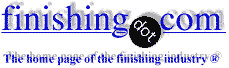
-----
Nickel electroless plating adhesion problems
2000
Nextrom SA is a Swiss extruder producer. For some production of plastic tubes in PVDF, we need a corrosion protective layer against HF acids to put on the pieces in contact with the melted polymer. Now we are coating all our extrusion heads (distributor, die, inner guide, connecting flange) with a nickel electroless plating layer. It's a NiP 0,02mm thick layer, with 8-10% P in weight, hardened at 400 °C during one hour. This layer covered an hot working steel (1,2343, X38CrMoV51, Z38CDV5), which is hardened at 54HRC (580HV). OUR PROBLEMS ARE THE FOLLOWING :
The NiP is peeled off after some moth of production. in some case we had also blisters after some hour. We suspect that the first problem could be due to the low abrasion resistance of the NiP layer maybe connected with corrosion on the steel interface. The second is more an problem of poor adhesion of the layer on the steel (cleaning, activating and or deposition problems).
Remarks : this kind of extrusion head are working at around 250 °C and under a polymer pressure of 400bars.
QUESTIONS :
Which are the real causes of this problems ?
Are there solution to avoid this problems ?
Is the 20 microns thickness enough to avoid any corrosion problems on the steel (through eventually layer defects, porosity, or microcracks) ?
Is the hardening treatment (400 C/hour) the best solution against corrosion and adhesion lacks ?
Is NiP electroless hardened layer the best solution for this kind of use (If not, which one could be better) ?
We had some ductility loose due to the hydrogen adsorption on our high resistant steel, is it affecting the adhesion ?
- Lausanne, Vaud, Switzerland
2000
Which are the real causes of this problems ?
Are there solution to avoid this problems ?
- I don't know, but can you try plating some test molds with electrolytic nickel or nickel-cobalt, as a test?
Is the 20 microns thickness enough to avoid any corrosion problems on the steel (through eventually layer defects, porosity, or microcracks) ?
- You suspect the failure after some months to be related to corrosion; is there physical evidence of this?
- A common technique to seal porosity (in the 1950's!) was to plate a layer of metal, polish it, plate another layer (different metal, sometimes), polish it. etc. It may be practical for an expensive component like a PVC mold.
Is the hardening treatment (400 C/hour) the best solution against corrosion and adhesion lacks ?
- I did not know that heat treatment provided corrosion protection, and sometimes heat treatment does not improve adhesion.
Is NiP electroless hardened layer the best solution for this kind of use (If not, which one could be better) ? electrolytic nickel or nickel cobalt, with hard chrome over it?
We had some ductility loose due to the hydrogen adsorption on our high resistant steel, is it affecting the adhesion ?
- I could imagine that if you are losing ductility of your high strength steel due to H absorption, it may be affecting the Electroless nickel - steel interface.
Does the E'less nickel form a barrier to H? Would another metal be less of a barrier? Would it be useful to bake the molds to remove H once in a while?


Tom Pullizzi
Falls Township, Pennsylvania
THE ORIGIN OF THE PEELING MUST BE:
1.IMPROPER ADHESION OF THE E-N PLATE. WHICH CAN BE SOLVED BY FOLLOWING STRICT PREPARATORY STEPS. (FOR THIS KIND OF STEELS THOROUGH CLEANING AND WOODS ACTIVATION LONG ENOUGH TO COVER THE ENTIRE SURFACE ARE A MUST).
2.LACK OF CORROSION RESISTANCE OF THE LAYER. ON THE LATER, I IT IS WELL KNOWN THAT HEAT TREATMENT NOT ONLY WILL NOT BENEFIT BUT WILL GREATLY REDUCE THE PROPERTIES OF YOUR E-N(IN SOME CASES UP TO 100 TIMES!).
3.LACK OF INTEGRITY DUE TO POROSITY OR MICROCRACKS. SOME BATH COMPOSITIONS PRODUCE EXCESSIVE POROSITY IN THE PLATE WITH THICKNESS OVER 0.01MM, ALLOWING THE CORROSIVE HF GASES TO REACH THE SUBSTRATE.
Monterrey, NL, Mexico
2001
As Mr. Marrufo said, heat treating a high P EN coating not only doesn't increase corrosion resistance but on the contrary reduces it. Why don't you try using it as it is. The coating is amorphous and has a very good corrosion resistance. Heat treatment is used for increasing the hardness and you get a crystal structure.
Christos Sigalas- Athens, Greece
2001
Q, A, or Comment on THIS thread -or- Start a NEW Thread