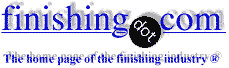
-----
Tin Plating Issues
I'm looking for any suggestions that you might have to solve a couple of plating related problems. I'm a purchasing agent, and one of my suppliers is having some problems with a tin plated component that they sell to us on a production basis. The component consists of a 3/8" copper tube that is bent into a serpentine shape, to which
1/16" thick copper strips are attached. After assembly, the component is washed in an alkaline soap, etched in a bath of acid, rinsed in water, and then dipped into a vat of molten tin. It is then withdrawn from the tin vat, passed through a curtain of air to remove excess tin, and then dipped into a water tank for cooling. The result is a tin plated component that normally exhibits smooth, bright plating on the copper strips and copper serpentine.
Lately, however, the plating has shown signs of de-wetting, in which the plating is dull, yellowish, and contains lumps and runs. A textbook that we consulted said that the probable cause is failure to fully clean the copper before the plating process. We experimented by increasing the time that the component is immersed in the alkaline solution, as well as by increasing the temperature of the alkaline bath, but have not had good results. This component has been in production for over ten years. The de-wetting problem comes and goes of its own accord, and has happened many times before. We would, though, like to find the root cause of the problem in order to keep it from happening again. Does anyone have suggestions?
Another issue that we are dealing with on this same component is this: we get drips of tin on the ends of the copper serpentine when we pull it out of the tin vat. The drips don't come off in the air curtain, so we reheat the drips with an oxy-acetylene torch after the tin has cooled, and the drips are shaken-off by hand. The issue is that the heat of the torch tends to anneal the copper tube, which causes problems further down the line in the manufacturing process. Does anyone know of a way to remove the drips of tin, either in the molten or solid state without applying additional heat? Thanks for any help that you can provide.
- Vernon Hills, Illinois USA
2000
Cleaning the parts is very important, as is the acid flux, and the purity of the tin bath. I would suggest a written procedure of how the parts are processed now. Time, temperature, concentration, drawings of the baskets, trays, conveyors, air knives (air pressures, type of nozzles, filtration of air). How often do you replace the tin bath? How often do you replace the other solutions. Can you quantify the rinsing process? Do you chart impurities in the tin bath? How do you make sure that the copper tubes are tumbled enough to drain each previous solution? The drips of tin can be controlled by the way the parts are removed and tumbled and blown clean by the air knife.


Tom Pullizzi
Falls Township, Pennsylvania
2000
I think Mr. Pullizzi has nailed it. My gut reaction is either a Sn bath purity problem (like excessive Cu) or a change in the nature of the copper (assuming that the preclean has indeed remained constant).
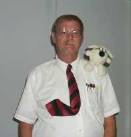
James Totter, CEF
- Tallahassee, Florida
2000
Tin bath replacement and utilization are very costly procedures. Speed of tin plating can be increased by placing in additional tin salts and thiourea
⇦ on
eBay
or
Amazon [affil link] . However after several corrections, complex of the accumulated ions of Cu +2 and Zn +2 will eventually cause full loss of the efficiency of the tinning bath.
Our group has developed regeneration procedure which require electrochemical process, and will not generate any waste.
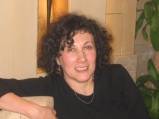
Anna Berkovich
Russamer Lab

Pittsburgh, Pennsylvania
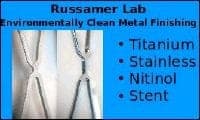
2001
Q, A, or Comment on THIS thread -or- Start a NEW Thread