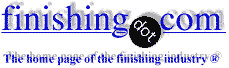
-----
Alkaline non-cyanide zinc plating vs. acid zinc

Q. We are working introducing cleaner technology in the Malaysian Industry - especially in the SMI's here. We are currently working with a plating shop who uses conventional "alkaline and cyanide" zinc plating.
We know the acidic cyanide free process, but is there any information on alkaline processes without cyanide ?
SIRIM
1996
A. All major supply houses have non cyanide alkaline zinc plating process. They are used for years and they are easy to operate. I don't know the suppliers in your place but Enthone-OMI and Mcgean-Rohco sell this process.
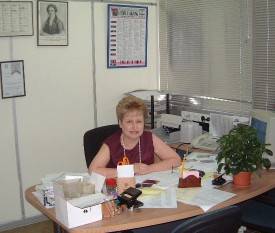

Sara Michaeli
Tel-Aviv-Yafo, Israel
A. There are 3 principal types of zinc plating: cyanide, acid, and alkaline non-cyanide.
The cyanide processes are the oldest technology, but cyanide processes are relatively easy to operate, versatile, and forgiving. Cyanide is a potent, fast-acting, poison and it is certainly a good idea to reduce its use.
Acid zinc is usually brighter, and is well suited to barrel plating, so that the great majority of barrel zinc platers use acid zinc. While acid zinc can also be used for rack plating, it lacks the throwing power of cyanide zinc, so it is often not a satisfactory substitute for chassis, and parts with crimped, staked, or spot welded features.
Alkaline non-cyanide zinc is reported to have good throwing power, so it is a better substitute than acid zinc for parts that require good throwing/covering power.
In substituting either alkaline non-cyanide or acid zinc to replace cyanide processes, remember that cyanide is "the world's best cleaner", and you may need to improve the pre-cleaning in order to make a satisfactory transition. Also remember that all zinc plating processes involve organic brighteners that can interfere with chromating, so that changes to the chromating procedures may be necessitated as well.
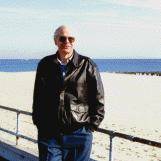
Ted Mooney, P.E.
Striving to live Aloha
(Ted can offer longterm or instant help)
finishing.com - Pine Beach, New Jersey
Q. 1. What is the ratio of Alkaline vs Cyanide zinc plating installations in the world?
2. What are the advantages/disadvantages of alkaline vs cyanide zinc plating?
3. Is it true that surface preparation is more critical in case of alkaline zinc plating?
4. Is there a web page from which I can learn more about alkaline zinc plating and the defects associated with this process?
- MH, India
2001
A. Hi Kripa.
1. Sorry, I don't know,; and I doubt that anyone knows authoritatively. 10 years ago I would have said there were many more cyanide zinc plating installations in the U.S. than alkaline non-cyanide. Today, I am fairly confident that the reverse is true. But cyanide solutions are non-proprietary and have no vested advocate, whereas alkaline non-cyanide solutions are proprietary and promoted by vested interests; thus you would see more journal articles, more presentations, and more chatter about alkaline non-cyanide even if it were the less prevalent technology :-)
2. Cyanide solutions are non-proprietary and thus less expensive; the vendors of alkaline non-cyanide solutions claim that this is more than offset in waste water treatment costs, however. In performance there is probably little difference.
3. Cyanide is a very powerful cleaner, and decades ago the transition could be difficult because the parts got to the plating tank somewhat soiled; but a properly designed line doesn't rely on the plating tank offering cleaning ability anyway, and it's been a long time since last I saw a plating line for steel parts that lacked an electrocleaning tank.
4. The Metal Finishing Guidebook has a pretty good defects guide.
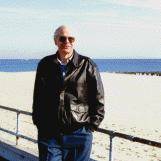
Ted Mooney, P.E.
Striving to live Aloha
(Ted can offer longterm or instant help)
finishing.com - Pine Beach, New Jersey
Multiple threads merged: please forgive chronology errors and repetition 🙂
Acid vs. non-cyanide alkaline zinc plating for fasteners
Q. Hello Everybody,
For zinc plating of fasteners, alkaline zinc plating is having the faster deposition rate or acid - ammonium chloride process?
