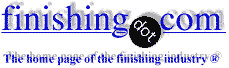
-----
Anodizing for Electrical Resistance / Dielectric
Q. Hi,
I'm working on electronics which are to be placed in an (mainly for aesthetic reasons) anodized aluminum housing consisting of several parts bonded together using threaded mechanical fasteners.
For EMI (electromagnetic interference) and ESD (electrostatic discharge) reasons, the anodized parts should make low impedance contact with each other. Does anyone here have any experience/advice on what/how much is required for this? (note, this is not aimed at protecting against mains electrical shock, so low frequency contact is not so important)
Electrical engineer - Denmark
August 24, 2022
⇩ Related postings, oldest first ⇩
Q. All,
I am a senior mechanical engineer for a government contract defense company. We are considering using a hard anodize finish on two aluminum electronics housings that will be joined together with mechanical fasteners. A requirement is that we need to maintain electrical isolation between the two housings. Is it possible to achieve electrical isolation with a thick hard anodize finish? Anyone have any experience using this coating for electrical isolation?
Thank You
- Nashua, New Hampshire, USA
2000
A. Hard anodize is an excellent electrical resistor. More often than not, this is considered a limitation. A lot of masking on hardcoated parts is to provide for a grounding path. However, due to the edge defect, I would not count on threaded fasteners to provide isolation. (Edge Defect: Hardcoat does not buildup on sharp corners or edges)
Chris Jurey, Past-President IHAALuke Engineering & Mfg. Co. Inc.

Wadsworth, Ohio
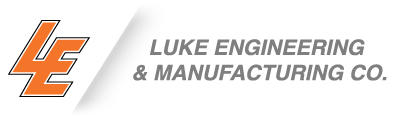
A. Tim,
Hard anodizing is an excellent insulator, my only concern would be the way that you join the 2 housings together. If this involves metal screws, or bolts, most hard coaters will mask these threads, as once they are anodized with a "thick" hardcoat, it is pretty near impossible to get a bolt into the threaded hole. So therefore, you will have continuity between the two housings, unless there is another insulator involved in your fasteners. Material selection of your housings is important also, as some alloys are very difficult to hardcoat...and being a defense contractor, your spec may call for 2024, or another high copper alloy, which, is difficult, but not impossible, to put a "thick" hardcoat on. Some aluminum castings are also very difficult to hardcoat, also. (When I say "thick" I'm referring to a coating that's .002" or more) One more small piece of advice would be to radius all sharp edges as much as possible (I believe 1/16" radius is recommended for a .002 hardcoat), as all sharp edges do not coat well, are very prone to micro-cracking during the anodizing process, and chip very easily after hardcoating, if not carefully handled. And since friction/wear does not appear to be an issue in this case, I would strongly recommend that your hardcoater seal these parts.
Ahh, fellow anodizers ... don't you like it when an engineer actually thinks "finish first"?
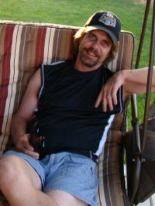
Marc Green
anodizer - Boise, Idaho
If only all engineers started from the finished product and worked backwards
engineering services - England
Q. I have a situation where I need to use high current and high voltage how does a hard anodize stand up to harsh electrical environments.
James McClain- Lakewood, California
2006
A. There is a process called Akadize that has excellent electrical insulating properties plus a harder finish. I work with a company in Pomona that provides this service.
Art Ramirez- San Diego, California
January 6, 2012
----
Ed. note: Thanks Art! But, gentle readers, please try to remember that this site is made possible for you by our supporting advertisers. They're happy to pay for the technical information discussions and the camaraderie it makes possible even when they get no benefit from it. But everyone must draw the line short of paying for their competitor's advertisements
Please try your best to use generic & descriptive names for processes rather than the trademarks and trade names of their competitors. We should now note that Luke Engineering & Mfg. Co., Inc [a finishing.com supporting advertiser]
very specifically offers similar proprietary processes, as well as do several of the other anodizing shops listed in our Shop Directory.
