preventing function, what's the function of black oxide, because once I thought we would not oil the part if the customer didn't like the oil.
Actually, we have delivered some parts to the customer, and they intend to ask a vendor to remove the oil by a process with wood chips and ultrasonic. And the customer showed me some black oxide parts from other vendors, and it is really very dry and seems no oil on the parts. Just the parts look not bright.
I find out complete notes on the drawing concerning finish: Black Oxide - Water displacement compound ES (Hubbard-Hall) dry finish. Parts must be dry. Corrosion protection level to pass 5 hrs salt spray test per ASTM B117 -03. Red corrosion at sharp edges/corners on part is acceptable. Parts must be dry and clean, will be rejected if any oil still wet or sticky found on part.
So I think I am still in trouble with it, and need further help.
Best Regards,
Electronic mfgr - Dalian, Liaoning, China
2006
Bill,
Many black oxide chemical suppliers also sell dry-to-touch oils and waxes which can be used instead of 'oily' oils. Sometimes called rust preventatives.
- Goleta, California

Rest in peace, Ken. Thank you for your hard work which the finishing world, and we at finishing.com, continue to benefit from.
RFQ: Bill,
Can you let me know who can supply that dry-to-touch oil in your area please, if you have got it? I happen to have a supplier in your area who needs the same help.
thanks in advance
August 8, 2008
Ed. note: This RFQ is outdated, but technical replies are welcome, and readers are encouraged to post their own RFQs. But no public commercial suggestions please ( huh? why?).
Multiple threads merged: please forgive chronology errors and repetition 🙂
Q. We are using a ballscrew that has been black oxide treated and oiled after. We need a grease instead of oil on the ballscrew and ball nut. Are there any problem to expect because of removing the oil and coating with grease? Will solvents affect the black oxide?
Thanks,
Using a product that has been black oxide treated and oiled - Falls Church, Virginia
March 18, 2008
A. I think that you can get by with just wiping it down with shop cloths or high quality paper shop cloths. If you use a solvent, you have a disposal problem.
James Watts- Navarre, Florida
A. Although there are many types and weights of oil and many types of grease, as far as I know the only difference is that the grease contains a fat or soap to keep it in place. I don't think that can hurt the black oxide coating; I don't think ordinary solvents have any effect on it either.
I am a little surprised that a wear surface like a ball screw would have a black oxide coating since it's not very durable. Sure it's not a salt bath nitriding (which is also black)?
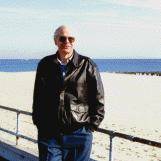
Ted Mooney, P.E.
Striving to live Aloha
(Ted can offer longterm or instant help)
finishing.com - Pine Beach, New Jersey
Multiple threads merged: please forgive chronology errors and repetition 🙂
Q. Hello,
We had 50,000 leg glides with a black oxide finish manufactured for us overseas and when they arrived they were oily to the touch. Our customer for this item installs them on (along with other components) office partitions that are covered with fabric. They cannot use these glides as they are because the installers will get the excess oil on their hands and it will be transferred to the fabric as they assemble.
Can you advise the most efficient and economical method to clean or dry these glides out so they are dry to the touch?
Many thanks.
Hardware Components - Danbury, Connecticut
November 17, 2009
A. Hi, Brian. You cannot leave them without oil or wax or they will flash rust in hours. You need to get the oil off in a solvent (maybe a vapor degreaser) and immediately apply a wax or dry-to-the-touch oil. Let a plating shop try a few dozen and see if they solve the problem. Maybe they are salvageable without redoing the finish completely.
Is the "oil" essentially transparent or is it sooty? I hope it's real hot black oxide, and the oil is clear, because if it's a selenium-based cold blackening process rather than true hot black oxide, I doubt the batch can be made smut-free without complete stripping and re-processing. Good luck.
Regards,
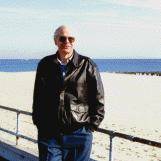
Ted Mooney, P.E.
Striving to live Aloha
(Ted can offer longterm or instant help)
finishing.com - Pine Beach, New Jersey
A. I have seen so many people try to use black oxide on furniture and other house hold goods and it just never works. Black oxide or blueing is a finish that is to be used on toys like guns or musical instruments that will be babied or on items like gears and bolts that will live their lives in an oil or grease environment. Yes 200 years ago it was a GREAT rust preventative but it was only great because people had nothing better!
With today's mad scientists we have all sorts of platings and polymers that have made blueing virtually obsolete. I do have to admit that I still do see blueing used in decorative environments but the way it is protected has also gone the way of the polymer revolution and for good reason.
The four things which destroy blueing are air, water, handling and acids. Air and water are hard to escape from. They are all around us at all times and they are in our bodies as well.
Oxygen of course is the real killer that is found in both of these things. In plain simple English oxygen combines with iron and makes rust. No chemical explanation needed here everyone of us has seen rust. The old methods of protecting blueing simply do not work that well. Oxygen has a tendency to work its way through both oil and wax if the parts are given enough time or are handled.
Handling blued parts has its own set of problems. Repeated handling strips the oil or wax away exposing the blueing and the acid in our hands eats blueing faster than you can imagine. People who are at the highest risk seam to be those who drink alcohol eat a lot of red meat or consume a lot of fruit.
The modern epoxy polymers seem to do a wonderful job of protecting blueing. They are tough, do not allow air, water or acids to pass through them and will stand up to very heavy handling and or use or misuse.
My best recommendation to you would be to send them to an automotive type paint shop and have them clear coat the parts with an epoxy. The shop will degrease the parts before they paint them and I have found that for what ever the reason there seams to be no need to prime the parts. One coat of clear coat should do it just fine.
I would be willing to bet just about anyone a case of beer that the parts have been caustic blued and not cold acid blued. Acid blueing is cheep if you are only doing a few dozen parts but because of the labor involved I doubt that any fool would try to acid blue 50,000 units.
If you just want to de-grease them and get them out of your hair which is what I expect you really want to do, just go out and buy a 50 gallon drum of Varsol or kerosene and slosh the parts around until the oil is gone. Put a light coat of paste floor wax on the parts with a paint brush, buff lightly with a rag, and pray you never have to bid on a job like that again!

