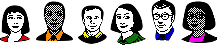
world gathers for metal finishing
Q&As since 1989
-----
How to Electroform nickel -- Introduction to Electroforming
for Plating Shops & Engineers (affil links)
Electroforming by Peter Spiro (1971)
avail from eBay or Amazon
Bureau of Standards: Electroforming of Waveguide Components
avail from AbeBooks or Amazon
Electroforming of copper for high vacuum applications
avail from AbeBooks
Fabrication of liquid-rocket thrust chambers by electroforming
avail from AbeBooks
A survey of electroforming for fabricating structures by W.H. Safranek
avail from AbeBooks
Electroforming in Restorative Dentistry
avail from AbeBooks or Amazon
Principles of electroplating and electroforming by William Blum (1949)
avail from eBay, AbeBooks or Amazon
Q. Hey, everyone! I'm very new to this (I won't say "green"; I'm not oxidized (or might we say "jaded") yet)... anyway, I was wondering ... I need a process that will allow me to electroform a >10 mil coating of nickel onto a conductive substrate, said coating to be mechanically finished. Can someone point me in the right direction? I'm not looking to take this job to someone's shop; I have my own equipment, but I need something like the Electroforming Society's old "how-to" sheets. Can someone tell me where I might find them on-line? Thanks!
Rich MartinSeraphim Productions
1996
A. Hi, Rich. I think if you are patient in searching you should find some good technical articles from the Nickel Development Institute site as well as the many threads about electroforming here on finishing.com.
These days I don't see why you should need to mechanically finish after electroforming (although you may have your reasons). It should come out of the tank smooth and bright. Most electroformers use sulfamate nickel plating solutions, if that's a starting point, and very low amounts of brighteners or none. Maybe call up a supplier and ask for a sulphamate solution for electroforming to get started.
You may wish to review the excellent chapter on electroforming (and also the nickel plating chapter) of the Metal Finishing Guidebook.
Good luck.
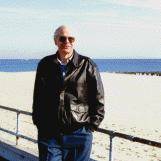
Ted Mooney, P.E.
Striving to live Aloha
finishing.com - Pine Beach, New Jersey
Seeking info on electroforming watch dial markers
Q. Dear Sir,
In electroforming flat objects, I have a raw information that the metal substrate is specially textured, I guess it is for the ease of removal.
What specific metal is most suitable for this process? This metal substrate is then coated with photo sensitive coating and the image has to be transferred by a UV light exposure. After rinsing off excess photo resist, an electro deposition process will take place on the unmasked surface. What is the current density required if the product is about 1 inch diameter?
The purpose of my research is to acquire a technology of making the watch dial hour marker(gold and nickel) through electroforming. In our application after removing the product from the substrate, the bottom portion is sprayed with adhesive
[adv: adhesive spray on
eBay or
Amazon] ready to stick on the watch dial face.
Thanks and looking forward for your prompt advice.
Process Engineering Manager - Philippines
2000
Q. Hi,
I want to setup a nickel electroforming unit for watch hands in India. I tried so many people but couldn't get any info. I got some technology information from China that says I have to create a SS mandrel through graphic art film and photo resistive glue, than develop the mandrel >> washing >> acid activation >> washing >> dip into electroforming tank >> washing and than peel off using transfer sticker.
This info does not include chemical names, voltage, amps, flow rate, quantity of chemicals/gal, photo resistive chemical composition and any other know-how.
Can someone give me detailed know-how or suggest a book?
prepress - Kanpur, UP, India
October 11, 2012
A. Hi Mittal. We appended your inquiry to a thread which should answer it. The Electroplating Engineering Handbook [on AbeBooks or eBay or Amazon] also has a great chapter on electroforming with over a hundred references. But it is obviously hard to proceed from no prior knowledge, so it will probably go faster if you can retain a consultant or get help from a supplier. Good luck.
Regards,
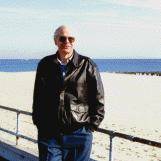
Ted Mooney, P.E.
Striving to live Aloha
finishing.com - Pine Beach, New Jersey
A. Contact the Institute of Metal Finishing in Birmingham, UK. They have a very good education course on electroforming that can be done by distance learning.
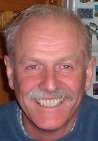
Trevor Crichton
R&D practical scientist
Chesham, Bucks, UK
Current density for Nickel electroforming?
Q. Hi,
I have a Nickel Sulphamate process and am trying to electroform surface patterned photoresist structures. My process works fine for non-patterned photoresist, but with patterned photoresist the electroform peels/pops away from the substrate during electroform. My guess is that the current density ramp is wrong. Could anyone give me an idea of typical current density ramps for CD manufacture. At the moment am using 17 ASF for 15 mins, ramp to 60 ASF in 1 min and plate for 5 hours.