Multiple threads merged: please forgive chronology errors and repetition 🙂
Best aluminum grade for hard anodising for electrical resistance
Q. I am having problems with the anodising of a component we use. The component is a 'top hat' bush which is effectively working as an electrical insulating washer. The purpose of the insulation is to allow the positioning of one component so that it can fit inside another without contact and therefore an electrical continuity method is used.
We specify 6082-T6 and hard anodise to BS 5599 which have had varying results in the past but no fully acceptable results. Through the bush is a M4 s/s caphead tightened to 1.5 Nm which is causing our problems due to the head breaking through the insulation. Washers, both in stainless and copper have been tried with some degree of success. Stainless is sometimes too hard and breaking the anodic layer and copper is too soft and 'creeping' due to the softness of the material.
Can anyone recommend a more suitable grade of Al alloy? I have spoken to people who 'think' certain grades are better than others but no-one convinces me.
Pharmaceutical/packaging machinery - Coventry, UK
2007
A. I don't know if a 'better' grade would solve the problem ... but if the problem is the hardness of the aluminium, then using 6082 in a harder temper (H24 for example), would increase the hardness by perhaps 10 to 15%, but would probably not give better results.
The 7000 series, (7075 for example) would increase hardness by maybe 50%, but the same might apply.
Could you spread the torque force by increasing the area of the washer, or reduce the torque, or use harder aluminium alloy washers?
Best of luck anyway.
Ship Repair - Plymouth, UK
A. Dale
The insulating layer on anodised aluminium is aluminium oxide. This is very hard but also brittle. Although you can control the torque of the capscrews, it is unlikely that their bearing surface is finished to a particular standard and there may well be areas where the contact pressure is very high and the underlying aluminium substrate will distort to accommodate this -- thus cracking the anodised layer.
Even if you can get a "better grade" of alloy, the underlying problem remains. Remember that even if you succeed, the first maintenance man to work on the machine may never have heard of torque -- the safety factor will be small.
I would suggest that you need an insulating washer. Thin PTFE should be acceptable in a pharmaceutical application.
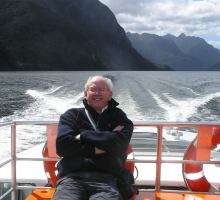
Geoff Smith
Hampshire, England
Thanks for the replies. To give you some more information, the cap heads are selected so that the surface contains no burrs or pips even to the point where the technicians building the machine use a file to take sharp edges away. Should the machine need to be dismantled, the anodised bush will be replaced with another 'fresh' one and the same technicians are used each time so they know the job well.
After visiting the anodiser responsible for the coating, it was thought that the coating wasn't thick enough so a trial batch are being coated with around 50 microns thickness and some are also having PTFE applied. I just thought there may be a better grade available for an application like this as I'm sure some people will have experienced similar problems.
Pharmaceutical/packaging machinery - Coventry, UK
2007
A. Dale,
I can suggest Keronite as a solution, a 40µm Keronite layer with an air dry PTFE overspray should give you a positive lasting fix.
Best regards
- Granta Park ,Cambridge, UK
----
Ed. note: Thanks Rod! But once again, gentle readers, we ask that you please try your best in this free forum for camaraderie & technical information exchange, which has been made possible for you by our supporting advertisers, to use generic & descriptive names for processes -- like "spark anodizing", "microarc oxidation" or "plasma electrolytic oxidation" rather than the trademarks or trade names of the competitors of our supporting advertisers :-)
"Minimum anodising thickness for electrical insulation?"
Q. Hi,
I have recently received a drawing that specifies anodising to 25 µm thickness for electrical insulation.
We anodise using a sulfuric acid electrolyte, but I was wondering whether electrical insulation would be achieved with a thinner anodic layer.
