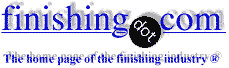
-----
Zinc plating wastewater? Best pH?
Q. Our company paints and Zinc plates automotive parts. We usually segregate the waste water from both the departments. But by accident, all the water got mixed up, and now we are having problems with the precipitation of Zinc. By the way, we use hydroxide precipitation to remove metals. We have been able to get down the Zinc concentration to 4 ppm using various chemicals, but not any lower than that. Our discharge limits are 2.61 (daily) and 1.48 (monthly).Various chemicals we tried : caustic soda ⇦liquid caustic soda in bulk on Amazon [affil link] , Lime, Magnesium oxide, ferrous sulfate ⇦ on eBay or Amazon [affil link] , Calcium chloride, Sodium borohydride, Calcium polysulfide, two proprietary organometallic polymers. Any suggestions will be highly appreciated. Thanks in advance.
prasad s [last name deleted for privacy by Editor]information service
1995
A. I assume these values are after filtration, Prasad?
If not, your problem is easily solved -- you need to clarify or filter the wastewater.
My personal experience is that sulfide chemistry is often the most powerful precipitating method for zinc, like calcium polysulfide, DTC (sodium diethyl dithiocarbamate) or Degussa's proprietary TMT15.
For this one-time troublesome batch, I suggest trying to lower the pH to about 5 and loading it up with your ferric chloride
⇦ on
eBay or
Amazon [affil link] before raising the pH for the hydroxide precipitation. Filter out the precipitated zinc. Now treat the filtrate with the proprietary co-precipitant and the polysufide, DTC or TMT15. Naturally, do jar testing of this idea committing the whole batch. before Good luck.
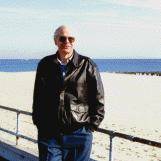
Ted Mooney, P.E.
Striving to live Aloha
(Ted can offer longterm or instant help)
finishing.com - Pine Beach, New Jersey
Q. Dear Mr. Mooney :
Thank you for your reply. I forgot to mention, but we tried the carbamate too. Yes, we are filtering the effluent. Since my last letter, we had successfully precipitated out zinc using Magnesium Oxide and a proprietary organometallic polymer 326-C. But now we are having problem removing Nickel. This is not caused by 326-c. We had the problem with Nickel to start with. One more chemical we tried in the last couple of days is ferric chloride
⇦ on
eBay or
Amazon [affil link] at around pH 8.0. Please suggest any chemicals to remove Nickel and at what pH, they work best. Thanks again for your reply.
-Prasad.
information service
A. Hi, Prasad.
1). When you describe all these things they you have tried, they hopefully were each tried on a small sample of the waste. You should never attempt treating the whole batch without lab scale beaker tests first to verify that they work, or you may end up with a large volume of witches' brew that already contains large amounts of a half-dozen different precipitants, and it just keeps getting harder and harder to treat.
2). After most of the metal has precipitated out, you must get rid of it by filtering it before going on to deal with the remaining dissolved metal. If the precipitated metal remains in the batch you are working with, constantly ready to redissolve into equilibrium, you will never get there. The strong sulfur based precipitant will remove a molecule of zinc, but if the waste was not filtered, a molecule of zinc formerly precipitated with hydroxide just goes back into solution to replace it. So you must hydroxide treat, filter it, and then sulfide treat only the remaining unprecipitated zinc and nickel.
3). In general, nickel precipitates best at high pH, about 10.5. When magnesium hydroxide is used for the treatment of nickel it has to be 'topped off' with caustic or another stronger alkali because magnesium hydroxide doesn't get the pH high enough. See letter 565 for starters.
4). You need a treatment sequence and strategy, not a hunt for a miracle precipitant. For example: lower the pH, add ferric chloride
⇦ on
eBay or
Amazon [affil link] , raise the pH, add flocculant, and filter out most of the zinc. Now you take the clear effluent and raise the pH further to remove the nickel, and filter it. Now you are left with a few ppm of zinc or nickel still in solution, and you add a few ppm of a powerful sulfur based precipitant to precipitate it.
It is probably unaffordable and environmentally hazardous to try to remove the bulk of the metal with strong sulfides like polysulfide or DTC! America's worst pollution incident in the electroplating industry (White River, Indiana) had nothing at all to do with a plating process or a discharge of untreated or under-treated plating waste … rather it was a gross over-discharge of the wastewater treatment chemical DTC. If you must use DTC, use it only as a final polishing treatment after almost all of the zinc has been removed and is no longer in the treatment tank.