Regards
- Quebec City
2000
A. It depends very much on the agitation, Mike. With minimal agitation 60 ASF is probably too high. With good agitation it's probably no problem at all. You might want to investigate a real-time stress monitor or, at the very least, "stress tabs" (a modified hull cell panel coated with resist on one side and serrated like a comb so you can see the stress at different ASF)
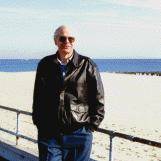
Ted Mooney, P.E.
Striving to live Aloha
finishing.com - Pine Beach, New Jersey
A. Hey Mike,
First the photoresist, some resists adhere better to a oxide than to clean metal (I know you don't want an active mandrel but the oxide layer needs to be even) so you must be sure that the surface to be plated is free of trace resist (easier to see with copper than nickel but can be done). Resists have a lot of factors to get right. (A balance of F-stop number and range, development break point, resist adhesion, to control side wall softening and leaking and good optics to insure sharp/clean features (good film density, complete vacuum, and proper light source.)
Next the bath/deposit stresses must be mildly compressive to hug the mandrel. As the deposit gets thicker this is more important. Measure the stress at the CCD you are using and remember that a patterned area (lines in the photoresist) plate at many different CCD's all at the same time with the finest lines plating at the highest CCD.
Regards,
- Royersford, Pennsylvania
Q. Mike Miller:
I'm interested in the photoresist used in the process described in his letter. How thick can this resist be applied and "cured"? The application I have in mind would require a 20 mil thickness.
- Huntsville, Alabama
![]() |
Q. Ted, please give some more info about the "stress tabs". ![]() ![]() Sara Michaeli Tel-Aviv-Yafo, Israel A. Hi Sara. "Stress-tabs" are offered by Larry King Co., 13708 250th St., Rosedale, NY 11422. Whether the name is a trademark I don't know, because I've only heard it verbally and second-hand. Likewise, whether there are competitive products or the idea is patented, I don't know. ![]() Ted Mooney, P.E. Striving to live Aloha finishing.com - Pine Beach, New Jersey |
Looking for the method for separation of Nickel electroform from Brass substrate
Q. I am a undergraduate student working on a project where I should conduct nickel electroforming process on brass substrate.
Brass substrate has micro-scale patterns on it and it should be replicated via nickel electroforming process.
Prior to the electroforming process, I passivated the brass substrate with oxide layer to prevent diffusion between brass and nickel.
I did a couple of experiments and found it difficult to separate electroformed nickel from brass substrate with maintaining reasonable flatness.
Anyhow, the main factor I should focus on is the flatness of electroformed nickel.
Is there any novel method for this?
Any comments would be appreciated.
Computer - Seoul, South Korea
June 20, 2012
A. Electroforming is not a simple case of depositing a metal onto a mandrel and then removing it as a perfect shape. The mandrel needs to be designed correctly so that the electroform can be removed - that is, there needs to a draught angle on the mandrel. Secondly, the mandrel must be adequately passivated; brass can be passivated by a tenacious layer of copper sulfide, so dip your mandrel in a solution of sodium sulfide (50-100 g/l) or better still, sodium metabisulphite (200-220 g/l) and leave it for 5-8 minutes. Alternatively deposit a thin layer of bright nickel onto the brass mandrel and then passivate it. Nickel does not easily adhere to another nickel surface, especially if it is bright, but the extra passivate gives it an even better chance of separating.
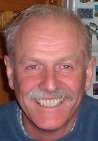
Trevor Crichton
R&D practical scientist
Chesham, Bucks, UK
Ed. note: For more info on separating electroforms from mandrels, readers may wish to view letter 42447, "Electroforms are sticking to cathode/mandrels"
Can't Remove Oxidation on Electroforming Mandrel
Q. Hello finishers,
I work at a Nickel electroforming factory which specializes in growing nickel products from a mandrel made of nickel also.
Previously we were able to achieve a life cycle in the range of 50 grows for a nickel mandrel, but recently government has been enforcing policies to restrict our daily water use.
Now the average life cycle for a mandrel has dropped to about 20-30 grows. Main defects we are finding are a white or yellowish oxidation which the image then transfers to the final product. The oxidation does not get removed during any cleaning process or acid soaks.
After each nickel grow we clean tools using anodic electroclean, neutralize with acid, then passivate with potassium dichromate.
If anyone could provide some insight into what causes this visible oxidation on nickel mandrels and also if there is a product out there that can remove it.
Thanks.
R&D Manager - Shenzhen, China
March 27, 2014
Process for electroforming metal stickers
Q. l want to learn the electroforming of metal stickers process: how many processes, which chemicals are used, how many times dried -- as an important knowledge,
Is there any sheet or book about this process?
What is the important part of electroforming metal stickers?