Regards,
Production Engineer - Gloucester, UK
2007
Treatment &
Finishing of
Aluminium and
Its Alloys"
by Wernick, Pinner
& Sheasby
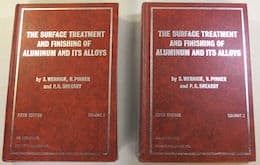
on eBay or Amazon
or AbeBooks
(affil link)
A. Voltage?
Aluminum alloy (high Cu or Si levels reduce the insulating value of the anodize)?
Hard anodize or conventional?
Dissolved aluminum in the electrolyte (high levels increase sulphate incorporation into the anodize)?
Flat surface or wire? If wire, what diameter (smaller diameters cause more anodize cracks, so less insulating)?
Environment (low humidity, non-condensing, wet)?
Section 10 of Chapter 12 of "The Surface Treatment and Finishing of Aluminum and Its Alloys" ⇨
6th Edn., covers electrical properties of anodic films. Earlier editions have similar information.
Tests for breakdown voltage are given in EN 12373-17, BS 6161: part 15: 1987 and ISO 2376.
Ken Vlach [deceased]- Goleta, California

Rest in peace, Ken. Thank you for your hard work which the finishing world, and we at finishing.com, continue to benefit from.
Anodized aluminum mounts for solar collectors
Q. I am developing a mounting foot for mounting solar panels to residential rooftops. If I anodize the mounting feet and insulate the hardware from the anodized aluminum frames, do I need to mechanically ground the panels or mounting feet? If not, should there be any concern for static electricity?
Kevin StapletonSolar energy - San Antonio, Texas, United States
March 25, 2012
A. Hi Kevin. Unfortunately I am not familiar enough with the technology to understand the potential issue you are concerned about. Are you suggesting the possibility that a static charge could build up between the mounting feet and the frame which could damage the solar panel, or shock an installer? I can't picture that happening.
Regards,
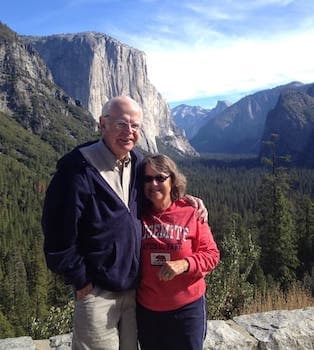
Ted Mooney, P.E. RET
Striving to live Aloha
(Ted can offer longterm or instant help)
finishing.com - Pine Beach, New Jersey
Electrical resistivity of hard anodizing per AMS2469
Q. I'm Kevin Cancino and I have a customer that has asked about the electrical resistivity of hardcoat anodize. Does the AMS2469 Spec. have required test criteria? How is this measured and by what acceptable means? Thanks
Kevin Cancinoplating shop employee - Dayton, Ohio
May 14, 2014
A. Hi, Kevin,
It is virtually impossible to get any meaningful measurement of electrical resistivity. An allied property, impedance, is measured. The impedance is used as a means of testing the quality of sealing: the higher the impedance the lower the porosity of the anodic film. Sealing quality is usually the preserve of decorative anodizers interested in corrosion resistance.
Just to make life difficult, the result of the measurement is usually expressed as admittance rather than impedance. Admittance is the inverse of impedance.
The testing procedure is well documented in anodizing test methods.
The question you really ought to ask is why your customer wants to know. It might be possible then to offer some more specific guidance. I wonder, for example, if the interest is really electrical breakdown voltage. Maybe too, that is a hundred miles from what is wanted!
Harry
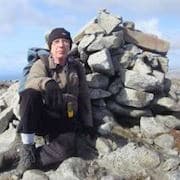
Harry Parkes
- Birmingham, UK
Q. Any thoughts as to best electrolyte chemistries to produce high dielectric breakdown voltages >640 V/mil and high corrosion resistance to 5% HCl bubble test? Have tried Sulfuric 15%-18% with Glycolic Acid and Sulfuric 15% with 3% Oxalic Acid with great corrosion resistance results ... however. the dielectric breakdown voltages suffer.
daniel schick- Redwood City, California, USA
November 24, 2014
Q. Dear All;
I am Irem from Turkey. I am a new worker on Special processes of defense industry. I have to learn electrical breakdown measurement of Chromic acid anodizing of Aluminum acc. to BS6161-15. How can I do this test? Our customer wants to do this test. In addition I haven't any knowledge about this test.
