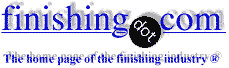
-----
Tin Wiskers Pest
I was reading some information on "tin pest". Is this the same as tin wiskers? Has anyone ever tried a Hot Tin Dip process instead of electrodeposited tin? The part is actually submerged into a pure tin molten bath. It is my understanding that Hot Tin Dip will reduce/eliminate the "wiskering" problem.
John Bowers- Everett, Massachusetts
2001
Hello John,
Tin Pest is different to Tin Whiskers. Tin Pest is the change from the usual beta tin to another allotrop, alpha or "grey" tin. It usualy only occurs to very pure tin or at very low temperarures. Tin Whiskers are crystals of tin that grow out from a tin deposit some time after the tin has been plated. Small additions of lead or bismuth (o.o1% or something) should stop it. I realy don't see the method of plating affecting the occurance of whiskers, and it seems that it may be fairly rare anyway. Ian Brooke search about on this site for more about tin pest, I know there's a few letters. And whiskers have been mentioned too.
Ian Brookeuniversity - Glasgow, Scotland
2001
I first met tin whiskers in the 60s.
Electro tinned brass used in avionics ( no DC voltages present\) sealed in dry nitrogen.
Grew whiskers up to 1cm! in a year or so in a very benign environment. Shorted out time and time again over a period from months to years.
We were told that the solution was to electro tin and flow. I have used glass to metal hermetic sealed panels which were electro tinned and flowed with no similar problem.
I have yet to see snslysis of alloys optimised to eliminate these problems and also optimum heat treatments to "flow " tin alloys.
I suspect heat profiles for soldering surface mount components will become valuable proprietary information.
design - Devon, UK
2006
Q, A, or Comment on THIS thread -or- Start a NEW Thread