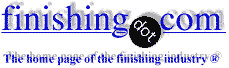
-----
Medical Device Chrome Plate over Zinc Question
2001
I want to explore my options of improving a decorative chrome finish on Zamac 3 zinc to prevent corrosion. This is a medical device that comes in contact with the skin and is cut upon by a doctor. The worst environment the device will experience will be 255 °F steam-autoclave, rotofinishing and ETO sterilization.
The corrosion usually begins where the rack contacts the device. I was thinking of hanging the device from an existing hole. The hole must have a proper coating. I can modify the mold and add another hole and use it instead if you think the plating would be compromised. My thought was hanging parts can swing/move in the bath. This movement would allow the various coatings to plate under the contact point.
I have not optimized the individual plating thickness. What thickness would be a good start for each layer?
- Copper strike
- Copper plate
- Nickel plate
- Chrome plate
- Copper plate
How much should be milled off before plating?
Is there a better chemical solution/bath of the metals compared to another?
Thanks,
P.S. Great Web Site!
Gary G [last name deleted for privacy by Editor]- Howell, Michigan, USA
A. You should look at the ASTM std for the plating thickness on ZDC that gives the optimum results. I don't know the std but it would be in the ASTM Volume 02.05. Typically 0.1 mil of Cu strike followed by a min. of 0.3 mils of Cu plate and 0.5 mils of bright Ni plus 0.00001 mils of Cr. To make the parts last longer you should look into plating semi-bright nickel and microporous Cr. Also the minimum amount of rack area the more plating in that area.
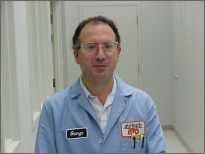
George Shahin
Atotech - Rock Hill, South Carolina
2001
A. You might also want to look at adding a high sulfur nickel layer in between the bright and semi-bright nickel layers. This extra layer increases corrosion resistance.
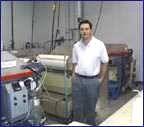
Tim Neveau
Rochester Hills, Michigan
2001
A. Hi. Most people think you should not mill zinc die-castings because of porosity if the skin is penetrated. However, New Brunswick Plating [a finishing.com supporting advertiser] is widely known as a precision plater of die-castings and for their contrary opinion that diecastings should be chemically milled before plating. You might contact them regarding your "milling" question.
Regards,
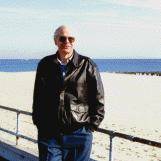
Ted Mooney, P.E.
Striving to live Aloha
(Ted can offer longterm or instant help)
finishing.com - Pine Beach, New Jersey
![]() |
A. Stop worrying about lack of plating at the contact points or where to put them. Use 0.002" of electroless nickel and, if you like it to be whiter, chrome plate it on top with standard decorative chrome. I know there are very few finishes that can compete with this in durability and complete coverage. Guillermo MarrufoMonterrey, NL, Mexico 2001 A. Show the part to a rack manufacturer, and tell him the problem. You should be able to plate part of the plating, then turn the part slightly so the rack tip contacts another area, then plate again. You could also wire the part, Plate some of the thickness, then unrack, and rewire in another area. Something like that has been done for many parts that did not allow a rack mark. The rack mark can be made very small indeed with the right configuration of rack tips, wiring, etc. ![]() ![]() Tom Pullizzi Falls Township, Pennsylvania 2001 |

Q, A, or Comment on THIS thread -or- Start a NEW Thread