Rod Henrickson
gunsmith - Edmonton, Alberta, Canada
Q. Thanks for your replies,
One of the black oxide plating houses we contacted thought they could clean the glides with a 'mineral spirit solvent' to the point where they would still have some oil residue on them to protect from rusting but not be oily to the touch.
Are you familiar with mineral spirit solvent and what are your thoughts on this?
Thanks again.
Hardware Components - Danbury, Connecticut, USA
November 19, 2009
A. Well as I have always understood it Varsol, is just ExxonMobil's version of mineral spirits ⇦ on eBay or Amazon [affil link] or paint thinner, whatever you want to call it. Kerosene is what the aircraft industry calls Jet A. It's the fuel that commercial jet liners use to cart us all over the world. I guess for all intent and purpose it's also a mineral spirit. The parts will have to be protected with wax or oil after being washed in any of these solvents. If not, they will rust!

Rod Henrickson
gunsmith - Edmonton, Alberta, Canada
Q. Hello,
I am interested in creating a finish for a tubular steel base on a coffee table. I have access to industrial factory finishing lines but am unclear about how to communicate to the factory what I am looking for. I would like the look of a black that is in the material - rather than applied with powder coating. Would black oxidizing the material be what I need to do?
- Winnipeg, MB Canada
April 16, 2012
A. Hi Madi.
I think it unlikely that you will be satisfied with black oxide on furniture. At best it will be oily or smutty. Zinc-iron plating with a black chromate topcoat would be better, but the overall most satisfactory solution would doubtless be black chrome plating. Good luck.
Regards,
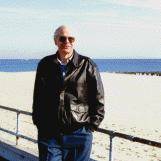
Ted Mooney, P.E.
Striving to live Aloha
(Ted can offer longterm or instant help)
finishing.com - Pine Beach, New Jersey
Removing excess oil on phosphated fasteners
Q. I have 750,000 u-nut fasteners that are coated with a phos & oil surface finish. Excess oil has dripped to the bottom of the cartons. What would the best way to solve this problem?
terry tobias- providence Rhode Island usa
July 12, 2019
A. Hi Terry. Any local plating shop who does barrel plating probably has centrifugal dryers (like the spin cycle on your washing machine, but designed for metal parts). These will fling off the excess oil without removing it all and leaving the fasteners rust-prone. Good luck.
Regards,
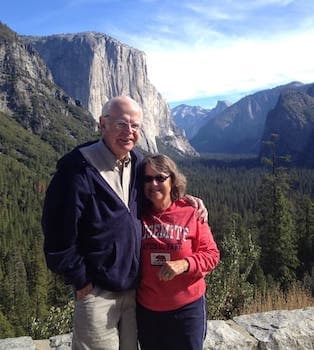
Ted Mooney, P.E. RET
Striving to live Aloha
(Ted can offer longterm or instant help)
finishing.com - Pine Beach, New Jersey
Post black oxide oil application
Q. Is there an oil that could be applied by hand to previously black oxide finished steel that would enhance the corrosion prohibitive properties? Like putting oil on a wood cabinet? We use black oxide finish in a wide variety of machine component applications and a customer is concerned that the air conditions in their plant will create corrosion too quickly.
Jon Brunner- Benton Harbor, Michigan
July 30, 2020
A. Hi Jon. The 'black oxide' that we are talking about here, is the same finish, with a different name, as 'gun bluing', and fastidious hunters wipe down their guns with an oily cloth after every use. Consequently gun oil is one such product you could use, but general machine oil like 3-in-1 should be fine too. There probably are 'rust-preventative' oils designed for the purpose as well.
Luck & Regards,
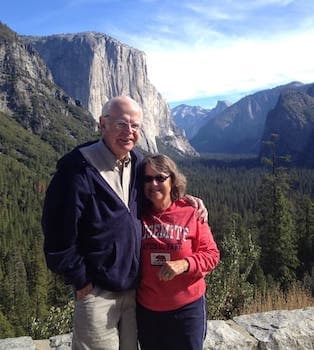
Ted Mooney, P.E. RET
Striving to live Aloha
(Ted can offer longterm or instant help)
finishing.com - Pine Beach, New Jersey
Q. I am in the middle of starting my own finishing business and I am starting with Black Oxide as a start.
I got used to the process but what is best oil / wax to use after I have dipped the parts into the black oxide?
I tried penetrating oil but it still leaves a bit of rust after I am done.
Wondering if anyone can help me please?
Thank you in advance
- Guelph, Ontario
September 29, 2022
Q, A, or Comment on THIS thread -or- Start a NEW Thread