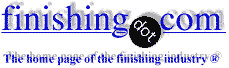
-----
Electropolishing Ti-6Al-4V Round-Bar Fatigue Specimens
2001
Q. Dear Finishers --
I searched your slick search engine and found nothing overly helpful--didn't want to be the 10th person to ask this question. Looks like I may be the first.
BACKGROUND
I'm a graduate student studying metal fatigue--currently working with that workhorse titanium alloy, Ti-6Al-4V.
As you probably know, surface finish is a variable that greatly affects fatigue life. It is common, therefore, for us to electropolish our specimens prior to testing. The specimens are 4-inch-long 1/2" diameter cylinders, threaded on the ends, filleted to a reduced-diameter middle section. We mask the threads and just polish the reduced-diameter middle section (which can be pre-polished to nearly any mechanical finish with a Dremel ⇦ on eBay or Amazon [affil link] ).
Usually we get our electrolyte recipes and polishing parameters (volts, amps, temp, agitation, miscellaneous tricks, etc...) from someone in the building who's already solved the problem. There is nobody around who has solved my problem.
Failing such convenient assistance, we read books (I have ASM Metals Hdbk, Tegart, VanderVoort ⇦[this on Amazon affil links], and Brammar & Dewey [on Amazon affil links]) and experiment with published recipes. This is not working for me, though. I have many recipes; I always get lousy results. I'm trying to study fatigue and all I ever do is wash dishes, mix dangerous chemicals and bottle up waste. It's making me crazy.
Best results thus far are with sulfuric + hydrofluoric + glycerin at 20 V, room-temperature, no agitation--but it only polishes near the surface of the beaker and it dissolves everything I have tried for masking the threaded ends.
THE QUESTION (you guessed it already, though)
Does anyone know of a published recipe for polishing this Ti-6Al-4V alloy that they have tried with success?
THE CAVEATS AND CONCERNS
I'd love to avoid "perchloric acid/acetic anything" mixtures because of their explosive tendencies, but I'm willing to be extra careful if it means I can get on with my research.
I'd also prefer (again, though, beggars cannot be choosers) to be able to use a stainless steel counter electrode. My lab has nice cylindrical ones that fit neatly around our specimens to help assure even polishing from all sides. I don't have any Ti tubing, but I'll buy some if I have to.
My research budget cannot handle contracting anyone to polish for me, nor can I afford any elaborate new equipment. I have several fine power sources, a stockroom full of chemicals/glass/plasticware, platinum gauze, ice, liquid nitrogen, a fume hood, and a magnetic stir plate. My group has polished a lot of different metals with the same equipment.
THE THANKS
Thanks to anyone who can help me out. All I can really offer in exchange is publication credit and an open offer to help with any metal fatigue questions that may arise in your work and/or studies.
Yours sincerely,
Andy W [last name deleted for privacy by Editor]- Philadelphia, Pennsylvania, USA
2001
A. Dear Finishers --
Months have passed and I've basically figured it out. Since nobody offered any assistance, I gather that none of you know how to polish Ti-6Al-4V. Here are the lessons I have learned--these directions give a shiny finish, though microscopic examination reveals differential attack of alpha and beta (so I probably won't be able to use this recipe for my work--still looking for a good alpha-beta polishing recipe).
Electrolyte lifted from Vander Voort (ASM-): 60 mL of 60% perchloric acid; 390 mL methanol [affil link]; 350 mL ethylene glycol. Several of his Ti electrolyte solutions are similar to this one.
Counter electrode: Stainless steel.
Temperature: Electrolyte should be in equilibrium with an ice bath (around 5°C).
Agitation: Gently stir electrolyte with stir bar (for temperature control); rapidly agitate working electrode (refreshes the polishing layer, I imagine--you get pitting and scale formation without this agitation).
Voltage: 38 V (draws around 10 Amps for my specimen geometry).
Time: Absolutely no longer than 15 seconds (unless you are interested in forming a lovely purple scale, pits, ugly grey scale, or a matte finish). This 15-sec polish takes away 600-grit sandpaper scratches. Fewer than 15 seconds will also work. Toy around with the time if you're worried about wasting electricity.
Trick One: Remove sample from electrolyte under voltage, then immediately plunge it into room-temp distilled water and stir (i.e. agitate sample slowly).
Trick Two: Wipe working electrode with acetone ⇦ on eBay or Amazon [affil link] Warning! Flammable! and air dry before polishing. If you need to polish longer than 15 seconds, you must stop at 15 sec, rinse sample in distilled water, then wipe with acetone ⇦ on eBay or Amazon [affil link] Warning! Flammable! before you return to polishing. I have no idea why this is so.
