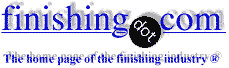
-----
Copper electroforming problems
Q. Recently all of the things I have been electroforming have been coming out this reddish copper color. I understand that when there is not enough current the result is a dull salmon color , but this is a little different. The object is still shiny it's just more red. It looks much different than other times that I have had too little amps on my object.
Any ideas to why this might be happening? For context I have a massive 150L tank that I use for all sorts of materials and sculptures. We electroform onto 3D printed plastics all the way to literal garbage -- not very clean but I do have a flo-king filtration system for particulates.
Attached are photos of the reddish color (shiny) and then another photo of a normal object that is shiny and the typical copper color. Both taken in similar lighting --
Does anyone know any scientific basis for why there is color variation based on the amps? I understand that the shiny ness comes from a smoother surface from a more steady and level plating, but why is there a difference in hue?
Sebastian Bidegain- New York
December 28, 2023
A. Hello Sebastian, you could be co-depositing some unwanted metallics in the bath. Your copper bath supplier should be able to do a full analysis on the bath that includes suspect metal concentrations. Iron is a big one to watch. You can also dummy plate the bath at low current densities. Watch the temperature during plating as well. As far as color change caused by different amperage, there must be a problem either with the solution, rectifier, or other parameters for the process.
Mark Baker- Cazenovia, New York USA
January 4, 2024
⇩ Related postings, oldest first ⇩
Q. I am attempting to electrodeposit a copper layer on a silver coated conductive substrate (wax), resembling a large coin/medallion. It is very important to me to preserve as much of the surface detail as possible, because my next step will be to melt away the wax and use the plated copper as a mold. The diameter of the wax medallions is approximately 6 inches. I am experiencing surface burning, dendritic features, surface "wrinkles", porosity in the areas of low radius curvature, and spontaneous flowering of beads. I must be doing something wrong. Can anyone help me? Thanks for any info or advise.
D Marti1995
A. Hi, D. Yes, as you suspect, the problem is not the limitations of the technology, but that you are doing something wrong :-)
The preservation of detail that you are looking for is not even a challenge for a properly operating process. Compact discs with their billions of precise dimples, and record stampers, wave guides, precision screening and a host of super critical items are made by processes similar to yours.
First, please talk to a plating chemical supplier and consider getting a proprietary copper plating bath. Their leveling/brightening agents are the result of decades of research and development. Follow their technical data sheet, and you'll quickly see dramatic improvement. Then control the temperature as recommended, and keep the amperage in a very low range. You may also want to get out to some local AESF meetings to discuss your situation and polish your skills still further.
Although you want to minimize the defects you speak of, they are on the outside of the electroform and it is the inside surface that is most important because it will be replicated. Good luck.
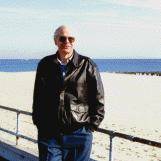
Ted Mooney, P.E.
Striving to live Aloha
finishing.com - Pine Beach, New Jersey
A. My company also does electroforming on wax shapes (for a totally different application) and it sounds like a bath control problem. Follow the previous advice and tank to a qualified vendor. We are using a product that was developed for rotogravure (printing) but we control to a lower hardness. It is a proprietary bath and I'm sure other vendors have good products too.
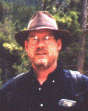
Bill Vins
microwave & cable assemblies - Mesa (what a place-a), Arizona
Leveler / Brightener for Acid Copper Electroforming
Q. I NEED HELP FINDING A FORMULA FOR MAKING A LEVELER/BRIGHTENER FOR ACID COPPER ELECTROFORMING. I'VE BEEN USING SOME COMMERCIALLY PREPARED ONES, BUT THEY HAVE BEEN VERY EXPENSIVE TO BUY AND SHIP. I WOULD VERY MUCH APPRECIATE ANYONE'S HELP ON THIS ONE. I AM ELECTROFORMING ART OBJECTS, AND LEVEL DEPOSITS ARE VERY IMPORTANT TO ME … BRIGHT IS OK, BUT NOT NEARLY AS IMPORTANT AS LEVEL AND NON-NODULATED. PLEASE HELP. THANKS.
MARK STANITZ1996
A. Hi, Mark.
Sorry that commercial products are expensive to buy and ship, but virtually every production plating shop finds that they really are worth it. Hopefully a reader can offer some ideas for specific generic formulas, but I don't have any. In fact, I think that you might benefit from considering a different proprietary salt rather than copper sulphate.
One point to remember is it takes time to make a quality electroform--a lot of time! While it may be possible to acid copper plate at 40-50 ASF, you'll probably need to electroform at a small fraction of that to avoid nodules. Best of luck.
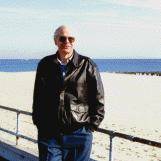
Ted Mooney, P.E.
Striving to live Aloha
finishing.com - Pine Beach, New Jersey
A. One thing is very important. Are you using air for agitation of the solution? If not, this is very important for distribution of copper and leveling. Then, and this is for the last 41 years, is a product that I use: its called UBAC#1. I also have made electroformed copper guitar, one piece guitar. I can also duplicate any wooden instrument in copper, but that's a different story.
