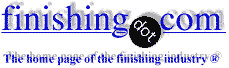
-----
Surface finishing for low coefficient of friction
Q. I am searching for surface(materials)-combinations, that show very little coefficients of friction (below 0.1!). We now use a graphite filled polyamid polymer against steel with good success, but we would like to reduce the friction further. Any advice or literature reference is welcome.
Franz Gammel1998
Q. I am looking for the same thing. So far the best luck I have had is with ceramic coatings boasting a 0.08 coefficient of friction. That sounds good to me but I haven't actually tested it yet. What do you know?
John MacHargOcean Pacific Technologies -
1999
Q. I am seeking low friction materials for use in the construction of low temperature differential engines where friction or the minimising of it is crucial. Particular uses are as bearing material for rotation and linear movement shafts of approx. 1/8" diameter. I am interested in your testing of ceramic coatings and graphite polymers and would appreciate hearing of your findings.
thanks
adrian cowardhuddersfield, england
1999
Q. I too am interested in low friction surfaces, one in particular -- it's ice.--the coefficient of friction value for this surface against a steel ice skate blade? I would greatly appreciate it!
Thank you.
Ian LieboldAthens, Georgia
2000
Q. Respected sir, I am searching for a material which would have a very low coefficient of friction (say 0.1 to 0.01) under a very high load (800 N/mm2) and a temperature of 200 °C. under surface contact.
rajesh.k- thanjavur,tamilnadu, India
2000
A. Greetings.
Teflon has a coefficient resistance of .04. Could this be of use to you? Also, Argonne National Laboratory has a material which has the resistance at an astonishing .001 and super hard, though I do not know of it's availability as it is likely a restricted product.
Eric P. Hennies- Billings, Montana USA
2000
A. To all I attach a pdf file about antimony infiltrated carbon sliding non-lubricated against MgO-ZrO2 or alumina, which exhibits a coef down to as low as 0,005 and wear rates known from mixed/boundary lubrication. Unfortunately, this was established in steam environment, which has an industrial meaning for zero-emission steam passenger car engines or APUs.
Contrary to the coatings of OAK Ridge or those presented from the Ecole Centrale de Lyon, those couples represent monolithic materials without problems related to adhesion of the coatings or limited life due to the low thickness as well; they work in air/steam, which is on earth more frequent than UHV or N2.
See J. Kleemann und M. Woydt "Friction in the millirange at 400°C without intrinsic solid lubricants", Proc. 13th Int. Colloquium Tribology "Lubricants, Materials and Lubrication Engineering", 15.-17. January 2002, Ostfildern, Supplement, p. 37-51, ISBN 2-924813-48-5 or extended next in Tribology und Schmierungstechnik and Industrial Lubrication Technology
0866.pdf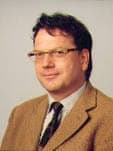
Dr. Mathias Woydt
- Berlin, Germany
2003
----
Ed. note: Unfortunately, our copy of this pdf became corrupted over the years. If anyone has a copy please email it to mooney@finishing.com.
ACRONYMS:
DLC = Diamond-like Carbon
GLC = Graphite-like Carbon
A. Certain DLC and GLC coatings can sustain contact pressures in excess of 3 GPa with a friction coefficient of >0.03.
However these are not the standard properties of all carbon based coatings.
- Worcester U.K.
2003
2004
A. THE EPILAMS.
1.The general characteristic of epilams. The epilams are multicomponent systems, which contain fluorine-organic surface-active sub-stances (fluorine-SAS) and controlling agents in various solvents. Epilaming process is a process of applying the fluorine-SAS molecules on the surface of a rigid body. As a result, the epilaming process forms a thin film of oriented fluorine-SAS molecules (40-80 A), fixed on the surface by the chemosorption forces.
