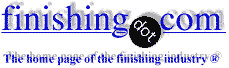
-----
Black coatings in the far infrared for space applications
Q. Hello,
We are interested in getting a coating that has low reflectivity, i.e., appears "black" in the far infrared. The wavelengths of interest are 200 to 670 microns. In the past, people have used a carbon suspension in epoxy, but these coatings tend to flake off, which is a no no for space applications. The process must leave a coating that is durable, and must not flake or bubble off from a temperature range of 4 to 350 K. (Yes, 4 Kelvin!)
I would like to add more information to the described finish. Other "black" coatings used for this application use particle sizes on the order of 1000 microns and is very heavy, on the order of 0.4 g/cm^2. We would like to find a coating that uses smaller particles and is lighter.
One last clarification. We are trying to coat the surface of a piece of aluminum that has been chemically converted to prevent corrosion.
Thanks for your help.
Robert Deschambault- Cambridge, Ontario, Canada
2001
A. Mr. Deschambault:
It appears to me that you won't find anything better than black nickel over an initial layer of electroless nickel (EN). Absorptance 0.87/0.91, IR Emissivity 0.07/0.10. EN adheres beautiful to aluminum and will give the black nickel top coat an excellent base to withstand low as well as moderate temperatures and vacuum. Perhaps the new developments in formulations for black chrome give slight better reflectance values but you will have trouble finding a contractor that gives you adequate covering an adhesion to aluminum. May I recommend you to refer to "The Properties of Electrodeposited Metals and Alloys" ⇦ this on eBay, Amazon, AbeBooks [affil link] by W. Safranek, 2nd Edition by American Electroplaters and Surface Finishers Society.
Good luck.
Guillermo MarrufoMonterrey, NL, Mexico
2001
A. Dear Mr R,
An alternative to epoxy based coatings is sputtered carbon based PVD coatings, other possibility is MoS2 based coatings, both of which are black, but I do not know which has better emissivity characteristics in the desired light range. These coatings do not rely on binders to give adhesion but on superior surface precleaning and vacuum etching to clean the substrate surface. These coatings can be made adherent to most metallic surfaces. Spallation may be a problem if the base material has phase changes in the indicated temperature range, but does not depend on the coating.
Such coatings are used for heavy duty tool and solid lubricating applications, so most likely will also withstand your low-load applications.
Ynte Stockmann- Venlo, Netherlands
2001
A. I disagree with the other answers. A method is discussed in Metal Finishing recently page 27 "Electrolytic Coloring of Anodic Aluminum for Selective Solar Absorbing Films. The method refers to mechanical polish (emissivity/enthalpy is 8 compared to 20 for blackened surface, but it's a fair sacrifice if you need to absorb VISIBLE light too). The key to the coloring of the based etched aluminum (using caustic soda ⇦liquid caustic soda in bulk on Amazon [affil link] ) is chromate, I am looking into the exact chromate used -- I think nickel chromate. If you look at diffusivity of nickel, it is very low for a metal, hence it lets infrared tunnel into the aluminum (that's the reason for the what is essentially corrosion induced by chromate additives). Nickel is nearly as low diffusivity (h^2) as water, so large temperature differences cause it to react quickly. Values of UV/VIS in 350 to 2500nm using Lambda 19 Perkin Elmer spectrophotometer are in excess of .96! Notice that no metal nitrides or oxides are used at all like the low-E coatings used on window rigid or flexible coatings.
John Holsen- Valders, Wisconsin
2002
Q, A, or Comment on THIS thread -or- Start a NEW Thread