David Neily- Watsonville, California, USA
2001
Electroforming rectifier questions
Q. I have recently purchased a small plating rectifier and accoutrements for my small jewelry business, and have attempted to electroform some small items as a sideline. Recently, the copper electroforming is, well, not working. I have had some success (a nice, bright finish), and some failures (a lumpy, dark finish -- because I "burnt" the process), but the last several attempts have resulted in a smooth, dark, oily finish -- what on earth have I done wrong? AND does it have anything to do with the fact that my rectifier is now "on the blink" and doesn't seem to transmit any electricity to the leads? (Although the oily finish started a day or so before the rectifier started acting up)
Blake Johnson- Oakland, California
2000
A. I have done an extensive amount of electroforming in my business. I have done everything from real flowers to baby shoes to wax models.
From some of your successful attempts, I assume that you are applying the conductive paint, silver nitrate, tin solution, etc., in a proper manner prior to plating. From my experience, you can look at the part after it had been in the tank for about a half an hour to get a very good indication whether your power (amps) is properly set. If the part is copper colored like a new penny, then your setting is perfect. Salmon-pink equals amps too low. Burnt brown or dark brown, amps too high. Try to calculate the area being electroformed as best you can. 10th of an amp per square inch … no less … no more. As for your rectifier, it may be on the blink.
Pewter and Plating - Bel Air, Maryland
Very exacting and informative, Henry. Thanks!
Regards,
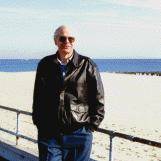
Ted Mooney, P.E.
Striving to live Aloha
finishing.com - Pine Beach, New Jersey
Copper electroforming with non hazardous chemicals
Q. I have absolutely no experience electroplating or electroforming with anything. My intention is to electroform copper onto a conductive paste. I want to avoid hazardous materials, even if it takes a great deal more time to build up the copper. I came across thread 4188, "9th grade electroplating science fair project" which suggests using acetic acid ⇦ on eBay or Amazon [affil links] (vinegar), Epson salt (magnesium sulphate), sugar and dishwashing fluid (a drop).
I also came across a site that implied their particular electroforming solution was acid based (non alkaline? -- probably sulfuric acid?) but no details, and I also came across a detailed electroplating? formula:
1.8 M Sulfuric Acid
40-100 ppm Chloride ions
50-500 ppm Polyalkylene-Glycol
5-100 ppm Organic Sulfide (SPS)
Anyway, my questions are: Is it even feasible to electroform with an acetic acid in general? If so, does anyone have a good formula? Or could someone critique the formula that I pieced together:
0.25 M copper sulphate ⇦ on eBay or Amazon [affil links] (62.48 grams/liter)
50-500 ppm Polyether (polyalkylene glycol)
some amount of Sugar?
I have so many questions (ugh). Is that formula realistic? Does anyone know how much sugar per liter is an optimal amount? Is Epson salt still needed or beneficial along with the copper sulphate? If so, does anyone know the optimal amount per liter? Does anyone know or is there a way I can estimate how high I can push and maintain the bulk copper concentrate, and an optimal realistic value to aim for (is more always better for the bulk copper concentrate)? With the absence of chloride, is polyether still an effective leveler? Does adding the drop of dishwashing fluid enhance that formula?
A couple of followup questions: the flow rate that I read so much about, does that refer more to the agitation of the solution, or the filtration pump recirculating rate, or both, or neither? When it comes to the agitation and number of times the solution gets filtered per hour, is more always better? One final question: in a setup like described does anyone know the highest voltage advisable without running the risk of "burning"; does that depend on the size of the bath and surface area of the copper anode? And can someone experienced point out to me where my novice / ignorance on electroplating is jumping out at them, and offer any information I'm lacking.
Best Regards,
Joseph James- Bridgman, Michigan, USA
2002
(affil links)
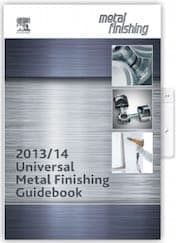
free pdf is currently available from academia.edu
A. Hi Joseph, I can see that we have confused you a bit. Sorry, but please try to forget the idea of vinegar ⇦in bulk on eBay or Amazon [affil links] solution -- you might still be, by law, generating regulated hazardous waste anyway :-(
A realistic guideline about avoiding hazardous processes though would be to not consider using any cyanide-based solutions, any concentrated acid or alkali, any chromic acid, any cadmium, mercury or lead, or any fluoride compound no matter how dilute. copper sulphate based solutions can be used for electroforming, and copper sulphate is often used in high schools for similar experiments.
As for the desired concentration of copper, it's pretty much "the more the better". A simplified explanation is that the copper ions must migrate across the solution and through the boundary layer, and you do not want the cathode ever "starved for copper" because then the excess electrons will pull hydrogen ions out of solution instead, leaving behind OH ions to neutralize the acid you need and causing other problems. High circulation rates make for better filtration and better ion transport across the solution.
As for what you might be missing that "jumps out at me", it's that real plating processes are not home-brew affairs :-(
You don't mix them from basic chemicals; you buy a proprietary plating/electroforming solution from suppliers who have figured out, from years of research, exactly what they need to contain besides the bulk ingredients like copper sulphate. The thing is, it's drop dead easy to move metal from the anode to the cathode, but getting that material to actually constitute a useful robust deposit is difficult. One other thing that jumps out is that you might find it productive of your time to look for the "Metal Finishing Guidebook", the Electroplating Engineering Handbook ⇦ this on
eBay,
AbeBooks, or
Amazon [affil links]
, or another plating textbook; books are invariably arranged in a structured tutorial fashion where learning is straightforward; smatterings of info from different sites offers no organizational structure, so progress can be tedious, and always involves ten steps forward / nine steps back because you're guaranteed to partially misunderstand things when the information doesn't come to you in proper sequence and context :-)
Best of luck!