The fluorine-SAS film has the following properties:
- it lowers the surface energy of the material approximately in 1000 times, that prevents spreading of a lubricating oil on the surface of the body;
- it has a low friction coefficient;
- it changes the character of wear in the zone of contact of the mating parts: the character of wear of the modified surfaces is mainly fatigue, the character of wear of the non-modified surfaces is mainly adhesive;
- it prevents the overcritical displacement of the lubricating oil (dry friction);
- due to high penetrability, the fluorine-SAS molecules fill up and degas all the pores and cracks, so the fluorine-SAS film prevents the electrochemical corrosion (prevents the hydrogen embrittlement);
- it has a resistance to high temperatures (the usage temperature is 400-450oC, the short-term temperature is 700oC), resistance to pressure (the approved unit pressure is 3000MH/sq.m), resistance to exposure of chemical substances and radiation;
- it protects the surfaces from the exposure of moisture and aggressive substances.
The counted above properties of the fluorine-SAS films make it possible to modify the surfaces of materials so that to impart them anti-friction, anti-adhesive, anti-corrosion and some other special properties.
2. The field of application.
2.1. In the world.
The element-organic SAS are widely used in the world practice as a base of compositions, which impart special properties to the surfaces. So, the department of NASA (USA) uses the compositions, having the SAS as a base, in production of high stability coats, impenetrable for liquids and gases. The firm Montaco Co.(USA) applies similar compositions to decrease the cavitation in mechanisms; Shell Oil Corporation - in production of lubrications for high-quality bearings; ÇÌ - to increase the wear resistance of recording devices. DuPont employs fluorine-SAS compositions in stable dispersion lubrications and lubrications, capable to resist the oxidising atmosphere at a temperature up to 300oC, and with the purpose to increase the wear resistance of the parts of various friction pairs. The firms Montedisson (Italy) and Hoechst (Germany) use similar compositions for impregnating the materials with the purpose to decrease the gas penetrability and impart the anti-adhesive properties to various surfaces. The firms Gold Schmidt, Texaco Inc., Avco Corporation apply such compositions as anti-wearing oil additives.
2.2. In Russia.
In Russia, a range of epilams, having fluorine-SAS as a base, has been developed. Compared with the Western and American analogues, Russian epilams have much more improved properties (for example, the thermal stability, resistance to oxidising effect, very low fugasity), that make it possible to expand the field of application. Below, there are the outcomes of trials and field of application of the epilams. Machinery, equipment, materials. Friction pairs in machines and mechanisms the service life of rolling bearings and plain bearings increases in 2-10 times, the friction coefficient reduces in 10 times, the overcritical displacement of a lubricating oil (dry friction) is pre-vented.
Instrument engineering
- the service life of optical instruments increases in 2 and more times;
- the service life of switches increases in 2-6 and more times;
- the treatment of the piston systems of pressure instruments rises the accuracy of measurement, reliability and service life; the tests showed that the break-away torque in the piston systems was reduced from 1,5-2,0 kg to 0,0002 kg;
- the treatment of the solenoid control valves of component pipe-lines rose their service life in 100 times.
Ships the treatment of the friction pairs and pipe-lines of the hydraulic systems decreases the wear, friction coefficient and friction torque, and rises the service life of
- compressors in 3 times,
- screw pumps in 3 times,
- fixtures in 3 times,
- hydraulic motors in 2 times,
- rubber seals in 10 times,
- friction pairs of steering systems in 5 times.
Diesel engines
the tests of the fuel injectors of Diesel engines showed, that the treatment of the surfaces made it possible to reduce the difference in pressure between the pump and injector on 80-100 kg/sq.sm. The pressure, giving a load on the parts of fuel pump drive, decreased on 30-40 kg/sq.sm , the injection pressure increased on 50-60 kg/sq.sm. As a result, the quality of fuel spraying improved, and the economical operation of the Diesel rose on 3-5 g/litre.h.p.hr.
Production equipment.
- the treatment of the nitrogen fertilizer production equipment (including the pumps and compressors) increases their service life in 1,2-1,5 times;
- the treatment of the friction pairs of metal-working equipment rises the precision and smoothness of movement of the actuating mechanisms, increases the service life of the equipment.
