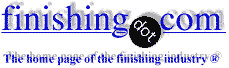
-----
Explain the Process of Chromate Conversion Coating
Can someone explain the details of the process of chromate conversion coating with formulae, time, and temperatures for the conversion?
Ronald Mlejnekj- Hastings, NE
2001
2001
As you may know, plating is applied to a base metal to prevent corrosion. There are two methods that a plating uses to protect a part from corrosion. The first is barrier where the plating just tries to cover the part well to prevent contact with oxygen, water, and salt so that rust can not form. The other method is sacrificial. Sacrificial platings corrode themselves instead of the base metal. The most popular sacrificial plating is zinc and zinc alloys. Nearly all sacrificial platings require a conversion coating. This conversion coating slows down the corrosion of the plating and thereby increases the life of the base metal.
Current conversion coating technology uses a bath of hexavalent chrome (Cr +6). It is typically run at 2% and 80° . The dipping time is around 15 to 30 seconds. These factors vary with different equipment and different chemistries. The numbers I gave you are just ballpark figures.
There are also different versions of conversion coating. They are referred to by color: clear, yellow, bronze, olive drab, black, etc.. Generally, the darker color is a thicker coating and provides better protection. However, black conversion coatings do not perform as well.
Exact conversion coating formulas are valuable proprietary information belonging to plating chemical vendors. Each of them spends much time and money developing these chemicals and it is not in their best interests to give that info out to the public. Many conversion coatings are now being switched from hexavalent chrome to trivalent chrome (Cr +3) due to environmental regulations from the European Union. Trivalent chrome baths on average are much more concentrated and require more heat and dipping time.
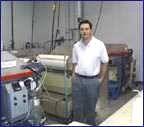
Tim Neveau
Rochester Hills, Michigan
Q, A, or Comment on THIS thread -or- Start a NEW Thread