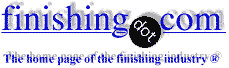
-----
Beer Can Printing Mandrels
I work in the aluminum beverage can industry. We use plastic mandrels for our printing process. Coated steel would have better wear properties. Polished steel hasn't worked at the speeds we run. Any ideas for a coating that will allow the aluminum cans to slide on the mandrels at a tight tolerance at high speeds?
Eric Berkheimer- Fairfield, California, USA
2001
Can you mount Nickel sleeves on mandrel? Stork manufactures sleeves which can be mounted on mandrel.
Kaushik- Charlotte, North Carolina
2001
2001
Let me clear this up. These mandrels are on a high speed printing press and the cans slide onto these 'can' shaped mandrels at high speed for the printing process. They are pulled onto the mandrel by vacuum. At lower speeds we have used polished steel mandrels with good success. With progressive upgrades and increased speeds we find that the aluminum can won't slide onto the steel mandrel fast enough because they seem to hang up.
We switched to plastic which tends to self lubricate but wears out quickly. In trying to get back to a steel core mandrel we have tried ceramic and titanium coating with no real success. We always seem to get to a point where the mandrel surface grabs ahold of the can and they won't load or there is buildup of aluminum oxide.
I was thinking there might be a surface treatment or finish that would have less tension or friction against the inside surface of the aluminum can?
Any suggestions?
Eric Berkheimer- Fairfield, California, USA
This sounds like a scaled-up version of the wire mandrels coated for the medical industry. A parylene coating may be just what you need.
Dick Molincoating systems - Indianapolis, Indiana, USA
2001
First of two simultaneous responses--
I think a good alternative to this would be polished electroless nickel followed by a thin coating of PTFE or Teflon type material. There are a few companies that can provide that coating. The polished EN will provide a lower coefficient of friction and the PTFE will provide lubricity that polished EN will not. If you use PTFE alone it will wear out very quickly.
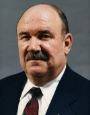
Daryl Spindler, CEF
decorative nickel-chrome plating - Greenbrier, Tennessee
2001
Second of two simultaneous responses--
Eric - Have you exhausted all the possibilities with plastic? Some of the glass filled polyesters have very good wear properties.
Instead of a polished finish on steel would a spark eroded finish help? There would be less contact between the two surfaces reducing the drag as the can came onto the mandrel.
Tim Strickland- Auckland, New Zealand
2001
How about texturing the finish of the mandrel? What performance might you get from dimpling the surface of a metal mandrel as a golf ball is dimpled?
Derek Samueltest engineering - Salt Lake City, Utah, USA
2006
Q, A, or Comment on THIS thread -or- Start a NEW Thread