Regards,
wire - Dubai
2002
A. Depends on what thickness you finally want. If the thickness for barrel jobs you need is under 5 microns, then stick to Chloride zinc. If you want 10+ microns use alkaline zinc.
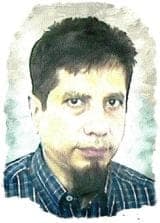
Khozem Vahaanwala
Saify Ind

Bengaluru, Karnataka, India
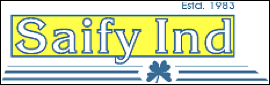
A. Dear Santosh,
Plating of Non Cyanide Alkaline Zinc is quite difficult process with regard to cost and maintenance. It require good quality attention to manage plating line. Its always better to have Acid Zinc line for fasteners. Since non cyanide zinc plating has bit of poor reception of passivation what I have observed.
Regards,
- Mumbai
A. Hi Santosh,
I would also recommend acid zinc but for a different reason: modern acid zincs can handle temperatures up to 40 °C quite well - alkaline zincs cannot. Acid zincs with potassium chloride are not as corrosive as the old ones and are very easy to run.
All the best,
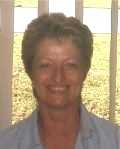
Trudy Kastner
electroplating service - Durban, KZN, South Africa
A. If you really desire a good plating use duplex Zinc. i.e. First layer of Acid Zinc Followed by Alkaline Zinc. Alkaline Zinc because of it's columnar hollow microstructure receives good passivation layer thereby offering excellent corrosion resistance.
Abhay Bhagli- Pune, India
June 10, 2008
A. Acid Zinc has the drawback of corrosion of machinery due to higher chloride content. But hydrogen embrittlement on high tensile fastener plating is the minimum among the various zinc plating processes.
Alkaline zinc can reduce neutralisation additives in ETP whereas rinsing should be very good; probably you need to have a hot water rinse after plating (especially for lower operating temperatures). If rinsing is not sufficient addition of chromate film will pose problem. In all the process needs to be monitored closely.
My suggestion is to go in for acid Zinc for fasteners.
- Bangalore, Karnataka, India
June 16, 2010
Alkaline zinc plating gives more NSS life than acid zinc plating but its process control requires more attention than acid zinc plating. I think productivity is less in alkaline zinc. So, in fasteners acid zinc is better than alkaline zinc for productivity.
Rameshwar Roy
fasteners - Bhiwadi, Rajasthan
Multiple threads merged: please forgive chronology errors and repetition 🙂
Comparison - Acid and Alkali Zinc Plating
Q. Can anybody tell me the difference between Acid Zinc plating and Alkali Zinc plating? What are the modifications that I need to make in the m/c, bath and other setups to convert Acid to Alkali Zinc plating?
V S Mageshengineer - Chennai, Tamil Nadu, India
2004
A. Hi V S Magesh,
The biggest improvement will be the plating rate in the low current density. I am not sure if this is the case with all alkaline zincs but it is with the product we use. The acid zinc plant is fine for alkaline zinc plating, however it is recommended to have a separate zinc anode dissolution tank off-line. The only disadvantage are the 5 additives, which take a little getting used to.
Good luck!
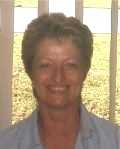
Trudy Kastner
electroplating service - Durban, KZN, South Africa
A. Mr Magesh,
Alkaline cyanide-free Zinc will function as follows.
- A throw of 1:1 LCD to HCD.
- The plating uniformity will provide improved SST.
- A filter is necessary for continuous good result. Some people still don't use filters.
- The current will pass at lower volts saving some electricity.
- There are two regular additives and 2 auxiliary additives i.e., - a Purifier and a conditioner. . One fume suppressant. Easy to use.
- Process is summer-proofed, works up to 50 °C.
