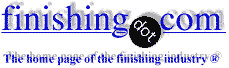
-----
Metal Coating to Cut Cold PVC Insulation
I am looking for a metal coating to reduce the force necessary to cut PVC wire insulation at -20 C. Ideally the coating could be applied in house, on millions of parts and locally (small area .015 sq in), must be compatible with Silicones and tin-lead over nickel platings on a Phosphor-Bronze or similar metal and last 50 cuts. I currently have an edge with .006" max flat on a stamped contact.
Sam D [last name deleted for privacy by Editor]Electronics - Harrisburg, Pennsylvania, USA
2001
Hopefully, for dealing with spot plating/coating on millions of parts, it will prove possible to handle the parts as a continuous strip, and cut the strip after the plating/coating is finished? "Spot plating" machines are available for such purposes, and have elastomer masking belts that move with the part through the plating cell so the plating is applied only to the desired spot.
I applaud you for a well-posted question, Sam, where you explain what you are trying to do quite well, although I didn't quite understand your final sentence. I am picturing some kind of quick-connect where an insulated wire is pushed down into a knife edge contact like one sees in telephone closets, but where you want to make the cut through the PVC ahead of time, rather than being made by the knife edge contact? And for this reason, the coating need not be electrically conductive? Or am I way off?
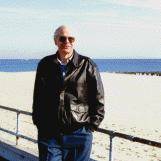
Ted Mooney, P.E.
Striving to live Aloha
(Ted can offer longterm or instant help)
finishing.com - Pine Beach, New Jersey
2001
Sir, you are correct. The parts would be on strip. The last statement refers to the geometry I have now. This "knife" edge (with small flat) contact makes the connection and I am trying to reduce the force necessary to accomplish this at the cold temperatures. The wire and contact are much larger in size than what are used in normal wiring closets.
A non-conductive coating could only be applied to that edge. A compatible conductive coating could be applied all over but that would probably incur a higher cost.
Sam D [last name deleted for privacy by Editor]electronics - Harrisburg, Pennsylvania, USA
2001
I guess I am in a rut. The answer to every question today seems to be 'chrome plating'. Chrome is exceptionally hard, exceptionally wear resistant, exceptionally low friction and non-stick. Premium quality saw blades and circular saw blades are given a flash of chrome plating to minimize 'sticking' of the sides of the blade to the wood they will cut.
Usually, if there is tin-lead over nickel plating on an area that requires further plating, the tin-lead is stripped back first (for example on the gold plated contact tabs of a circuit board).
You might start discussions with a manufacturer of strip plating machines like Technic
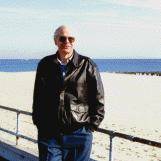
Ted Mooney, P.E.
Striving to live Aloha
(Ted can offer longterm or instant help)
finishing.com - Pine Beach, New Jersey
2001
Q, A, or Comment on THIS thread -or- Start a NEW Thread