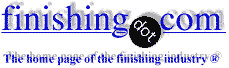
-----
Help for Nickel electroplating problems
We manufacture seamless pressure vessels. We are currently produce a 24" diameter X 7' long cylinder that is coated on the Inside diameter with Nickel 200. We contract out the plating. We are currently having problems with small "pin-holes" throughout the plating. The cylinders are polished to a mirror finish, so any small defect is magnified. The cylinders are electroplated in a sulfamate bath. We have been working with our plater to solve this problem but to no avail. I have digital pictures available, upon request, that show the problem. The base cylinder is made from BOF melted, strand cast rounds. Pierced and hot rolled to make seamless pipe. Steel grade is AISI 4130 alloy. The cylinders are heat treated by liquid quench and temper before plating.
Mike Geissler- McKeesport, Pennsylvania USA
2000
Mike-
Your plater must have the chemistry of the bath in perfect shape to avoid the pits and the flow of solution must be consistent. It must be analyzed for nickel, boric acid, pH and surface tension/wetter concentration. If all these are in range and the pits continue, it is possible that the breakdown products have caused high ammonium in the bath. For further information on how ammonium in sulfamate baths causes pits, contact Anthony D'Amato at Zero Discharge Technologies in Chicopee, MA. He gave a paper on this problem last year at the AESF sponsored Aerospace Conference.
airline - San Francisco, California
2000
Without seeing the part and preferably the process, it is a guess. My guess is gas bubble pitting. Better agitation should eliminate the problem. An air sparger made out of tubing with holes in it and place quite close to the metal surface at the bottom would be my choice. Pumped solution pointed at an angle to the part so that you get a spiral motion (several nozzles)would work if the pump was strong enough. Impeller agitation works, but frequently there is a problem with interference with the anode.
James Watts- Navarre, Florida
2000
On top of what all the other good ideas that you received here, I would check the filtration. It is possible that tiny little parts in the solution cause the pits.
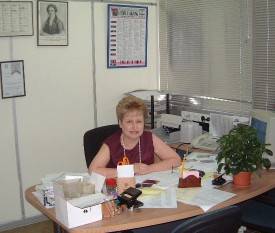

Sara Michaeli
Tel-Aviv-Yafo, Israel
2000
Mike
All above ideas are very good ones, Years ago the shop I was working at would plate ID of cylinders something like you are talking about. The cylinders were honed and polish tiny slivers would smear into the surface, during the cleaning cycle (reverse current) would pull the slivers and after plating would have pits. At that time we found that honers were trying to "hog" to much when close to finish size
plater - Charlotte, North Carolina
2001
Q, A, or Comment on THIS thread -or- Start a NEW Thread