Good luck,
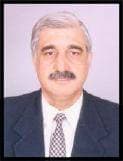
Asif Nurie [deceased] [deceased]
- New Delhi, India
With deep sadness we acknowledge the passing of Asif on Jan 24, 2016
Q. Sir,
I want to know the advantages of Alkaline Non Cyanide Barrel Plating over Acid Barrel plating for Zinc plating.
- JAMSHEDPUR, JHARKHAND, India
February 15, 2016
A. Hi Arijit. We appended your inquiry to a thread on the subject. Letter 34321, "Differences between chloride (acid) and alkaline zinc plating" offers additional perspectives, and patient use of the search engine will yield still more. But if you detail exactly what kind of parts you wish to plate, and the application, people can probably offer a specific recommendation. Good luck.
Regards,
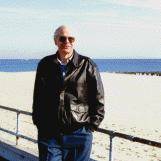
Ted Mooney, P.E.
Striving to live Aloha
(Ted can offer longterm or instant help)
finishing.com - Pine Beach, New Jersey
Which zinc plating is best for cast iron, acid or alkaline
Q. Sir,
We are doing zinc alkaline plating on cast iron components. After a few hours black corrosion is developing in the casting surface. How to avoid this issue? Which process is best acid or alkaline?
- Coimbatore, Tamilnadu, India
November 3, 2017
A. Hello,
Stick with Chloride Zinc.
Minimize Acid pickling and resultant carbon enrichment of the surface.
regards,
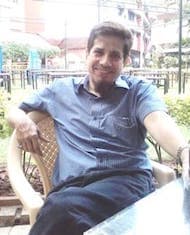
Khozem Vahaanwala
Saify Ind

Bengaluru, India
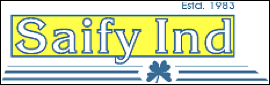
Q. Why throwing power is better in alkali zinc bath bath as compares to acid zinc bath, and efficiency is less in alkali zinc bath as compared to acid zinc electrolyte?
girish chandra- Bangalore, India
April 4, 2018
A. Hi Girish,
For throwing power, it is because of the form (and chemical functions) of the carrier involved in the plating process. In cyanide zinc, the carrier was the cyanide ion with a leveler of medium to high molecular weight, nowadays it is something with almost the same behaviour without the cyanide because of its hazard level. Alkaline conditions make zinc behave differently than in acid plating baths: zinc is dissolved in form of a hydroxy-complex instead of a lone plus-charged ion.
For efficiency, in alkaline conditions it is very difficult to avoid or diminish hydrogen production in the cathode. Brighteners and levelers maintain hydrogen overpotential high and the kinetics of this reaction slow, but from 1 to 30% of the current goes to hydrogen production. In alkaline conditions, it is very difficult to maintain less than 10% of hydrogen production, so efficiency is lower in this case. Acid zinc plating baths have a nominal efficiency of 99% and hydrogen overpotential can be maintained very high.
Hope it helps! Best regards,
TEL - N FERRARIS - Cañuelas, Buenos Aires, Argentina
Q. We were earlier using cyanide zinc and have recently shifted to alkaline zinc for plating springs made of high carbon steel. The issue we are facing is that after some time the zinc starts fading and gets dull with time. Is it something related to the dip we are using or is alkaline not suitable for high carbon steel?
Thanks & Regards
- Ghaziabad, India
February 15, 2019
A. Hi Akshay,
You say that the parts get dull with time, which would indicate that the process is suitable, as you have conforming product at the beginning.
Do you carry out any Hull Cell
⇦ huh?
analysis? It may be you are depleting your brightener rather quickly. Try adding some to your hull cell and see whether the dullness moves further toward the low current density area (away from the anode). Also, check the bath chemistry, to make sure all the components are in the correct proportions.
Alternatively, take a sample and send to your chemical supplier (assuming you are using proprietary chemicals), they will be able to tell you whether the tank is in balance.
Aerospace - Yeovil, Somerset, UK
Q, A, or Comment on THIS thread -or- Start a NEW Thread