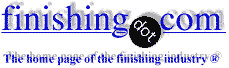
-----
A Nickel Bath Puzzle
2000
One of my clients has a problem with his new bright nickel tank. Everything was mixed the same way it was at the old location, except that the tank size had increased, which was calculated in prior to mixing the bath. HOWEVER- this bath, cfc-free bright nickel sulphate in a five lane poly tank @ 100 amp per lane installed rectifier capacity is used to plate small parts racked in a cross rack ( + ) about 20 deep and five to six per lane for a 15 minute duty cycle, performed well in the other shop ( being shut down )but here it will not start up for us. Throwing power is uneven with burn, roughness or pitting, or under plated at random locations. Analytical came back within or close to operating parameters. Nothing that should impact the process this muchBrightener, carrier and leveller additions seem to have some effect but not a solution (hehe)
As this tank's operation is essential to the line we need to find the cause and get this resolved. The vendor is dragging feet which is not a good thing at all. (The landlord and the new tenants for the old location agree!)
All that we find different is the tank size. Anyone have a similar experience? We would appreciate any solutions you have or
Julie C. Rogers- Tempe Arizona USA
Check the rack agitation, solution agitation, air agitation, and temperature profile of the bath. About all I can think of is that there's something radically different at the boundary layer; it is not exchanging solution fast enough.
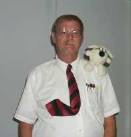
James Totter, CEF
- Tallahassee, Florida
2000
Julie,
I would like to recommend to do a Hull Cell ⇦ huh? on the bath if you haven't do this yet if the hull cell comes out good then the solution is probably good. This would possible omit the solution for sure. The next area that I would look at is rectifier(s) or at least in that area, are your contacts on tank heating up, any possible loose or shorted contacts, rectifiers correct for the type of plating.
Chris Snyderplater - Charlotte, North Carolina
2000
2000
If the tank is new, the lining was not leached prior to use, or leached incorrectly, and the organics leaching into the bath can cause all the problems which you describe. Leach the tank, and carbon treat the nickel solution.
(You should see some of the same problems if you plate a Hull Cell panel 1 or 2 amps, for 5 minutes)
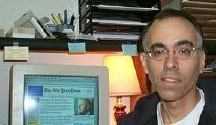

Tom Pullizzi
Falls Township, Pennsylvania
If the chemicals are within the correct parameters, obviously the area to look at is mechanical. Firstly, you say nothing about agitation. If this is a sulphate (watts) type nickel, generally some type of agitation (preferably air) is used. Poor agitation will lower the allowable current density before "burning" occurs and will cause poor distribution and other maladies. The pitting may be from particulates formed by particles coming from the "burn"
Also look at the placement and connection of anode baskets. Are they full, do they make good contact, have they been bagged?
Not to second guess your supplier, but were test panels (Hull or Jiggle Cell) ran or just analysis? What parameters were these tests done at (if at all)? Try changing some of these parameters to see if you can simulate the problem you are having.
Gene Packmanprocess supplier - Great Neck, New York
2000
Had a similar problem recently on a bright nickel, Analysis correct, Hull Cell perfect.
Found the rectifier was a phase down. Cured immediately
Tom Kinsman- UK
2000
2000
A lot of good advice. Here's what I would do:
1) Analyze the solution. Particularly, make sure the nickel sulphate level is high enough. Check and adjust the pH.
2) Run Hull cell test and adjust brighteners.
3) Using a multimeter, check for ripple (AC volts divided by DC volts x 100. A good rectifier should be less than 1%. If it's around 33%, you've lost a phase and the rectifier needs repairing.
4) Use a DC amprobe on the tank while it's loaded with racks. The amperage from rack to rack must be fairly close to stay in the bright range.
5) Try to keep a reasonable distance between the anodes and the work. The farther away, the less the effects of current density.
6) Lastly, and very importantly, make sure yoy agitation is adequate, throughout the vat. Inadequate agitation can result in high current density burning and low current density dullness.
Hope this helps.
George Brackett III- Utica, NY USA
Q, A, or Comment on THIS thread -or- Start a NEW Thread