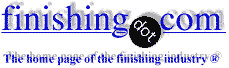
-----
Aluminum vs. lead cathodes for anodizing

Q. 6063 is not a Precipitation hardening alloy. How does it get to T6, heat treated and age hardened?
Gordon Beveridge- Australia
January 11, 2023
A. Hi Gordon. Sorry, I'm not sure if that is a refutation of the claims on this page or just a question. But my understanding, as a non-metallurgist, is that 6063 IS a precipitation hardening alloy.
Luck & Regards,
Ted Mooney, P.E. RET
Striving to live Aloha
(Ted can offer longterm or instant help)
finishing.com - Pine Beach, New Jersey
⇩ Related postings, oldest first ⇩
Q. I am looking for advice on using aluminum vs. lead cathodes for anodizing. We currently use lead cathodes, but are considering switching to aluminum, based on supplier recommendations. The case for aluminum cathodes is that less current and less cooling is required do to the greater current carrying capacity of aluminum vs. lead. A more even coating thickness across the workbar and elimination of lead from the waste stream are also given as benefits. Does anyone have experience with this matter? Any other information (recommended alloy of aluminum, proper anode to cathode ratio, recommended way to connect to copper bussing, etc.) would be greatly appreciated.
Keith Rosenblumplating shop - St. Paul, Minnesota
1996
A. Charlie Grubbs wrote several articles on this subject.
"Products Finishing" or Clariant may have copies of this article. He recommends 6063 (6061^6101 a fair substitute).
Albright and Wilson Americas has some fairly strong opinions on this also.
James Watts- Navarre, Florida
A. Charlie Grubbs' article on aluminum cathodes can be found in the Nov. 1981 issue of Plating & Surface Finishing.
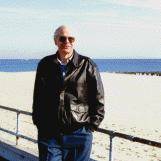
Ted Mooney, P.E.
Striving to live Aloha
(Ted can offer longterm or instant help)
finishing.com - Pine Beach, New Jersey
A. As stated above, 6063 T6 or T5 is the recommended alloy for aluminum cathodes. Alloy 6101, NOT 6061, is a substitute! Do not use the overaged 6063 T52 temper as it will dissolve rapidly. All welds should be made with 5356 alloy welding rod, not 4043, which is a common welding material.
Anode:cathode ratio should be approx. 3:1.
Lead cathodes or SS cathodes are not as good conductors as aluminum (Al = approx. 60%). Lead has a conductivity of approx. 9%; SS has a conductivity of approx. 4.5%, therefore, much of the energy from the power supply is utilized overcoming the high resistance of lead or SS, whereas the aluminum conducts the energy to the anode (parts) for better anodizing response.
In many instances, a 2-3 volt saving is noted when aluminum is used. Depending upon the total amperage being used, this could add up to considerable energy savings.
I would suggest that you bring the aluminum cathodes out of the tank and connect to either flexible copper cable or aluminum bus conductor (if the distance from the tank to the rectifier is not too far). Keep the copper below the top of the tank to minimize the possibility of copper dissolution into the anodize tank.
Hope this answers some of your questions.
Charlie Grubbs- Alpharetta, Georgia
A. I have 30 years of experience running anodizing lines. I have used both lead and aluminum. I prefer lead by far. I recommend lead cathodes connected to aluminum buswork. I have found that copper corrodes in a sulfuric acid atmosphere.
If you wish to discuss this further, I will be happy to give you pros and cons.
Raymond HendrixTroy, Tennessee
1997
![]() |
Q. Hello. Do you have any examples of specifications for lead starter sheets? Is it a pretty standard product? Many thanks, Eric Eric FrawleyPartner - New York June 23, 2021 A. Hi Eric. Raymond's posting is very old and the e-mail address we have on file may not reach him, but we'll try. Luck & Regards, ![]() Ted Mooney, P.E. RET Striving to live Aloha (Ted can offer longterm or instant help) finishing.com - Pine Beach, New Jersey |
A. As a major producer for the lighting market, we find that aluminum cathodes work for us.
Gerald Janssenaluminum coil anodizing - Streamwood, Illinois
A. Dear Gerald,
We have been using aluminum cathodes and busbars for 25 years. Purer the aluminum, better the conductivity for the busbars. AA6063 with minimum alloying elements concentration recommended. For the cathodes, even EC grade extruded sections can be used. Cathode/Anode ratio is 1:2 to 1:4 (not so important, my opinion). If busbars in aluminum, 1 amp/sq.mm is the min. section area for good conductivity. Connection of aluminum to copper needs care to prevent corrosion by cell-effect later. There are some proprietary compounds to put between Cu and Al for such purposes.
Sincerely,
Timur Ulucakaluminum extrusions & finishing - Istanbul, Turkey
A. The Sanford Process supply to their licensees the process tank with graphite cathodes.
Leonid LernerNatick, Massachusetts
A. To choose a cathode material for an anodizing system we have to take into consideration a number of factors, such as conductivity, reactivity, corrosion resistance, maintenance convenience, cost and mechanical properties, and so on.
Each kind of cathode has its own advantages and disadvantages. In general, the voltage drop on the cathodes resulting from electric resistance is negligible in the order of millivolts, relative to the whole cell voltage in the order of volts to 100 volts.
The voltage drop on the cathodes is principally attributed to the cathodic reaction resistivity. In the case of anodizing aluminum in sulfuric acid solution, for example, major cathodic reaction is hydrogen evolution. As indicated in many references, the hydrogen evolution resistivity on lead, stainless steels, or graphite is much larger than that on aluminum. As a result, the voltage drop on aluminum cathodes is the least among the cathodes mentioned above.
From the point of view of energy saving, it is natural to recommend aluminum acting as a cathode material for aluminum anodizing. To further reduce the voltage drop on cathodes, one can design the configuration of cathodes to increase their specific surface areas or develop alloys containing catalytic elements.
Ling Hao- Grand Rapids, Michigan
A. Keith,
6063 T6 isn't a readily available alloy in the T6 form. To get certified material usually you have to have it extruded at a minimum of 1000 lbs. That's a lot of material for most anodizing operations. The good news is we have our special extrusion certified to 6063 T6 in stock at all times. No minimum. We also have it in 1.5" and 2" X 4" as header bars to attach the extrusion to.
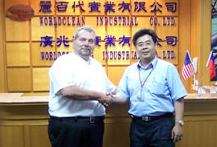
Drew Nosti, CEF
Anodize USA