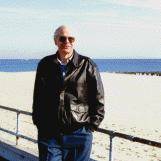
Ted Mooney, P.E.
Striving to live Aloha
finishing.com - Pine Beach, New Jersey
Eco friendly electroforming?
Q. Hi, this is Ornella from the RCA and I wanted to know if there is any kind of solution for electroforming in copper and silver that can be used and which would be not so bad for the environment? My work is based on this process but it is also related to Nature and I think it might be a bit paradoxical to use chemicals to say that we should take care about Nature … Let me know if you've got any suggestion. Thanks
ORNELLA IANNUZZIstudent - UK
2007
A. Hi Ornella. I don't necessarily see environmental harm from either of these processes. The potential environmental harm comes from misuse or mishandling of the process solutions, not from the electroformed object. But silver plating may only be practical from cyanide based solutions and they are quite dangerous to use, and only for the experienced, not for beginners. Copper should be fine, and if you need a contrasting color, maybe think of nickel rather than silver?
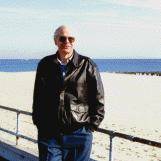
Ted Mooney, P.E.
Striving to live Aloha
finishing.com - Pine Beach, New Jersey
A. Acid copper electroforming is a comparatively harmless solution if compared with cyanide-based. As Silver electroforming solution you can use ferrocyanide bath (1% of cyanide toxicity and it works), phosphate bath (according to one ex-USSR handbook), or thiosulphate bath (according to one expired US patent) or you can buy proprietary bath. Hope it helps and good luck!
Goran Budija- Cerovski vrh Croatia
A. Ted is right. All plating solutions are harmless to the environment until they are wrongly used and processed and let loose into the environment. However, if you want to take account of the carbon footprint of the solutions, then you need to do a complete life cycle analysis and I am not sure this has been done in the chemical industry. Electroforming is a precise and delicate science that has taken many years to perfect. It is not possible to formulate a new electrolyte that is green (although nickel solutions are all green!) as the requirements are for specific deposit properties. The best electroforming solution for nickel is nickel sulphamate and for silver it is silver cyanide. The trick to making these environmentally green is to keep them away from the environment and have sufficient environmental protection that they cannot get in contact with the environment.
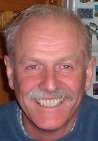
Trevor Crichton
R&D practical scientist
Chesham, Bucks, UK
Multiple threads merged: please forgive chronology errors and repetition 🙂
How to electroform copper anodes for spark erosion
Q. I want to make electroformed copper electrodes for spark erosion to make moulds for glass products with different designs. Can you suggest the method how it can be made, with the process and the know how? I am ready to enter into a technical tie-up or know-how transfer. Can you also suggest to me an alternate to make the designs in the moulds?
Parmanand P Acharyamouldmaker - Baroda , Gujarat, India
2003
A. In electroforming the basic principles involve the selection and special treatment of the mother surface to permit separation and a proper chemistry and plating parameters to produce very thick coatings without cracks, distortion or premature separation. From this very brief idea you can follow that you need a pattern with exactly the negative surface of the electrode (positive to the EDM mold surface). The rest is a matter of either years of personal research and involvement or the hiring of a professional in the field. One organization that could help you is The Nickel Development Institute.
Guillermo MarrufoMonterrey, NL, Mexico
High-Strength Electroformed Copper Parts
Q. I'm interested in electroforming parts to create small, intricate pressure vessels. I've read all about large liquid rocket engines using electroformed nickel and copper structures to produces parts that would be near-impossible to machine. Obviously these rocket engine structures withstand an incredibly high amount of thermal and mechanical stresses.
My project involves electroforming copper parts that must be able to withstand a fairly high level of stress due to pressurization. Although I've done a bit of research I've never seen anyone directly compare the mechanical properties of electroformed parts to those of raw machined stock. Will I be able to electroform parts capable of taking appreciable loads?
From what I've read in texts and in some of the finishing.com posts, the best mechanical performance sounds like it comes from pure, clean copper sulphate solutions with relatively low current densities. Is that correct?
Can someone recommend a good starting point for me to experiment with the plating solution and current levels? My part has roughly 0.6 ft^2 of area and I'm hoping to deposit roughly 0.120 inch of thickness. There is no need to produce these parts quickly so it is acceptable if it takes a long time to plate on the desired thickness.
Thanks! Finishing.com is an amazing resource!
-Ian
University of Southern California - Los Angeles, California, USA
2007
Ed. note: Thank you for the kind words, Ian. As you've already discovered, we at finishing.com personally contribute little of the technical expertise; we rely on the generosity of a good number of regular contributors. When you thank us, we trust that they realize that you are thanking them.
A. I think you should get a copy of the book Properties of Electrodeposited Metals and Alloys [affil link to Amazon or on AbeBooks affil links] , by W. Safranek. It's full of references to the properties of electroplated or electroformed copper (and other metals too) using different electrolytes and conditions. Also, mechanical work hardens copper (all kinds) and makes it more resistant.
Guillermo MarrufoMonterrey, NL, Mexico
A. Also get ASTM B832,
'Standard Guide for Electroforming with Nickel and Copper',
and a freebie, 'INCO NICKEL ELECTROFORMING PROCESSES AND APPLICATIONS' at www.inco.com/customercentre/nickelplating/science/pdf/EcopyElectroformingGuide.pdf
The above items together are basically an update of the Electroforming chapter in Electroplating Engineering Handbook ⇦ this on
eBay,
AbeBooks, or
Amazon [affil links]
, 4th Edn., although omit iron electroforming.
