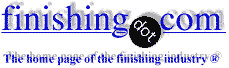
-----
Throwing Power of Cyanide Zinc Plating Solution.
Hi
1) Does voltage affect the throwing power?
2) What composition of the bath improves throwing power?
3) 'Increasing current density improves throwing power' But high current density lowers efficiency of the bath which in turn leads to hydrogen embrittlement at the edges. To worsen the problem the component is crimped at the edge which may lead to plating peel off.
Can the solution composition be maintained in such a way that efficiency remain higher at HCD areas?
Rajesh Kumar- Maraimalainagar, India
2001
2001
Well, a metal ion naturally wants to take the path of least resistance, which means it wants to deposit in the high current density area, rather than "throw" into a low current density area.
1). Higher voltages can do two things to improve throwing power: first they cause hydrogen to evolve (inefficiency) in the HCD areas, leveling things out; second, if the agitation and temperature are low enough, they may be able to help distribution by "starving" the HCD area of metal ions. That is, you use them up so the metal concentration drops in the HCD area while not dropping in the LCD area.
2). We've discussed this one here before and I've claimed that a lower concentration improves throwing power via this "starvation" concept, but I've been contradicted by others whose experience indicates that you can't really starve an HCD area this way. So I'll stick to my claim, but warn you not to infer too much.
The "best" way to get metal to deposit where you want it to is to employ "shields" that lengthen the current path so that the former HCD area is no longer a HCD area. Unfortunately, this is not always practical.
The second best way is to employ effective organic additives that are attracted to the HCD area and tend to block deposition of metal there, thus promoting deposition in areas of lower current density.
Anything else is "third best", and "third best" things are often questionable. It is theoretically possible to affect distribution by adjusting temperature, concentration, voltage, pH, and agitation, but there are usually difficulties about, and you will rarely find a plater who has 'solved his distribution problem' through those kinds of adjustment.
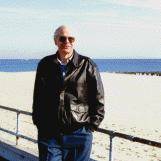
Ted Mooney, P.E.
Striving to live Aloha
(Ted can offer longterm or instant help)
finishing.com - Pine Beach, New Jersey
2001
Dear Mr Rajesh,
A 'normal' 30 gms/lit zinc, 60 NaOH , 90 NaCn, bath will have distribution problems with plating thickness varying 1:3 if your anodes are too close and current in excess of 20 amps/sft.
Try maintaining 15-20 gms / lit of Zinc 45-50 gms / lit of NaCN and
60-75 gms / lit of Na OH. Use a lower current density of 15 to 20 Amps /sq.ft. and use longer plating times which will give you a plating thickness distribution of 1:1.5 from the LCD to HCD range.
This in a way corroborates, Mr Mooney's starvation concept as I have left many platers happier with the lower metal concentration.
All the best,
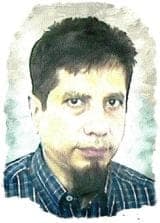
Khozem Vahaanwala
Saify Ind

Bengaluru, Karnataka, India
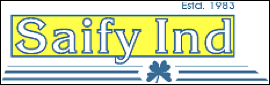
Q, A, or Comment on THIS thread -or- Start a NEW Thread