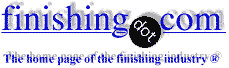
-----
Why phosphate? Which kind to use?
What is the importance of Phosphating (Pre-treatment) before Painting process. Which Phosphating is having best corrosion resistance.
Sameer Saxena- Jamshedpur, India
2000
Phosphatizing does several things: it improves the paint bond, it serves as a protective coating should the paint chip or scratch, and it neutralizes anodic "hot spots" on the surface of the part--minimizing corrosion.
Zinc phosphating is more expensive than iron phosphating and more corrosion resistant.
However, an iron phosphate with a good chemical final rinse
(chromic-acid based or a more environmentally accepted alternative) is perfectly acceptable for most situations.
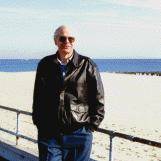
Ted Mooney, P.E.
Striving to live Aloha
(Ted can offer longterm or instant help)
finishing.com - Pine Beach, New Jersey
2000
Phosphating provides an inert crystalline base over which to paint. This coating is never very thick or very complete, but is the most efficient way of preparing metal for subsequent painting in a high volume situation. The coating used as a paint base is not suitable for storage or use without a topcoat, mainly because of its porosity.
Zinc Phosphating is the best pretreatment for high-end applications such as automotive and appliance, provided a good process is set up including the correct final rinse materials for the topcoat.
Iron phosphating is by far the most common, representing a further compromise based on cost and environmental impacts. Iron phosphate systems can be made to perform very well, almost equaling Zinc phosphate systems, but the process must be tightly controlled and the best pretreatment materials and methods must be used.
Other phosphate systems exist but these two are the most common for paint base applications in high volume situations. For aluminum, Chrome phosphating has been replaced in recent years by safer, less environmentally damaging treatments that give almost the same results.
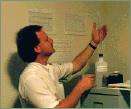
Jeff Watson
- Pearland, Texas
2000
Q, A, or Comment on THIS thread -or- Start a NEW Thread