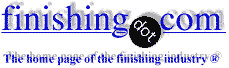
-----
Discussion about the MP&M
Now MP&M is a big topic for our world. When I read the document from the EPA, they specify the microfiltration for the newly opened metal finishing shop. I understand the process generate the reject water. In other word if I discharge 3000 GPD, I always have 1000 GPD reject water. They did not suggest any solution for this. We do not have any small amount exclusion either. Is anybody have the answer for this. The reject water should be treated with chemically. Then the water will the cause of the violation under MP&M.
Stephen Lee- Chatsworth, California
2001
Microfiltration returns the reject water to the feed tank. When the sludge in the feed tank gets thick enough the slurry is run through a filter press. The filtrate water from the filter press returns to the head of the treatment process.
Your water losses are therefore only what goes out with the sludge, or through evaporation. Everything else goes through the MF membrane and out the door.
If I can find or draw up a decent flow diagram I will send it in and I'm sure the finishing dot com guys will figure a way to display it.
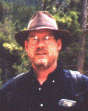
Bill Vins
microwave & cable assemblies - Mesa (what a place-a), Arizona
2001
If the reject returns to feed tank and the feed water become thick, I see some problem in pump selection. We need about 100 psi to use membrane. I think it will cause some problem for the feed pump. I see the problem in feed pump strainer. I might need to clean every minute.
Stephen Lee- Chatsworth
2001
Typical microfiltration systems in the metal finishing industry operate at between 20 and 50 psi. There are numerous systems currently in operation that have been running for a number of years. Cleaning frequency is anywhere from once a week to once every couple of months.
The technology is not new and is very proven for this application. The problem is using the right membrane with the right diameter tubes.
There are many companies proposing the use of small diameter tubes in this industry and they just don't work. If a system is built using 3/4" to 1" diameter membrane tubes, then the operational problems (clogging & cleaning) are minimized and high pressures are not required.
Stephen Bell- Lowell, Massachusetts
2001
To get the high pressure the choice is only centrifugal pump. The pump should be multistage (3 or 4 stage). Then we need to use suction strainer. The thick fluid can be problem for the strainer. I imagine the pump is more than $1500.00/ea. Can I use diaphragm pump ? I wonder the pulsating action of the pump can cause the problem to the membrane.
Stephen Lee- Chatsworth, California
2001
Actually, the use of smaller diameter tubes allows a smaller pumps size. Crossflow microfiltration systems operate on the concept of tangential crossflow velocity to keep the layer of solids down to a minimum thickness, therefore allowing good permeability at what is called a trans-membrane pressure differential (the difference in pressure between the feed side of the membrane and the permeate side of the membrane). Larger diameter tubes (3/4" - 1" dia) require a significantly higher horsepower to achieve the velocities required for good crossflow velocity. We can push upwards of 80 GPM of permeate through our system at 45 psi feed pressure with a 20 HP pump. Most of the larger tubes require 30 - 40 HP to even come close to it. The problem of "solids or plugging" is a sales pitch - as any solids greater than 5.5 mm or larger are easily captured in a strainer prior to the pump. In 22 years of using microfiltration membranes, I have yet to see one plugged by incoming debris that was not easily removed - that's over 300 systems in the US alone.
Another advantage of the smaller tubes is the ability to be backpulsed - reversing the flow from the permeate back through the membrane to the concentrate side to push solids off the membrane. Large diameter tubes cannot do this due to the lack of self supporting structural integrity. Therefore, they are either chemically cleaned more frequently or you send these cute little foam rubber balls cascading down them to - hopefully - remove the solids from the side walls.
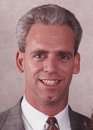
Tom Baker
wastewater treatment specialist - Warminster, Pennsylvania
2001
Q, A, or Comment on THIS thread -or- Start a NEW Thread