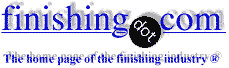
-----
Delayed Plating Blisters on Zinc Castings
2001
We are having problems with delayed plating blisters on barrel plated zinc die castings that are not going to different climates. There are a lot of very small blisters developing all over the parts. This seems to be taking about 1 month to occur. We use nickel over copper with a strike.
Any ideas would be greatly appreciated.
John M. Mahaney- New Oxford, Pennsylvania, USA
I am also interested in this answer. We are having blisters develop on architectural door hardware (zamak plated with satin chrome)after 4-6 months. This is accelerated if the climate is hot or coastal or both. We have been told to install a sacrificial anode of zinc on each door.
Jon Payne- Norcross, Georgia, USA
2001
2001
My first guess would be microporosity of the castings for the first problem.
For the second problem I would increase the Nickel thickness or go to a duplex Nickel to improve corrosion.
I used to work for a company that had been plating zamak #3 knife handles. With .0003" Copper, .0003", Nickel and .000001" Chromium they would last over 20 years with regular use. A strike/plate is essential for good adhesion and sealing of the part (at least 40-50 microinches). A good leveling Acid Copper helps fill in any micropores present and the thick Nickel gives good corrosion protection.
For the Chrome plated door handles you can try microdiscontinuous Chromium if you aren't already using it.
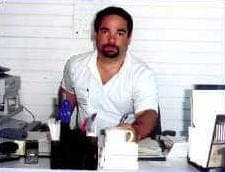
Jim Conner
Mabank, Texas USA
Blisters on cast surfaces occur on many alloys, particularly Zn and Al-based alloys. They are the result of turbulence during the mold filling, causing oxide films to be folded over to make an unbonded double oxide interface. I call this a bifilm.
Hydrogen diffuses slowly into the microscopic air gap between the films and inflates the gap if the bifilm is near the casting surface, pushing the surface away to form a blister.
A change of metal quality and casting conditions is required to avoid bifilms. This is not easy with pressure die cast parts, where the turbulence during the filling operation is not easily controlled. You might try a reduced filling pressure, plus higher casting temperature to make up for the reduced fluidity. A quick test to ascertain whether blisters might be present will be to put a casting into a muffle-type furnace at a temperature just below the mp of the alloy, and boil some water in the furnace to provide a moist atmosphere that will provide hydrogen for the blisters to grow (if there are any).
For a bit of background, you might like to read my books "Castings" 2003 .
and "Castings Practice - the 10 Rules for Casting" 2004, both published by Elsevier. Best of luck!
- Ledbury, UK.
August 17, 2009
Q, A, or Comment on THIS thread -or- Start a NEW Thread