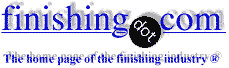
-----
Mechanical stress/cracks in thick copper layers
Q. I do copper electroforming on complex three dimensional substrates. A conductive starting layer is realized by chemical copper deposition. Subsequently the substrates are reinforced with a two step plating process. 1st step is a thin copper bath at 2 A /dm2 current density for 30-60 min and 2nd step is thick copper plating in a special bath running at 5 A/dm2 current densities for about 12 hours. I require at minimum 500µm copper layer thickness, therefore the long plating time is required. The problem is that the thick copper layer seems to be brittle on certain spots of the substrate and cracks occur.
Can a wrong brightener or leveler concentration be the reason for that? Has anybody experience in mechanical stress phenomena of such thick copper layers? Would pulse plating be a possible solution of this problem?
Please feel free to send me your remarks and amendments!
Regards,
- Graz, Austria
2001
A. Why don't you try acid copper without any brightener? You can build good thickness without any problem.
Payal Mag- Charlotte, North Carolina
2001
A. Have you tried heating the material after the first electroless plating? I read somewhere that hydrogen builds up during that process that can be removed by heating.
Richard Helzermqn- Newburgh, Indiana, United States of America
2001
A. I would try using a brightener system developed for the printed circuit board industry. Although the current density might be a lot less than what you are currently using these additives were developed to alleviate the problems you are describing. The other answers posted are perfectly good and viable options also.
Rick Richardson, MSFDayton, Ohio
2001
Q, A, or Comment on THIS thread -or- Start a NEW Thread