Good luck!
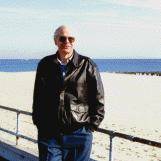
Ted Mooney, P.E.
Striving to live Aloha
(Ted can offer longterm or instant help)
finishing.com - Pine Beach, New Jersey
A. Try 3 separate tanks, bring the pH to about 6.5 in the first tank while adding the ferric chloride ⇦ on eBay or Amazon [affil link] ; then in the second tank raise the pH to about 9.2-9.5 try aluminum sulphate in this tank; then in the 3rd tank (typically a smaller tank then the first 2) meter in the polymer and run through a clarifier/filter press. There are many things to take into consideration … the flow of the water and how fast the coagulant/flocculant chemicals are feeding, I do not deal with nickel but our effluent numbers are usually below 1 mg/l.
Jake Skinner- Clinton, Iowa, U.S.
May 2, 2013
Q. Our company is a manufacturer of latex paint, and we are looking to install a filter press to reduce our wastewater disposal costs. We also have an issue with zinc contaminants, as we have trouble flocculating it to below 3 ppm. The filter press will likely require a wastewater pretreatment stage to improve performance, probably some sort of surfactant. I am wondering if there is a surfactant that will also precipitate the zinc. If anyone has experience with this, I appreciate your help.
Mike Rompala- Garland, Texas
2000
A. I maybe can help. I have experience treating zinc to 0.5 ppm. If I could get more information?
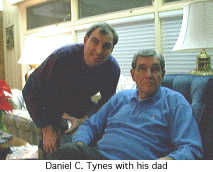
Danny Tynes
used electroplating equipment
- Birmingham, Alabama
A. In your case I would advise a filter press with a post treatment to remove the last few ppm of zinc. Concentrate from the post treatment can be recycled to the pH-adjustment before the filter press. This always ensures low zinc level in the effluent and results in a lower moist content in the filter cake, compared to the use of flocculants, surfactants and other additives.
Ruud Gerritsen- Simpelveld, Netherlands
A. Yes, filter press will responsible for the receiving water only, that is, the wastewater need to be treated before filtering.
pH adjusting is also a method for thickening the solids and shifting those tiny ones to bigger ones; is it possible to add flocculant agent?
Or just discharge the wastewater to tanks to check its thickening conditions?
The smallest ones are the key point "role" during filtering, as it will stay on the filter cake growing side or filter cloth side for cake building.
- Hangzhou, Zhejiang, China
May 17, 2011
Why High Zinc Levels in Wastewater
Q. I am searching for possible causes of High Zinc Level readings in our waste water. I have had the incoming well water tested with normal readings. Our effluent has the DEQ concerned. We have covered all of the chemicals used in house with the manufacturers and MSDS's. I have walked the plant and looked at all possibilities. The only thing odd I have noticed is we have a few of our indoor Air Conditioner units condensate drain into the sinks. Could this be a possibility?
Thank you for any help,
Paul Dofermire- Front Royal, Virginia, USA
2003
A. What is it that you do at this plant? I would not think that you would get high zinc from AC condensate, as most heat exchangers in AC units are aluminum, not zinc treated metals.
Perhaps a facility walkthrough with a water treatment engineer familiar with metals and treatment might be of help?
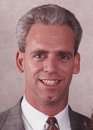
Tom Baker
wastewater treatment specialist - Warminster, Pennsylvania
Q. At what pH value we have the best precipitation of Zinc in a wastewater?
Sergio Zeni- Montevideo, Uruguay
2007

A. It's not quite as exacting as that, Sergio. According to the famous EPA chart that people have been both relying upon and laughing at for 3 decades, it's about 10.2. I think in practice it's been more like 10.5 for typical zinc-bearing electroplating wastes. The thing is, the "common ion" effect shifts it quite a bit based upon what other metals are in the waste solution.
So please remember to design the system only after jar tests with the specific waste. Good luck.
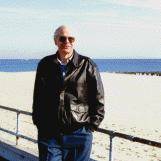
Ted Mooney, P.E.
Striving to live Aloha
(Ted can offer longterm or instant help)
finishing.com - Pine Beach, New Jersey
by Clarence Roy
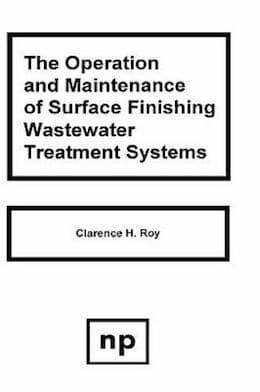
on eBay or Amazon
or AbeBooks
(affil link)
A. Optimum pH for precipitation of zinc as zinc hydroxide is 9.45 from my experience. Above this pH zinc effectively comes 'back' into solution as a zincate Zn(OH)4 - - ...thus causing a rise in zinc concentration in your effluent outfall.