The Electroforming chapter in The Canning Handbook [on
eBay,
Amazon,
AbeBooks affil links], pages 573-590 (23rd Edn.), gives more information on plating Ni-Co alloys.
The Electroforming chapter in ASM Handbook, Vol. 5 Surface Engineering ⇦[this on
eBay ,
Amazon,
AbeBooks affil links]
, is short but gives more iron plating solutions and mentions periodic current reversal for producing fine-grained copper of excellent mechanical properties in greater thicknesses.
One probably can locate additional information by searching on the authors and titles of papers presented at the 1996 AESF & NiDI Electroforming Course & Symposium,
www.finishing.com/library/conferences/eform96.html
by K. R. Rao
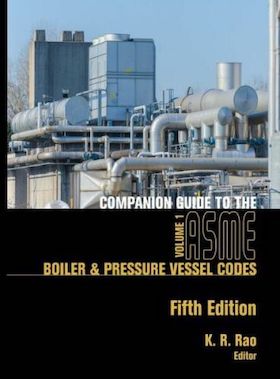
or AbeBooks
(affil link)
However, I have some doubt that an electroformed copper pressure vessel is permissible under the ASME Boiler and Pressure Vessel Code. Staying below 10 inches diameter will avoid the regulations.
Also, pure copper isn't very strong and suffers from creep when moderately heated, so normally isn't used for pressure vessels. The wrought Cu alloys typically used are alloyed with Ni, Sn, Al, Fe, Zn, Mn, etc.* and have annealed strengths 1.5 to 4 times that of pure Cu. For higher strengths, Cu can be clad onto steel.** The NASA rocket application requires extremely high thermal conductivity rather than high strength -- an oxygen-hydrogen combustion chamber is cooled by liquid hydrogen -- so the only alternatives to copper are silver & gold.
* ASTM B171/B171M, 'Standard Specification for Copper-Alloy Plate and Sheet for Pressure Vessels, Condensers, and Heat Exchangers,' and ASTM B96/96M, 'Standard Specification for Copper-Silicon Alloy Plate, Sheet, Strip, and Rolled Bar for General Purposes and Pressure Vessels.'
** ASTM B432, 'Standard Specification for Copper and Copper Alloy Clad Steel Plate.' "The material is generally intended for pressure vessel use but may be used in other structural applications where corrosion resistance or conductivity of the alloy is of prime importance."
- Goleta, California

Rest in peace, Ken. Thank you for your hard work which the finishing world, and we at finishing.com, continue to benefit from.
Ed. update, Dec 2016: As an update to Ken's incredibly generous bibliography & research ...
Inco is now a part of Vale which sadly seems to have abandoned the product stewardship that Inco was well noted for. Not only can't we find that particular article anymore but, unless we're missing something, zero of Inco's famous white papers about nickel plating are maintained anymore :-(
However, Gar Electroforming is currently maintaining a copy of that paper at
Download it while you can, product stewardship is apparently rather 'yesterday' for today's megacorps :-)
Ed. update, Oct 2023: Too late, garelectroforming.com doesn't exist anymore either. Thankfully, the fabulous Internet Archive preserved a copy here

Please consider a donation to The Internet Archive. Never follow broken/abandoned links, old URLs are sought out by hackers!
Treeing / burning only on bottom of electroformed objects
Q. Treeing and burning only on bottom side of acid copper electroformed objects? I am using a simple acid copper bath for electroforming on ceramics. It seems that no matter where I place the anodes, or how I agitate the solution, dendrites form much more on the lower portion of the object. They also show blackening unless I scale the current way back. I don't get it … the solution concentration should be the same through any vertical cross section of the bath, and even if I place the anodes higher than the center point of the object or move them away, the bottom still forms a denser dendritic growth (with blackening) than the top or sides. What am I not taking into account?
Robert Coyleproduct designer - Santa Fe, New Mexico, USA
2007
A. Hi Robert,
If this was high current density burning you would think you would be getting it at the top or at the point of rack/wire to part or outer edges. Because I don't know of your exact bath make-up, I can only suggest fixturing a copper thieving strip an inch or so below the part. If you can't incorporate the thief strip on the rack or wire you can hang the strip from the cathode bar with two pieces of copper wire for placement. This will help, and most likely eliminate burning. Good Luck!
Process Engineer - Syracuse, New York
A. Either the bottom of your anodes hangs well below the part, or you are getting stray current through something metallic which is below the part. Piping, heater, etc.
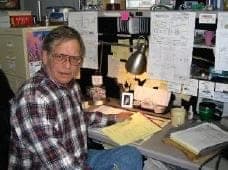
Jeffrey Holmes, CEF
Spartanburg, South Carolina
Q. I have tried raising the anodes so they are well above the midpoint of the object being plated. The geometry of the object doesn't seem to matter. I still plates selectively on the bottom side.
I am plating glazed ceramics that are somewhat acid sensitive so I am using a copper sulphate/acetic acid /boric acid solution that seems to plate well but doesn't attack the glaze as sulfuric or HCl would.
I did find a little anode metal precipitated out at the bottom of the tank. Maybe that's the problem? I'll clean it out and try again.
Thanks.
Bob Coyle
- Santa Fe, New Mexico, USA
A. I think that Mark is on the right track. Current will bounce off the floor of the tank and increase plate on the bottom. I also wonder if you have enough agitation in the tank.