Ladson, South Carolina
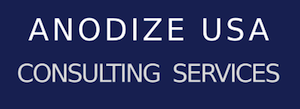
2002
Q. Well, this is an old thread, but I have a new question. I replaced some stainless cathodes with aluminum cathodes. I followed Charlie's advice for the materials. I used 1/4" x 4" 6063 T5 flat bar stock and welded it into a grid/lattice pattern with 5356 rod. The aluminum dissolved completely in 2 months. What gives? The only thing that I can think of is that the tank wasn't used much which means that it didn't spend much time cathodically protected. I guess I'm forced to go back to stainless or lead, but I really wanted aluminum to work. Comments?

Jon Barrows, MSF, EHSSC
Kansas City
June 2, 2009
A. Strange that you would get only 2 months life time. What concentration are you running?
I use cathodes supplied by Drew Nosti (the poster above yours) and I get close to 2 years life.
With that being said, I have 2 tanks that I operate at similar concentrations, but at different temperatures, and have noted that I get a much quicker dissolve rate of the cathodes in the tank at the higher temperature. What I've done to combat that, is when that tank is going to be idle for a period of time, I will keep it chilled to
40 F to slow down the dissolve rate.
Another possible solution for you, depending on your use (which sounds very infrequent), would be to store your acid in drums, then pump into the tank as needed.
Lastly, are you sure you don't have any stray current from your rectifier going to the cathodes while the tank is idle? That would also cause them to dissolve quicker.
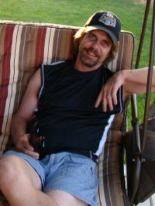
Marc Green
anodizer - Boise, Idaho
Thanks Marc. The tank is "thin film sulfuric anodize" and the concentration is much more dilute than type II at around 45 g/L. Temp is 78 degrees. Even though the temperature is higher, I expected less attack because of the dilution. That was probably wrong. The bath is used infrequently because we are waiting on auditors to qualify the process. I can't really store the tank solution in drums because it is 2200 gallons. Energy costs to chill that much solution to 40 degrees during idle periods would be too costly. The life of the anodes was so short, that I have no choice but to switch to either lead or stainless and try to design for the poor conductivity. My curiosity about the aluminum failure is mainly academic at this point.

Jon Barrows, MSF, EHSSC
Kansas City
A. Jon
Double check your alloy/temper. I have seen your issue happen twice, both times due to the wrong temper being provided.
- Colorado Springs, Colorado
A. I still feel the material you received was NOT 6063 T6. But BOLT NOT WELD [see online library article]. The only catch is that you do not put the connections to the header bar below solution level.
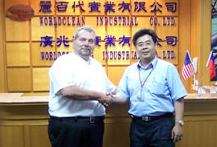
Drew Nosti, CEF
Anodize USA