Rubber products (RP)
the service life of RP increases in 6-10 times ; RP become more resistant : the non-resistant RP become limited resistant, the limited resistant RP become resistant or chemically resistant ; the wear resistance rises in 15-25 times ; the aging stability increases in 2-3 times ; the friction coefficient decreases in such friction pairs as RP-metal, RP-polymer, RP-ceramics, RP-RP.
Production process.
Metal-cutting tools the treatment by epilams rises the wear-out period of
- turning tools in 1,5-6 times,
- milling cutters in 1,4-2 times,
- taps in 4-10 times,
- drills in 3-10 times.
At the same time, the surface roughness of the finished parts diminishes.
Press tools
- the treatment of the drawing dies rises their wear resistance in 2-4 times. Simultaneously, it makes it unnecessary to chromium-plate the working parts of drawing dies.
- the treatment of blanking dies rises their wear resistance in 2-8 times.
Vulcanising moulds
the treatment of vulcanising moulds rises their wear resistance in 4 times on the average. Simultaneously, it make it unnecessary to chromium-plate the working parts of vulcanising moulds, and excepts the application of silicone lubrications.
Injection moulds
the treatment of injection moulds rises their wear resistance in 4 times on the average and make it unnecessary to chromium-plate the working parts of injection moulds. Consumption of silicone lubrications either diminishes in 8-10 times, or is fully excepted. Quality of surfaces of the finished parts improves. The removal of the finished parts from the moulds improves. The spoilage reduces.
Grinding
the tests of grinding wheels, impregnated with the fluorine-SAS composition, showed the following:
- the wear-out period between dressings increased in 1,5 times,
- the service life increased in 1,3 times,
- burns and microcracks on the surfaces of the finished parts were prevented.
3. The epilam marks and purposes. The Table 1 contains the full information about the epilam marks, purposes, application results and technology.
4. Epilaming process.
There are the following processes of applying the fluorine-SAS films on the surfaces:
- the cold process,
- the hot process,
- the technological medium process.
Every process is a number of methods, united in a group by some general valuable sign. The hot process unites all methods, when the fluorine-SAS molecules are applied on the surfaces from the fluorine-SAS-containing solution at a temperature higher, then the boiling point of the solvent. The cold process unites all methods, when the fluorine-SAS molecules are applied on the surfaces from the fluorine-SAS-containing solution at a temperature lower, then the boiling point of the solvent. The technological medium process unites all methods, when the fluorine-SAS molecules are applied on the surfaces from the technological medium (oil, emulsion, grease), containing the fluorine-SAS.
The epilaming process is a sequence of the following production operations:
- surface preparation;
- applying the fluorine-SAS film;
- thermal fixing or drying;
- quality control.
The surface preparation means cleansing all kinds of pollution from the surfaces. Various sol-vents ( acetone ⇦ on eBay or Amazon [affil link] Flammable! , benzine, alcohol, chlorine-containing solvents) are used for this purpose. After cleansing the surfaces should be dried. The drying time is either 5-8 hours at a room temperature, or 0,5-3 hours at a temperature of 90-100 °C. In the technological medium process the surface preparation is not required.
Applying the fluorine-SAS films
In the cold process the body has been immersed in the fluorine-SAS-containing solution, or the solution has been applied on the surfaces by spraying or wadding. The film is formed after evaporation of the solvent. In the hot process the body has been placed in the boiling solution. The process runs in a sealed installation. Various methods are used for heating. The process provides better quality of the film and less consumption of the epilam, than the cold process does. In the technological medium process some quantity of the oil-compatible (or water-solvable) fluorine-SAS has been introduced into the technological medium (oil, emulsion, grease). The technological medium transports the fluorine-SAS molecules to the surfaces, which are intended to be treated. The most active process of the film forming runs on the contacting surfaces.
Thermal fixing or drying
As a rule, this process has been carried out in electric furnaces or driers at a temperature of 90-150oC. The process strengthens the hemosorption bond between the fluorine-SAS film and the treated surfaces. Products of polymeric materials and composite materials have been dried at a less temperature (sometimes at a room temperature) because of low thermal stability of the materials. Heavy parts and products have been dried at a room temperature because of the absence of appropriate driers.