James Watts- Navarre, Florida
Electroforming copper onto tin mandrel
for Artisans, Jewelry, Crafts
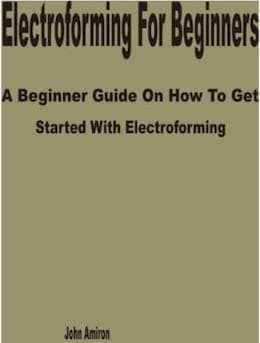
avail from eBay, AbeBooks or Amazon
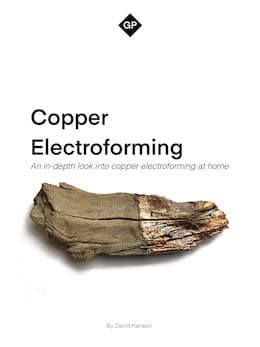
avail from Amazon
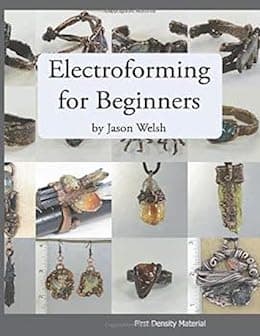
avail from Amazon
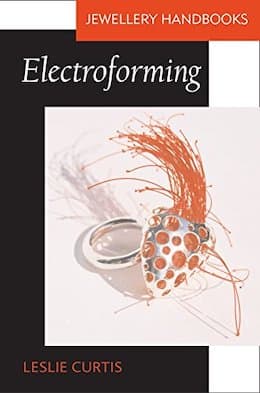
avail from eBay, AbeBooks or Amazon
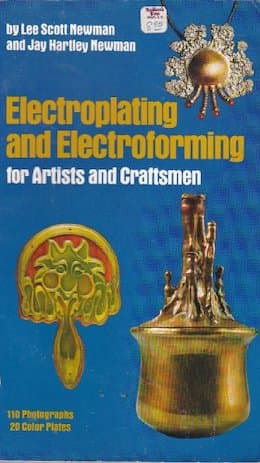
avail from eBay, AbeBooks or Amazon
(as an Amazon Associate & eBay Partner, we earn from qualifying purchases)
Q. Hello, I'm a Spanish artist. Sorry if my english is not very good. I'm trying to electroform a copper layer on a surface of tin. How can I do to passivate the tin? Nitric acid, chromic acid? For electroform a thick layer of copper on the surface of tin, Do I need an alkaline bath or an acidic bath? Has anyone tried the cyanide-free alkaline baths sold by hobby plating suppliers? Are there other options? Many thanks.
Antonio sanchez- spain
December 2, 2013
A. The most common copper electroforming electrolyte is an acid based one, using 200-250 g/l copper sulphate ⇦ on eBay or Amazon [affil links] with 50-75 g/l sulfuric acid; temperature about 25-30 °C and current density 2-10 A/dm2. Anodes are phosphorus deoxygenated and agitation is air or mechanical
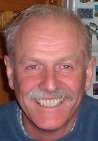
Trevor Crichton
R&D practical scientist
Chesham, Bucks, UK
Can electroform small wax objects but not big ones
Q. Hello everyone--
I am a sculpture artist who has built his own electroforming chamber up from a beaker [beakers on
eBay
or
Amazon [affil links] , to a gallon, to five gallons, and now I'm in the ten gallon range. I use lab-grade copper sulphate, brighteners, and car battery acid
⇦ on
eBay
or
Amazon [affil links]
as sulfuric acid. On a good day, I can get bright penny out of my chambers.
I've been having some pretty tricky problems of late, however, and I wonder whether they are due to the fact that I am a do-it-yourself outfit, or whether I'm missing something fundamental. The biggest is that my larger items--an object as big as a head/bust, and one of a hand/forearm--refuse to plate. With the one, I'm using Rio Grande's copper conductive paint, and with the other, I'm using a graphite paint--all to no effect.
Now, I have a technique where I sculpt a wax form, lay copper kitchen scrub pads over the object, and then electroform it from there--the result is that the threads turn into wires, then I evacuate the wax. I've had success putting the graphite paint in between the spaces between the threads, and they accumulate copper very nicely. Also have seen successful electroforming laying down paper letters on to a copper plate, varnishing the letters, and then applying conductive paint.
In a nutshell, I don't seem to have a problem when there is actual metal helping out--but failure after failure when I'm just using conductive paint over a large wax form.
Help! And very much thanks in advance!
Caldwell Sculpture and Design - Charlottesville, Virginia, USA
July 12, 2014
A. Hi Eric. I'm only half understanding your clever use of copper scrub pads, which is something I've never heard of. But I think I can guess what is wrong with your graphite-only or copper paint-only approach to large objects, and that is that the metallization can only carry a very low current without burning. When you are plating a small object the thinness and limited conductance of the graphite/paint isn't a severe limitation, but on larger objects it is. I think you need to find a way, whether it is with copper scrub pads or some other way, to bring electrical contact to many points so you don't have more current flowing through the metallization layer than it can sustain. Alternately, it may be possible to electroplate at a very low current density for a little while until you have a good conductive "shell" that can carry many times more current than the graphite "shell" … then you can up the current density to your usual values.
Regards,
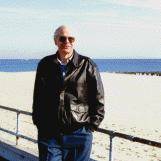
Ted Mooney, P.E.