Ladson, South Carolina
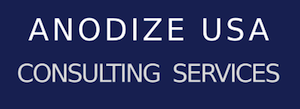
A. Drew and I might have to agree to disagree on this. I use Drew's cathodes, but am a proponent of welding the cathodes to the header bar, then coating the top with a fluoropolymer powder coating to prevent corrosion, and an unsightly anodizing tank. This also minimizes cleaning, and eliminates the need to check bolt torque on a regular basis.
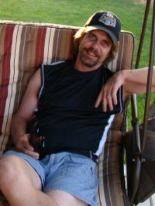
Marc Green
anodizer - Boise, Idaho
July 1, 2009
Treatment &
Finishing of
Aluminium and
Its Alloys"
by Wernick, Pinner
& Sheasby
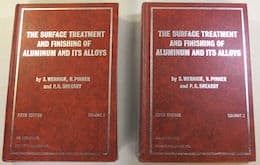
on eBay or Amazon
or AbeBooks
(affil link)
Q. I would like to take this letter further deep and need suggestions from various experts already in this field (who have always been an inspiration to me).
It has been quite a debate, and I have read in many forums/letters/online/offline publications, etc. that Aluminium cathodes are better than S.S./Lead. I agree to this fact after reading about it almost everywhere and getting opinions from experts in this field.
Now my query is, How is graphite in comparison with Aluminium cathodes? S.Wernick, R.Pinner & P.G.Sheasby in their book titled "The Surface Treatment and Finishing of Aluminium and its Alloys".
has mentioned in Pg 404, under the heading, 'Cathodes' that, "Stainless steel cathodes are used for chromic acid anodizing and for some integral color anodizing processes and graphite is used in mainly continuous anodizing processes...."
Now I am confused here. What does 'continuous anodizing process' which they are referring to, mean? If someone can throw some light on this, I would be grateful.
Also, Industry experts/Technicians who have used graphite as cathodes could share their experience comparing to Aluminium cathodes (if there is anyone who has experience in using both types)
- Rajkot, Gujarat, India
December 13, 2009
A. 'Continuous anodizing process' is I think known also as 'reel to reel' or 'coil anodizing'
Stephen ParkesRetired MD of Anodising Company - Walsall, England
September 21, 2010
Q. Hi,
Am setting up a anodizing plant for Alum Strips, Very low spec requirement, but large volumes, (50,000 pieces a month).
Have a FRP Lined tank approx. 10,000 Ltrs, at 16 V, 2000 Amp rectifier, plan to fill with 180gm/ltr of sulfuric ( I hope thats not too much ), ambient temp currently at 25 °C,
The part is a alum strip 6063t4, 1" wide, up to 30 inch long suspended by a rotomac type conveyor approx. 1.5 ft above the tank surface using alum wire hooks.
My question is what material and what configuration/shape do I use for the cathodes.
lead vs alum, everybody I spoke to uses lead, but none of them knew why!!
Any suggestions would be great..
(have the necessary environ clearances and ETP to handle the effluent etc.)
Regards
Manufacturer - Chandigarh, India
September 1, 2011
Q. I have a home anodizing system, and the physical constraints of its location prohibit removing the cathodes each time its not in use. The first cathodes were 6061 aluminum sheet, but I'm now removing and replenishing the acid in the tank because they completely dissolved over a period of about 10 months of disuse. My question is whether lead sheet, say 1/16" or 1/8" thick, will last longer. Does lead also dissolve in the sulfuric bath, or will it last a few years?
Jack Long- Austin, Texas, USA
June 7, 2012
A. The lead cathodes will last longer, but Aluminum is preferred in industry. 6063 cathodes would be a much better alloy choice as opposed to 6061, it is less susceptible to corrosion, and a far better conductor than lead. I get approx. 1 1/2 - 2 years of service out of my 6063 cathodes before they have to be replaced.
While the lead cathodes will last quite some time, you will eventually end up with a anodizing bath that is contaminated with lead, and will/should need proper disposal.
It would seem to me, that a different solution to your problem if your bath is going to be idle for months at a time would be to store your anodizing bath in a poly drum(s) while not in use.
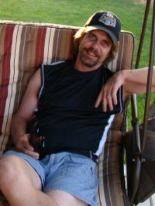
Marc Green
anodizer - Boise, Idaho
Thanks for your advice, Marc. I decided not to buy lead sheet due to the disposal problem. There's also an issue of mechanical support in the tank, which is simply something that's specific to my particular installation. Maybe the solution for this is to build a small rack to hang the plates on when they're idle, and not leave them in the bath longer than a week or so at a time. If I had done that originally, then the first set would probably still be useable.
- Austin, Texas
Avoiding use of lead in anodizing
Q. Hi All,
I wanted to start making a Sulfuric Anodize Type 2 tank. We currently have one with lead anodes but we are trying to get away from the lead as it's expensive when it comes to repairs. The question is what would I need, the type of plastic PVC or Poly? Also type of anodes instead of lead? The coils also for temperature what material?
Thank you in advance for your comments and guidance.
- orange California
June 4, 2019
A. Hi Rodger. We added your inquiry to a thread about cathodes for anodizing tanks. As you see, aluminum cathodes are an accepted alternative.
Tanks can be fiberglass, polypropylene, PVC, or PVC lined steel.
Coils can remain lead or be titanium or teflon.
We have dozens of threads with second & third opinions on those subjects if you search the site with patience. Good luck.
Regards,
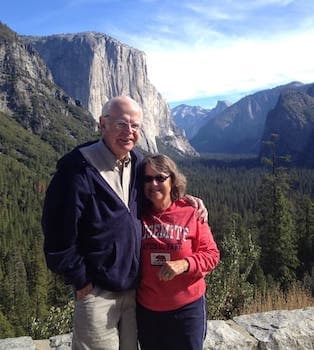
Ted Mooney, P.E. RET
Striving to live Aloha
(Ted can offer longterm or instant help)
finishing.com - Pine Beach, New Jersey
A. Lead, titanium, and stainless steel will stand up in an EXTERNAL exchanger, but the only metal that can be used for an internal coil is zirconium. You can "get by" for a while with titanium, but tie in to the cathodes for cathodic protection.
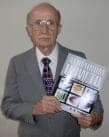
Robert H Probert
Robert H Probert Technical Services