Andrew W [returning]- Philadelphia, Pennsylvania, USA
2003
Q. Dear Andrew:
I have made some tests of electropolish on titanium with the bath that you mention. I must say that I feel enormously thankful since I obtained wonderful results. I want to ask some questions in reference to the subject:
* You say that the bath must be to a temperature of 5 deg. What do you mean? 5 deg C or 5 F° degrees?
* Sometimes, the bath produces a noise rather hard. Is this normal? * Sometimes the pieces are well and other times not. When they are well, the color of the piece (when it is retired of the bath) its yellow. When it's bad, the piece present a gray-blue layer. After cleaning't with acetone, the somewhat porous brightness can be seen. It's this a voltage, amps or temp problem ?
And the last question:
* How dangerous it can be to work with this bath? I have heard quite ugly things about the Perchloric Acid and I would not like that my employees can damage their health. What safety measures do you recommend me?
Again, thank you so much for share your experience
Ezequiel R [last name deleted for privacy by Editor]- Capital Federal, Buenos Aires, Argentina
A. Hi, Ezequial. Perchloric acid is horribly dangerous and was responsible for one of the worst chemical disasters in U.S. history. Please see letter 9408. Proprietary recipes for electropolishing titanium are available.
adv.
Please consider Russamer Lab [a finishing.com supporting advertiser] for technology for electropolishing of titanium.
Regards,
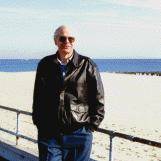
Ted Mooney, P.E.
Striving to live Aloha
(Ted can offer longterm or instant help)
finishing.com - Pine Beach, New Jersey
Q. Dear Andrew
I read through your recipe of polishing titanium alloys. May I know the value of roughness you attained through that process.
Thank you,
AravindPhD student - Chennai, Tamilnadu, INDIA
Q. Dear Andy,
I am searching for titanium fatigue bars for an unrelated project. Please tell me where you obtained the titanium fatigue bars you used. Thank you.
Bill Emery
- Tulsa, Oklahoma
2007
----
Ed. note: Andy's posting was from back in '01. He probably checks the page infrequently if at all, and our contact info for him is dated. Sorry.
Q. I'm a PhD student and I'm working on Titanium alloy (Ti6Al4V) for orthopedic application. our subject is to improve prosthesis life time by coating but with mechanical polishing we don't have a good result so we like to try with electropolishing.
Zhor Nibennaounestudent - France
July 2, 2008
May 15, 2012
Q. I have some titanium parts I want to electro polish. After I electro polish it I want to anodize it.
I read about heating the tanks. What temperatures would work well?
I will be using 6lv4 I think that is the grade.
I have also read about using a combination of perchloric acid, methanol
[affil link], and butanol.
What dangers are these chemicals?
It also talks about agitation. They report a 300 rpm stirring velocity. I think I need more information about this. I was thinking to use a bubble injection method. Inserting an air hose and sending in a low air pressure. This will move the parts and circulate the electrolyte.
I have a 4 minute wait time. at 28 volts. I don't have the number of amps.
Has anyone tried to electro polish with the brush method?
- blacksburg South Carolina usa
Electrochemical Metallizing by Marv Rubinstein
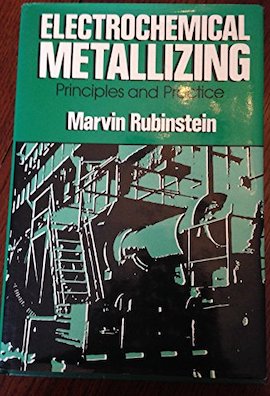
on eBay or Amazon
or AbeBooks
(affil link)
A. Hi Bob. Please don't even consider perchloric acid (see letter 9408), but we appended your inquiry to a thread which may have some answers for you. Brush electropolishing probably is possible. Please try contacting companies who specialize in brush plating.
Regards,
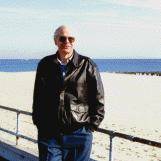
Ted Mooney, P.E.
Striving to live Aloha
(Ted can offer longterm or instant help)
finishing.com - Pine Beach, New Jersey
May 15, 2012
Electropolishing Ti64 with Ti64 cathodes
Q. Is it possible to successfully electro-polish Ti-6Al-4V parts while using cathodes with the same material ?
To make the question more general, can you electro-polish a metal while using cathodes of the same material?
The electrolyte is composed of 10% Vol. perchloric acid (60%) and 90%. vol. acetic acid
⇦ on
eBay
or
Amazon [affil link] (glacial)
Student - Montreal, Quebec, Canada
March 31, 2016
Q, A, or Comment on THIS thread -or- Start a NEW Thread