Hope this helps!
- Glasgow
Q. Hi, I am investigating a problem with too much zinc in effluent.
The site produces metal ceilings; they are consistently over the 2 mg/liter on their consent. The zinc contaminates the water when washing the perforated metal prior to painting (powder coating).
They have an effluent treatment system in place which is:
Caustic (to bring pH up to between 9.8 - 10.5)
34% ferric chloride
⇦ on
eBay or
Amazon [affil link] (as the coagulant) made up to a 1000 L solution.
They then have one 18 m3 tank with weirs to help clarify.
But this does not work. Zinc is still over. Any ideas?
- UK
January 24, 2018
A. Hi Craig. Step 1 is to simply take a sample and tell us the Zinc concentration before and after filtering it. If there is a lot of dissolved zinc, we will have to talk about the source and the chemical treatment. If the problem is poor clarification, that's something else. Get back to us.
Regards,
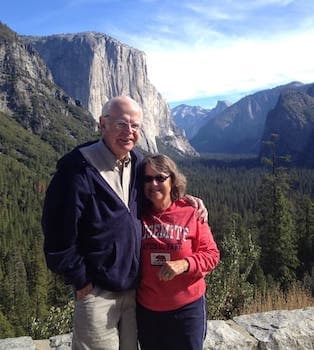
Ted Mooney, P.E. RET
Striving to live Aloha
(Ted can offer longterm or instant help)
finishing.com - Pine Beach, New Jersey
A. Try 9.2 to 9.5.
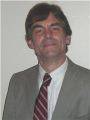
Dave Wichern
Consultant - The Bronx, New York
A. Hello Craig,
As Dave said, pH values around 9 are better for zinc precipitation. ferric chloride
⇦ on
eBay or
Amazon [affil link] alone is not the best way for metal precipitation, I would use an anionic polymer after you add the ferric chloride
⇦ on
eBay or
Amazon [affil link] and adjust pH.
And most important:
1 - First add ferric chloride
⇦ on
eBay or
Amazon [affil link]
2 - Adjust pH
3 - Add polymer
ferric chloride
⇦ on
eBay or
Amazon [affil link] is always acid, so if you adjust pH before adding it, pH values will be not consistent and you will have problems as you are experiencing.
First of all, see if the step order is correct. If it is, try adding a polymer.
Best of luck!
TEL - N FERRARIS - Cañuelas, Buenos Aires, Argentina
February 14, 2018
Effluent from paint manufacturing is not clear after treatment
Q. I treated an effluent for a paint manufacturing company of about 8000 l and it wasn't clear enough; I used ferrous sulfate
⇦ on
eBay or
Amazon [affil link] , polyelectrolyte, hydrated lime and chlorine. But didn't use alum.
Please someone should help me out want to prepare an SOP.
Environmental consultant - Ikeja Lagos Nigeria
April 17, 2018
A. Hi Newton. An SOP is important, but treatment strategies must not come from calculations of theoretical "textbook" reactions but by scaling up from beaker tests. It's a fundamental rule that you always try treatment strategies on a one-beaker volume, never on the 8000 liter batch. Only after you know that a strategy will work do you scale up from beaker size to 8000 liters because you definitely don't want to formulate 8000 liters of witches' brew, and anything you add to the batch has the potential of just making things worse :-(
Have you filtered a sample to determine whether the coloration or turbidity is filterable or not? Also, you have told us the names of the chemicals you employed, but can you tell us your treatment sequence and its general rationale? Thanks!
Regards,
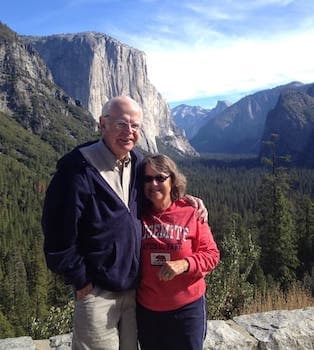
Ted Mooney, P.E. RET
Striving to live Aloha
(Ted can offer longterm or instant help)
finishing.com - Pine Beach, New Jersey
April 2018
Q, A, or Comment on THIS thread -or- Start a NEW Thread