Garner, North Carolina
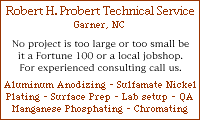
February 12, 2020
A. I have used 316L stainless heat exchangers for external plate and frame units. The other materials may work but why bother. I have never had a failure due to material on the 316 units except when a customer used plain steel fitting when hooking up the unit. And then the unit was still good to go.
! Information from our alliance partner in regard to lead cathodes:
Jan 31, 2020
"Morning Drew:
With regard to Luster-On's take on lead cathodes for aluminum anodizing, we no longer feel we can, in good conscience, recommend that material for cathode construction.
Our reasons are threefold:
• Due to the extremely low solubility and the slow acid attack on the lead, lead sulphate quickly begins to form and precipitate from the bath causing an additional sludge issue. The sludge which now contains lead causes a change in the classification of the sludge itself to a hazardous material.
• Although the solubility of lead sulphate is extremely low at 0.00443 g/L at 20 °C, that does mean that in a sulfuric acid based bath, the soluble lead ion concentration can be as high as 3 ppm in the working solution. In most municipal water districts, 3 ppm of lead would be well above any discharge limits; therefore the sulfuric acid anodize solution and its rinse waters would need to be treated and tested for lead.
• Lead is a hazardous material banned by RoHS, REACH, ELV and WEEE, along with California Prop 65, so any anodized material from a lead containing bath should be verified to be free from the upper limits of lead outlined by the various Directives."
Let me know if you have any follow-up questions.
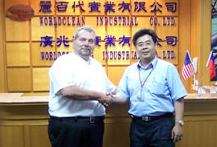
Drew Nosti, CEF
Anodize USA

Ladson, South Carolina
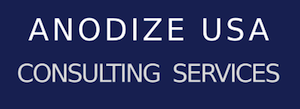
February 20, 2020
⇦ Tip: Readers want to learn from your situation;
so some readers skip abstract questions.
Q. Can Al alloy 5083 used as cathode for anodizing as alternative to Al alloy 6063?
Shaymaa ahmed- Cairo egypt
November 3, 2020
A. Here is a list of the relative conductivity for various metals for a type II & III anodizing bath: Aluminum 36, carbon 5, lead 4, titanium 2, and stainless steel 1.
When it comes to aluminum 6063 T6 has the slowest dissolution rate compared to several alloys including 5051. Generally, this correct alloy will last between 2-3 years without stray currents in the tank. 6063T6 is a special alloy/temper so it is not available as a stock purchase no matter what a standard aluminum supplier says. It is most likely T52 or T5 so ask for certs before purchase.
Now you can increase the life of any aluminum cathode by adding material but since other alloys dissolve at a faster rate than 6063T6 you will just add more aluminum into the anodizing solution and dilute your acid. Always stick with a reputable supplier who can supply certs to you before you purchase.
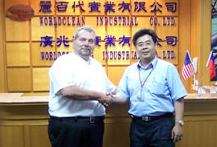
Drew Nosti, CEF
Anodize USA

Ladson, South Carolina
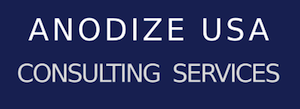
May 10, 2021
A. Yes. You may use ANY wrought alloy aluminum.
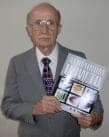
Robert H Probert
Robert H Probert Technical Services

Garner, North Carolina
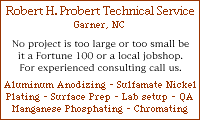
May 11, 2021
Q, A, or Comment on THIS thread -or- Start a NEW Thread