Quality control
The wetting angle of an oil drop is used for estimate of the film quality. The angle should be equal or more than 72° (as shown on Fig.1). The oil drop, having 2-4 mm in diameter, should stay still on the surface as well (as shown on Fig.2). The improved methods are based on the estimate of the surface energy of the material.
5. Epilam consumption. The epilam consumption differs according to the kind of epilaming process:
the hot process - 60 g. of fluorine-SAS-containing solution per square meter of the treated surface;
the cold process - 150 g. of fluorine-SAS-containing solution per square meter of the treated surface;
the technological - 5 g. of fluorine-SAS per 1 kg. of the technological medium. medium process
6.Safety precautions. The epilams are non-toxic, non combustible and non explosible. The exclusion is the epilam bfd-2000, which is combustible. It becomes uncombustible after dissolution in the water or technological medium in proportion 1 per 5. When operating with the epilams, there is no need in special safety precautions.
Ezry Akkerman- St. Petersburg, Russia
Q. I am looking for a material that is very hard and can withstand a lot of wear, with very low friction, and that is inexpensive. If anyone can help me, I would greatly appreciate it!
Saniago Garza- Pasadena, California, USA
June 21, 2009
June 22, 2009
A. Hi, Saniago. Look into hard chromium plating. It is relatively inexpensive and has been used for such applications for decades.
Regards,
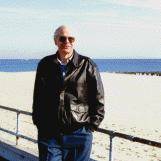
Ted Mooney, P.E.
Striving to live Aloha
(Ted can offer longterm or instant help)
finishing.com - Pine Beach, New Jersey
Q. Hi
I am looking for a material to be used in an internal combustion engine that will make close contact (seal) to steel. The material must be strong and can withstand temperatures in internal combustion engine. This is a new invention I am working on. the two contact parts both moving in the same direction and touch on a specific point only momentarily.
Thanks
PRIVATE - Johannesburg, Gauteng, South Africa
November 12, 2012
Q. Between e-coat, zinc coat or black paint, which offers the least amount of friction resistance to ABS plastic?
Jeff LangAuburn Hills, Michigan, USA
March 8, 2013
A. Hi Jeff. Although my guess is that an epoxy e-coat on a polished surface would
measure the lowest coefficient of friction, I don't think it's going to be quite as easy as that.
I think when you look deeper into the overall proposition though, you'll probably find zinc electroplating the better
counter surface to run the ABS against. Good luck
Regards,
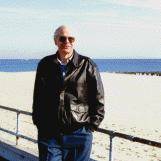
Ted Mooney, P.E.
Striving to live Aloha
(Ted can offer longterm or instant help)
finishing.com - Pine Beach, New Jersey
March 8, 2013
Q. Good morning,
I am looking for a Hard material that doesn't have scratches on it and it is frictionless.
Suggest me any alloy or composition of material or a material which has low friction, low wear, and is a hard material.
Impact Metal Parts Pvt Ltd - Gujarat, Surat, India
July 8, 2017
Hi Mitesh. Please help people help you by making your query very clear. Since you seem to reject the previous answers on this page like DLC coatings or chrome plating, can we assume that you require a solid material rather than any type of coating? Must this low friction condition exist when totally unlubricated? Hard is a relative matter ... harder than hardened steel, or just harder than plastic?
Can you give us info on the application? Good luck.
Regards,
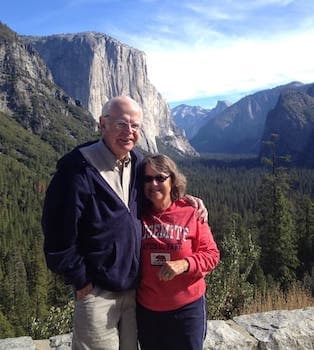
Ted Mooney, P.E. RET
Striving to live Aloha
(Ted can offer longterm or instant help)
finishing.com - Pine Beach, New Jersey
July 2017
Use ice blocks!
Bangalore Plasmatek - Bangalore, Karnataka, India
July 9, 2017
Q, A, or Comment on THIS thread -or- Start a NEW Thread