Striving to live Aloha
finishing.com - Pine Beach, New Jersey
A. Good, usable and download free book on that subject is Die Galvanoplastik by russian german Moritz Herman von Jacobi (inventor of electroforming). Hope it helps and good luck!
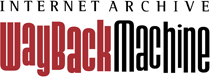
Very good old book in English (same subject):
https://archive.org/details/electrotypemanip00walk
Goran Budija
- Zagreb,Croatia
August 11, 2014
Q. Hi, I am trying to electroform some jewelry. I have some electroplating solution. Will it work as is to electroform? One person said yes, another said no. I can't find any information on the chemical difference. I bought paint from Dalmar and no plating stuck to it, but did stick to any metal I used in the pieces. I am getting very frustrated.
Please help!
- Cornville, Arkansas U.S.A.
August 5, 2014
A. Hi Sylvia. Electroplating/electroforming isn't necessarily easy. For some of the regular readers and visitors to this forum, electroplating has been their career for 50 years, yet they are still learning. So patience is a requirement.
Semantics: the difference in "electroplating" vs. "electroforming" is pretty simple: if you have an object and you put a thin coating of a metal on it (like the chrome plating on a truck bumper or the rhodium plating on a white gold ring), we call that 'electroplating'. But if the plating actually becomes the object, not just a coating on it (for example, hollow gold earrings which are made by plating gold onto wax which is later melted away), then we call it electroforming … simply because we've 'formed' an object.
When we electroplate onto a leaf or a flower, most people will call it 'electroforming', but it's a bit ambiguous -- is it a flower that has been plated, or was the flower just a form and the metal is the object of interest?
Yes, in general you can use electroplating solutions to do electroforming. But in every endeavor, tweaks are possible, and customizing to a given purpose can improve performance. A plating solution optimized for plating bright nickel will probably not be great for electroforming heavy layers because the metal will be very highly stressed. So those who say you should use 'electroforming' solutions are not exactly wrong either :-)
I don't know what kind of metallizing paint you used and what kind of plating solution you are using, and we have no other data, so it's hard to say why the plating isn't sticking to the paint. There could be a lot of reasons. But I'd suggest you practice plating on metal and become reasonably competent at it before you introduce plating onto conductive paint as yet another variable to tame. Best of luck.
Regards,
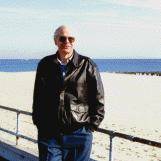
Ted Mooney, P.E.
Striving to live Aloha
finishing.com - Pine Beach, New Jersey
August 2014
Q. Thanks for responding. I am using Krohn's copper electroplating solution, and Delmar's copper conductive paint. The man at Delmar was very helpful, and said the electroplating solution should work. After many frustrating trials, I am now getting good results. I seem to be getting better results as the paint thickens; also, most of my problem was not getting good connections to all parts where the paint was. I am taking more care now.
I still wonder about my question about the difference between electroplating and electroforming copper solutions. Every recipe I find for either, seems to be the same. They never point out a difference in the chemicals. Maybe the ratios are different.
Thanks again,
Sylvia
- Cornville, Arizona U.S.A.
A. Hi again. Glad to hear of your improving success.
I tried to answer your question about electroplating vs. electroforming, but I'll try again:
Electroplating is usually (although not always) very thin. Gold or rhodium plating, for example, is usually well under a micron thick (40 millionths of an inch). But an electroform, since it is an actual usable object, is thousands of times thicker. The problems that may arise at this thickness include too much internal stress in the plating, which will causes the electroformed object to curl up. This is especially a problem in nickel electroforming, for which much different solutions are used than in bright nickel electroplating. But copper is a soft and low stress metal, and some copper plating solutions seem to be fine for both applications.
Luck & Regards,
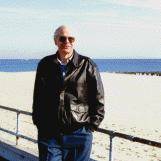
Ted Mooney, P.E.
Striving to live Aloha
finishing.com - Pine Beach, New Jersey
Thanks Ted, Believe me, I thoroughly understand the difference between electroplating and electroforming. My question was "what is the difference in the chemical make up of copper electroplating solution and copper electroforming solution that vendors sometimes insist you have to buy to copper electroform?" Is it just the same solution with two names?
If you want to make your own solutions, the same recipe for either are given, so what are these vendors trying to sell us to buy? In DIY tutorials, I keep seeing the recipes for copper electroplating when they are showing us how to copper electroform.
I am not having any trouble now electroforming with the copper electroplating solution, as the man at Delmar said it should work fine and it does.
Still curious!
- Cornville, Arizona
A. Hi again. A given copper sulphate bath can be used for both copper plating and electroforming, so those who say one bath is all you need are right not wrong. But absolutely anything can be optimized.
Canned coffee sellers offer this grind for Mr. Coffee machines, another for electric percolators, another for expresso, yet another for old fashioned percolators -- is it actually important to pick the perfect grind? Are we to believe that copper plating solution is the one thing that absolutely cannot be optimized for plating vs. electroforming? Certainly it is possible to put a brightener into a copper plating bath that is designed to make the plating hard and bright, but which will not be ideal in an electroforming bath.
It's just life that some will point out a distinction and call it important and others will call it a distinction without a difference :-)
Regards,
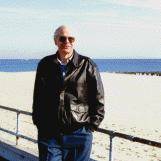
Ted Mooney, P.E.