Can I find someone to help me with this Project?
- turkey,istanbul
November 12, 2014
Q. what is the differences between electroforming and electroplating? I'm confused how to avoid nickel electroform from adhering to mandrel? As I know dry resist film is used to transfer the image but I'm just doing nickel laser cut, plain stencil not fully electroform.
SAZLIN- MALAYSIA
July 6, 2020
A. Hi cousin Sazlin. The difference between nickel electroforming and nickel electroplating is that nickel electroplating involves depositing nickel onto the surface of a part to improve the part's appearance, corrosion resistance or some other property of the part. The part, which is made of some other material, is the thing of main interest and the nickel is just a coating on it.
In electroforming, the nickel deposit itself becomes the part: a coin, a stamper, a piece of jewelry, a miniature bellows, an intricate machine part, a wave guide, etc.
As with other things in life, there are always borderline cases: is a nickel plated flower or maple leaf a nickel electroform or is it just a nickel-plated leaf or flower? Obviously, it can be argued either way.
In practical application though, nickel coatings are usually something like 5-20 microns thick whereas few electroforms could have any structural integrity at that minimal thickness. So electroforming usually involves much thicker/heavier nickel plating, and in turn that may impose some new limitations in how it can be done.
Although I don't quite understand your situation, regarding "just doing nickel laser cut, plain stencil, not full electroform", the removal of an electroform from its mandrel can be a tricky issue because if it comes off too easily it can spontaneously pop off during electroforming, with nickel then growing on the underside and ruining it. We have several threads here about removal of electroforms from permanent mandrels (please search the site), but they usually involve passivating the mandrel with sodium dichromate, or using egg albumin or something similar as a separation agent, plus paying careful attention to the mandrel design.
Luck & Regards,
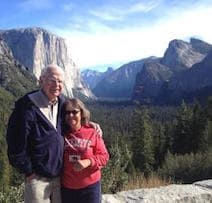
Ted Mooney, P.E. RET
Striving to live Aloha
finishing.com - Pine Beach, New Jersey
for Artisans, Jewelry, Crafts (affil links)
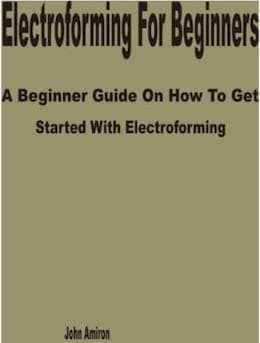
avail from eBay, AbeBooks or Amazon

avail from Amazon
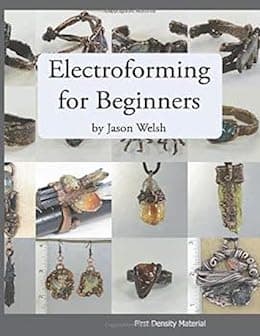
avail from Amazon
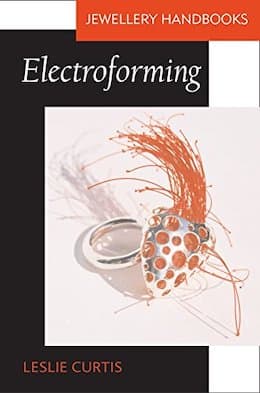
avail from eBay, AbeBooks or Amazon
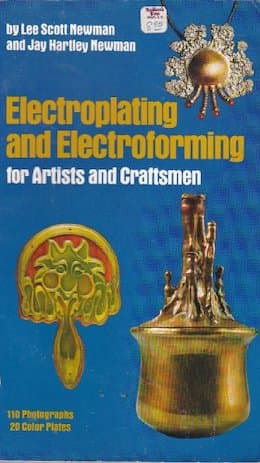
avail from eBay, AbeBooks or Amazon
Q. I have no idea what type of non conductive layer that will be used to separate from mandrel? I'm currently doing an experiment of nickel electroforming on a sheet of nickel foil. Generally I have idea to use nickel pellets as anodes, stainless steel mandrel as cathodes, nickel sulphamate, nickel chloride, boric acid as electrolytic solution, beaker [beakers on eBay or Amazon], rectifier, solution of sodium dichromate to give a passive parting film on the surface of stainless steel. All these for small scale only. But I have no idea what makes the nickel electroform to not stick (adhere) to mandrel so I can peel it to get electroformed nickel foil. Is there any sources, book or websites that fully explain about nickel electroforming?
SAZLIN [returning]- MALAYSIA [returning]
July 6, 2020
A. Hi again.
The "dichromate to give a passive parting film" is the same thing as the "non conductive layer that will be used to separate from mandrel".
Luck & Regards,
Ted Mooney, P.E. RET
Striving to live Aloha
finishing.com - Pine Beach, New Jersey
Q, A, or Comment on THIS thread -or- Start a NEW Thread