I need your help.
Thanks everybody
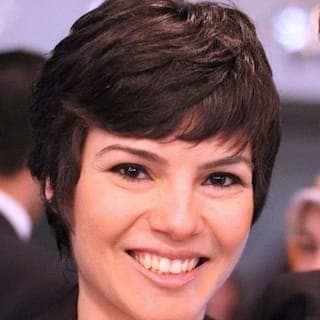
Irem Tuncel Boğaz
Chemical Coating Engineer - Izmir, Turkey
October 30, 2015
A. Hi Irem,
The answer lies in your question: buy a copy of the standard. Surely it must be a requirement of a defense contractor to keep up to date copies of the standards to which they are working?
A quick Google search said that the standard has now been superseded by BS EN ISO 2376. I doubt if the content of the standard has changed but is more to do with bringing old British Standards into line with modern ISO formats.
I was much involved with BS 1615 in the 1960s. It included the method of measuring voltage breakdown which eventually became this standard. It was intended as a method of determining anodic film thickness. For this purpose it was killed off by eddy current machines.
Best wishes,
Harry
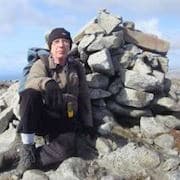
Harry Parkes
- Birmingham, UK
Q. Is hard coating with Teflon good to get isolation of 4kV (Electrical breakdown voltage) in ISO Safety testing?
Dan
- Migdal HaEmek, Israel
October 29, 2015
Continuity Testing for Chromic Acid Anodizing
Q. Is any continuity test applicable for chromic acid anodizing process? If applicable then what standard should be followed?
Nabin Pal- madhyamgram, west bengal, India
August 10, 2018
A. Hi Nabin. We appended your inquiry to a thread where Harry Parkes has discussed the issue. Please see his posting, then ask for any necessary clarification. Thanks!
Regards,
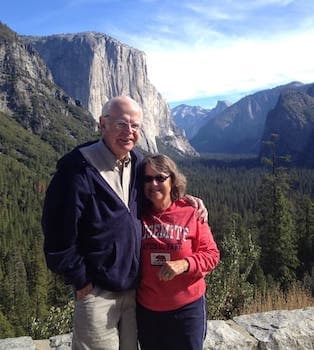
Ted Mooney, P.E. RET
Striving to live Aloha
(Ted can offer longterm or instant help)
finishing.com - Pine Beach, New Jersey
Q. We do conductivity test for anodized part to check, is part got anodized or not?
Looking for how much volt and current to be applied to do conductivity test?
Bz, Anodised layer may break if apply more volt and current.
- Bangalore, India
September 10, 2018
A. An ohmmeter can be used to check for continuity.
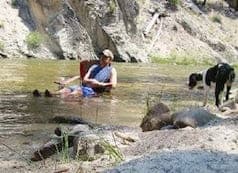
Marc Green
anodizer - Boise, Idaho
A. If you wonder anodized profile's quality as conductivity you should implement "admittance test". One of the important characteristics of anodized surfaces is "dielectric", but this issue depends on quality of anodized surface (especially sealing quality is most important). So if you measure sealing quality, according to Qualanod book you should make "admittance test". If you read this chapter in Qualanod book you will understand your question; but also if you make this test you must buy "anotest machine". Also this test is not applicable for cold sealed profiles and coloured profiles (medium bronze, dark bronze and black).
Alaattin tuna- sakarya,TURKEY
Q, A, or Comment on THIS thread -or- Start a NEW Thread