Striving to live Aloha
finishing.com - Pine Beach, New Jersey
Q. Hi -
I have been electroforming both organics and onto cast metals for some time. I am now having a problem with the solution crystallizing onto my copper anode. I make my own solution with copper sulphate pentahydrate, distilled water, and acid. I have also found that the solution is evaporating very quickly these days. Any thoughts on either problem?
- Savannah, Georgia USA
November 15, 2014
A. Hi. Copper concentration tends to grow in acid copper plating, especially if you are plating at low current density, which is usually the case when electroforming. Are your anodes phosphorized copper? If not, that should help. Please see letter 848 for a good discussion of copper anodes. For now, you may have to dilute the solution to get the copper concentration down.
Regards,
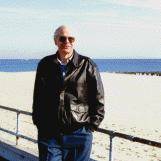
Ted Mooney, P.E.
Striving to live Aloha
finishing.com - Pine Beach, New Jersey
Q. I am a Costume Designer/Artist/Professor and I have been playing with electroforming a variety of materials for use in my designs. My boyfriend has been helping and last night he left the copper anode in the solution with nothing in it and no current on. He doesn't believe me that this is a BAD IDEA. Could you explain exactly why he should not do this? Aside from wasting copper, does is do any harm to the solution? Is there a way to clean it? Or do I even need to clean it?
Nola YergenArtist - Phoenix, Arizona, USA
November 11, 2015
A. Hi Nola. This is not generally considered harmful. Large plating shops almost always leave the anodes in their tanks all the time.
Regards,
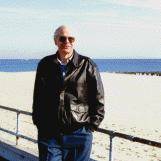
Ted Mooney, P.E.
Striving to live Aloha
finishing.com - Pine Beach, New Jersey
Q. I'm a recent fine arts sculpture grad and am looking to continue my path with sculpture by starting a small hand made jewellery business. I just wanted to check on the rectifier voltage and amperage before I purchase one, as well as the cathode.
For the rectifier I'm looking at either a 0-24 DVC and 15 Amp. However, since the rectifier is not digital would this be sufficient for copper electroforming? Or should I go with a lower amp that is digital which would be 0-30v 5amp? For my cathode I would be electroforming brass rings which I have read do not require a nickel plate as copper adheres well to brass. The brass ring will have a gem epoxied to the top, the epoxy will be painted with a copper conductive paint. I'd like a somewhat thick layer of copper to build around the ring and gem. Could you please let me know if I'm on the right track with the power of the rectifier and material of the cathode?
Many, many thanks,
Rachel
- Peabody, Massachusetts USA
January 16, 2016
A. Hi Rachel. The rectifiers you mention have far, far more voltage than you need. You'll almost surely never use even 6 Volts. And 5 Amps should be more than enough for any ring-sized object; Henry suggests 1/10 Amp per square inch of surface area and I'm confident that he's right and you should not exceed this.
I think you'll be able to plate onto brass substrates with reasonable adhesion from copper sulphate.
Regards,
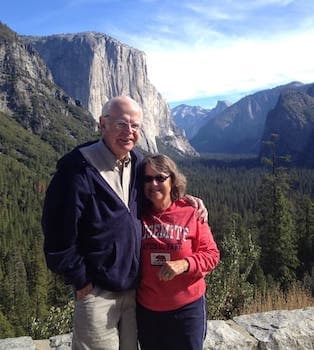
Ted Mooney, P.E. RET
Striving to live Aloha
finishing.com - Pine Beach, New Jersey
Copper electroforms were good at first but now they are grainy
Q. Hello!
Thanks for providing such an informative thread. I have had a recurring problem that I usually solve by buying more copper electroforming solution, but I have to wonder if there is a better way to resolve my issue. With my current bottle of electroforming solution I have produced roughly about 100 pieces of jewelry (none substantial in size) that have all turned out with such a great finish. Now they are coming out with the texture of sandpaper, if monitored frequently, and large forms or branches, if monitored less frequently. I am keeping my amperage low and I'm using Rio Grande's electroforming solution. Does it simply need brightener or should I play with different variables? I know temperature was mentioned as a variable in another Q&A, what is an acceptable temperature to electroform copper and how would you recommend regulating it? I also read that it's helpful to agitate the bath, could that be a possible solution?
Thanks so much for sharing your wisdom!
- Austin, Texas US
February 10, 2016
A. Hello Caitlin, there are a few causes for rough plating. Brighteners are a grain refiner for your deposit. After plating so many pieces it should be added by a certain amount of ampere hours. Your tech data sheet for the solution will give you that info. I find that a Cu sulphate bath plates/electro-forms best at 70-75 °F. If the temp rises, a small chiller or an easy method of cooling (your discretion). Another cause is organic contamination. I don't know the volume of your solution so maybe a small filter with a carbon pack for 2 hours maximum. The other common cause is particulate matter in the Cu solution. Filtering through a 5-10 micron filter will solve that. Depending on your anode setup if using small Cu anodes they should be bagged with polypro or Dynel bags. Do not use any bags with a cotton content. You have some measures available to you to keep the solution longer. Good Luck!
Mark BakerProcess Engineering - Phoenix, Arizona USA:
Q. I have been getting into electroforming, but have run into a few snags along the way.I have multiple questions.
1. I have a magnetic stirrer with heat. Is it better to electroform with warm solution or cold? (I get a better current when its warm)
2. What should the current and voltage be if I'm doing a bunch of small rings at once? It seems to more all over the place. Sometimes the current will just stop working all together in the middle of a plate. Any idea why?
3. I heard Root Kill is basically the same things as the solution you get at Rio grande. It this true and is it safe to use. It's 99.9 percent copper sulphate.
