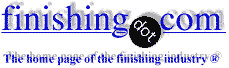
-----
Chemical Polish Problem
2001
Being a production supervisor and not an expert on anodize
I hope some one can help.
We anodize Aluminum at our plant; We etch it and then put it in a chemical polish consisting of (Sulfuric & Phosphoric Acid)before we put it into the anodize tank. We get pitting almost every day from the chemical polish. At one time we added water every day and did not seem to have this problem and now we are told that the parts should be dry before we enter the chemical polish or we will get this pitting. Does anyone have any suggestions as to the best way to chemical polish?
Bryan Burk- Dolgeville, NY USA
I believe you meant to say the formulation was phosphoric / nitric acid. And I think you've gotten some very good advice.
George Brackett III- Utica, New York
2001
The reason when you added water to your bright dip tank and you had no pitting was probably due to the fact that a certain specific gravity of the solution versus the amount of dissolved aluminum is required to avoid pitting and coincidentally you were in that range.
Generally one good way to control a bright dip tank is to adjust the solution parameters based upon the amount of dissolved aluminum. If you are fairly consistent in your surface area being processed then at some point drag out and drag in will equilibrate out the dissolved aluminum content. The bright dip chemistry is complex however. Have your chemist contact your supplier, they should have an understanding of these concepts about control of electropolishing principles as I have outlined them.
As far as the part not being allowed to be wet when processing them through the tank, that is not correct. Usually the parts come out of a rinse following cleaning directly into the bright dip tank. It is bad practice to allow parts to dry during processing once started.
Ward Barcafer, CEFaerospace - Wichita, Kansas
2001
2002
The concentration on bright dip
80% phosphoric acid - nitric acid 3%-42* (Ed. note: baumé scale?)
17% h2o- by volume
aluminum must be kept between 30-40 g/l
specific gravity 1.70-1.73
temp. should be 190 - 210 degrees
these are very important controls. With these controls and a 2.5 to 3.5 minute run you should get a bright finish. if not add more time in seconds. like adding 15 seconds at a time. you will also have to control the specific gravity in your rinse tank. do not let the specific gravity get to the point where your parts don't rinse well. if you get to much drag out your parts can pit if left in rinse to long .
Kris HeimWalkerton, In.
Q, A, or Comment on THIS thread -or- Start a NEW Thread