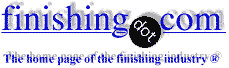
-----
Pin hole leaks in stainless steel ozone tanks
Q. Hello,
I work for a municipal authority producing drinking water. Over the last six years we have built and brought on line seven treatment plants all of which use ozone as the first treatment process. The ozone is bubbled in to the water flowing counter current. Fine bubble diffusers are used and this process takes place in stainless steel tanks (10 ' diameter and 20 ' high. We have a total of 33 tanks that have been in service up to 5 years. In the last year we have noticed pin hole leaks in the tanks at one plant. There were a couple a year ago and now there are 40 . All of these appear to be at places where welding has been done.
William W. HutchisonAltoona City Authority - Altoona, Penna., USA
2000
![]() ![]() |
A. Just as you would get galvanic currents when two dissimilar metals are in a conductive solution and have a metallic path connecting them, you get similar (though smaller) galvanic currents between the stressed 'hot spots' on a surface and the rest of that surface. And you also get galvanic currents between highly oxygenated areas and less oxygenated areas. I don't know the exact solution to your problem, but I am confident that the pinholes are galvanic corrosion. Perhaps bead blasting after the welding will limit this galvanic differential. Naturally, the degree of ozone aeration at different spots is also a factor that you may possibly be able to address. Although I can't come up with the term at the moment, there is a name for the phenomenon whereby corrosion occurs underneath bolt heads due to oxygen deprivation compared to the surfaces that are not under the bolt heads. ![]() Ted Mooney, P.E. Striving to live Aloha (Ted can offer longterm or instant help) finishing.com - Pine Beach, New Jersey 2000 A. William, One option you can look at would be to Brush Electroplate the seam areas to fill in the porosity. This process can be done at the facility on an as needed basis using Nickel, Copper or other metals for the repair, of course this would depend on the definition of pin hole. For bigger pin holes the tanks may be able to be welded, then cleaned with a weldment cleaner. David Crocker- Valencia, California 2000 A. You have a major problem developing from your description. Was the welding certified by the mfg. of the tanks? Were the welds passivated? I think you will have to have the welds ground down, the correct filler applied, and all weld areas repassivated in situ. Dan Weaver- Toccoa, Georgia 2000 A. There are two possible failure mechanisms for the leaks in your tanks. One is pitting corrosion. The second is stress corrosion cracking. Pitting corrosion is a problem since the leaks will gradually get worse until the damage is repaired or the tank is replaced. If the leaks are due to pitting corrosion, you may be able to repair and rehabilitate these tanks if the damage is not too severe. The location of the leaks along the weld is not surprising. Corrosion resistance is diminished by welding, especially if the weld areas are not cleaned properly after welding. If the leaks are due to stress corrosion cracking (SCC), there is a risk of catastrophic failure of these tanks. The cracks will grow with time, and may cause a dangerous collapse of the tank without having severe leaks. SCC would also occur preferentially at the weld heat affected zone. I strongly recommend that you have these tanks inspected soon by someone familiar with nondestructive testing and corrosion. This recommendation is made for safety sake in case the damage is SCC and to give you the best chance to make repairs without losing these tanks altogether. Good luck. ![]() Larry Hanke Minneapolis, Minnesota 2000 A. A very big problem in welding Austenitic Stainless is sensitization. Stainless is corrosion resistant because of the thin film of chromium oxide formed on the surface. When welded, the chromium in the heat affected zone (800-1400 F) forms chromium carbide. This ties up the chromium allowing corrosion. Heat treat after the weld will prevent this. Randy Dastrup- Logan, Utah, USA 2000 |
A. Dear Sir,
We dealt with a customer who was an engineer for company who makes Aquafina Drinking water which is also a ozone process. They were having the same problems as you because ozone will eat stainless at a rate approximately .01/year.
They knew that this was going to be a problem, but it was cheaper for them to replace these tanks every so often rather than constructing the tanks out of a material that could withstand the ozone. Other materials might include titanium and other such materials which are extremely costly.
If we can pass any other information along to you, please let us know.
Thank you,
Hunter Cutchin- Easley, South Carolina
2000
A. My corporation has been manufacturing stainless steel ozone contact tanks for the past 20 years. Sizes range from 9 5/8 dia. to 65 in dia. To date we have several thousand tanks in service. The failure rate is less than 1%. Your problem is descriptive of what we have seen. In most cases the problem can be traced to an electrical differential in the system. (Causes range from a bad electrical ground to, in rare cases, an electrical potential generated from impurities in the water when it is set in motion.) As far as repairs go, the pinholes will blow out if re-welding is attempted as the stainless in that area has been altered in composition and is high in impurities. In fabrication, welding procedure is very important. If the heat, speed and shield gas are not within correct parameters the metal may not recombine correctly and the area roughly an inch away from the weld will exhibit cracking or pitting in time. The presence of Chlorine will accelerate this problem. Interestingly enough there are a few places in the United States where the water rapidly eats through 304 stainless steel. One solar contractor in Calif. had a tank go out in two weeks! We sent him another. It lasted 2 weeks! In changing to T 316L the problem was solved.
Lou BaribaultMfg. Stainless steel tanks - Sandpoint, Idaho
2004
A? Hi all! What about using 316L pipes with longitudinal TIG welding for the ozone transfer pipes?
Johnny Rovk- Italy
October 14, 2016
Q, A, or Comment on THIS thread -or- Start a NEW Thread