4. I've been getting some uneven pieces and am not sure why. I use gloves to touch the pieces to ensure there is no oil or dirt on them while I'm painting them, but seem to still have some places that won't plate. Any cleaning solutions I could try before I paint?
5. Do you know how to make your own conductive paint or glue. I can't find one that I like.
6. How often should I be changing the copper solution and anode?
Thank you for any info you might have :)
- Brooklyn, New York
March 5, 2016
Foam buildup from aerating my copper plating solution?
Q. Guten tag from lovely Rostock, Germany! I am an electrician by trade but also an avid fan of making copper jewelry. I was really excited to try out this crazy "electro forming" all the kids are talking about, and last week acquired the various bits and things I needed to get started. In my haste and excitement my first attempt was a total disaster, upon which I found and read through this forum. Thank you so so SOOOO much for all the great questions and answers! I actually literally found solutions to all my issues here! What a great resource!
I DO however have one question … I bought a small aquarium pump, but found that if I leave it on continuously, a layer of foam builds up at the top of my solution which left unchecked would flow over the top of my beaker. Do you have any suggestions as to how I may remedy this?
Also, since I am already asking questions, what is the lifespan generally speaking of the solution itself? Like, specifically if I am doing small pendants approximately 2 square inches of surface are for a time of 6 to 8 hours each at 0.2 amps … roughly how many times can I repeat this process before I require new solution?
Thank you again for all of your great help!
hobbyist - Rostock, Mecklenburg Vorpommern, Germany
March 13, 2016
A. Hello Ian. There are wetting agents made for air agitated plating baths to prevent this foaming; the supplier of your copper plating bath should know about them. Electroplating baths are "equilibrium processes" which are designed to -- if all goes well -- run forever; in industrial applications, copper plating baths are filtered, and various purification steps are taken as needed, and the plating bath is almost never dumped and re-made.
If your library has a copy of The Canning Handbook.
it has a good chapter on copper plating, and another good one on electroforming.
Regards,
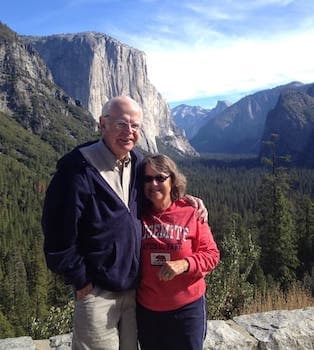
Ted Mooney, P.E. RET
Striving to live Aloha
finishing.com - Pine Beach, New Jersey
Q. Hello I just bought a rectifier to start electroforming/electroplating copper onto geode stones. I know of the materials I need, but I do not know what is the difference between bright copper electroforming solution vs. Bright copper electroforming with Acid. What is the purpose of the acid? Do I need it? Thank you.
Julie afzali- brooklyn new york USA
March 8, 2016
A. Hi Julie. I suspect that nobody except the particular vendor who is offering that solution can tell you what it means. Both solutions are probably "acid copper sulphate" based.
Regards,
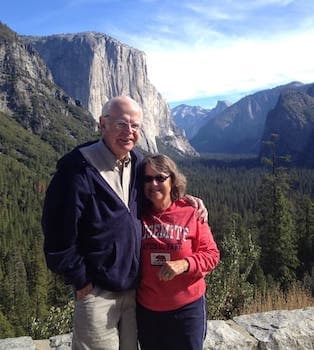
Ted Mooney, P.E. RET
Striving to live Aloha
finishing.com - Pine Beach, New Jersey
Q. I recently moved. When I did, I bottled all of my electroforming solutions in their original bottles and boxes, packed them away and had hopes of reusing the solution once I got my studio back up and running.
I am using a small 1 gallon fish tank to electroform which uses a fish filter/air pump for agitation. I am using silver conductive paint and a large piece of copper for an anode. In the past (after the first hour) I could see the plating happening and could just let it do its thing. My piece has been in the bath for over 12 hrs now and has barely any plating, and that is salmon in color. It seems to be happening a lot slower than in the past. Although I switched the containers I was using, they are the same size and material so that doesn't seem like it should create any problems. Do you have any idea what could be the issue? I guess I'm going to let it keep going but its highly frustrating. Do I need to add acid to the mix? Please help!
Alexandra CamachoArt/jewelry - Los Angeles, California, US
March 21, 2016
A. Alexandra: It sounds like you are getting little if any current flow. Check that all electrical connections are clean and tight. It would be best if you had an ampere meter, but even a simple DC volt meter will help. You can pick one up at a big-box hardware store that will read low voltages. Depending on your setup, you'll probably need 2 or 3 volts. Or if you can measure amps, maybe 4-8 amps per square foot of surface being plated.
Are you certain you don't have the connections reversed?
(+) to the anode (-) to the part.
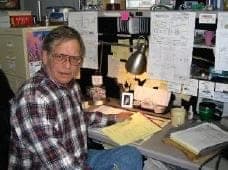
Jeffrey Holmes, CEF
Spartanburg, South Carolina
Q. Thanks for responding. I use a digital rectifier and I always have used it on the lowest setting and has worked fine for 1-3 pieces up until the move. I turned it up to .85 and the the other setting changes along with it to compensate I guess? Do I still need to check the amps and volts if it's showing current on my rectifier?
Alexandra camacho [returning]- Los Angeles, California
(you are on the 1st page of the thread) Next page >
Q, A, or Comment on THIS thread -or- Start a NEW Thread