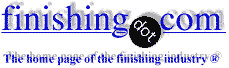
-----
Information on Resurfacing 440C Wear Surfaces
I would be interested in any help or suggestions I could get for the rebuilding of 440C wear surfaces. The wear item is exposed to oil under pressure (100-600psi) where it is being used in it's operating environment. The process that has been tried is heating the material up to 500F and using 409 wire applied with a mig weld while the wear item is held close to that temperature. Then the material temperature is brought back down slowly. Problem that occurred is that the weld build up did not hold to the wear surface. I have asked a few local shops and one suggestion was taking the wear item up to 1500F to "boil" out any oils that may be present in the pores of the material and to wire brush the surface area that is to be welded on to clean it off. Next, proceed to build up the surface with a mig weld on the area that is to be re-machined while the wear item is still hot and then bring the temperature back down slowly. This last process has not been tried and I was wondering if any one else out there has had a success with using a wire weld build up on 440C.
Shannon Stapleton- Sabetha, Kansas USA
2001
2001
Shannon:
The part is made from 440C stainless steel so that is has good wear resistance. The 409 SS did not last because that alloy is not nearly as hard and wear resistant as the original material. Elaborate heat treating processes are not going to change that.
You will need to build up the surface with a hard, wear resistance material. There are many alternatives, the best of which will depend a great deal on the part configuration and specifics of the service application. A thin build up may be accomplished by chromium plating. A hardfacing alloy, possibly a Stellite alloy, may work for a thicker build up. The main thing is to find a material that will have equivalent properties to 440C, then use an application procedure that will not destroy the important properties of the base metal.
Good luck.
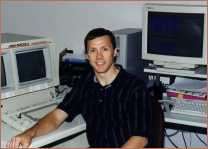
Larry Hanke
Minneapolis, Minnesota
Q, A, or Comment on THIS thread -or- Start a NEW Thread