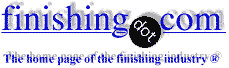
-----
Degreasing ofAluminum Foil
2001
We are manufacturers of Aluminum Foil for blister packing. The aluminium foil is in shape of one meter wide continuous rolls of 12,000 to 15,000 meters.
The degreased aluminium foil is coated with Nitrocellulose primer [lacquer] on one side and a heat-sealable or thermo-reactive vinyl coating on the other side.
We usually buy fully degreased 20 micron hard temper aluminium foil. However, a number of rolling mills offer much lower prices for mill finish aluminium foil which has rolling oils on the surface.
Because of the rolling oils, it is very difficult to apply either the Nitro primer or heat sealable coating which does not adhere to aluminium surface. It therefore necessary to degrease foil in line before it is coated with primer.
We would like some suggestions on the possible methods for degreasing of aluminium foil.
After coating on both sides, the foil is used for packing of confectionery and pharmaceutical products so we have to be careful with the choice of materials which have no possible adverse reservations.
Gul Muhammad Bawa- Karachi, Pakistan
2001
My experience with aluminum rolling is from about 25 years ago, so be forewarned. As I recall, we used a petroleum based rolling lubricant fluid like kerosine, but more refined kerosine, like grade K-1, that is sold for space heater fuel today. We made foil stock at about 0.006" gauge thickness for a foil re-roller, and annealed these in an atmosphere furnace, prior to being shipped out. These wide coils undoubtedly did not allow the rolling lubricant to be completely "burned off" or vaporized clean. I also recall we had to prevent water absorption, and tramp oil build-up in the lube to prevent staining, so that the foil maker could achieve satisfactory surfaces for his customers, or we heard complaints. Uses included making TV dinner trays, etc., where food was in contact. I know they roll foil with two layers together to get it thin enough, which is why all foil has a shiny side against the steel rolls, and a duller side (where the two layers were touching.) After rolling! , the layers are peeled apart and coiled before annealing again, or they will metallurgically bond (stick together).
Obviously your foil supplier is not set up to produce food grade foil, or he would do so, and check each lot for compliance to the FDA standard. I would go shopping for another supplier, not try to clean the foil yourself.
W. Carl Erickson- Rome, New York
Q, A, or Comment on THIS thread -or- Start a NEW Thread