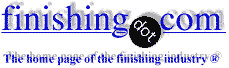
-----
Price difference between hexchrome & trichrome coatings
Q. Can anyone estimate the material cost difference between hexchrome and trichrome coatings? I work in the materials department for a company who is trying to convert over to trichromes because our customers are telling us that they would like to eliminate all hexavalent chrome by 2003. (Ahhh!) I was just curious because this directive is costing us a lot of money in engineering time, let alone material costs. Thank you for helping me to better understand.-Julie
Ken Swartz- Warren, Michigan, USA
2001
A. Actually, tri chrome is slightly less expensive than hex chrome, although the difference is lost in round-off error in most shops. So, if you don't have rigorous salt spray requirements, your problem is easy to solve--just change the spec and forget it.
The problem comes when you want to change to tri chrome without sacrificing salt spray resistance. Tri chrome is markedly inferior in corrosion resistance. So, what you really need to do is replace the tri-chrome with some kind of more exotic conversion coating which inherently costs more, which usually will involve extra steps and more labor, and will probably have a higher reject rate (also driving up costs).
In my experience there are no 'standard cost tables' that can help you; rather, all you can do is to get your plating shops to quote you. And all that most of them can do is take a stab at it, offer short term pricing, and see what they learn as they move towards real production.
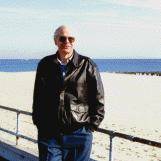
Ted Mooney, P.E.
Striving to live Aloha
(Ted can offer longterm or instant help)
finishing.com - Pine Beach, New Jersey
2001
A. Hi! I work in Auburn Hills, but live in Warren. I am an engineer doing the same thing as you are. The simple answer is no. The chemistry is different and is new, so nobody has developed cost figures yet. People can give quotes if they really have to, but there is going to be some big assumptions and guesswork involved. Happy hunting!
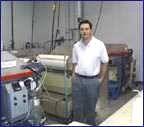
Tim Neveau
Rochester Hills, Michigan
2001
A. The cost differentials depend on a number of factors. "Standard" blue bright trivalent chromates are about 10 to 20% less expensive than hexavalent products of similar (low) salt spray. Much of this difference in cost revolves around longer bath life, lower disposal and treatment costs.
The extended corrosion protection type products being introduced as replacements for hexavalent yellow or black finishes are a good deal more expensive to make up and operate. Make up costs can be five to twenty five times higher since not only are they more expensive, they generally operate at five to twenty times the concentrations of products in the first group. Operating costs are also higher, not only based on the use of more expensive materials but higher drag out since the solutions are more concentrated. Much of this can be negated by better reclaim of dragged out material and reduction is waste treatment and disposal costs. Therefore, I believe that overall operating costs may increase 10 and make up costs as indicated.
I hope this gives you some ideas without getting into proprietary information. Gene
Gene Packmanprocess supplier - Great Neck, New York
2001
Q. Ted Mooney's response that "Tri chrome is markedly inferior in corrosion resistance" to Hex chrome is interesting. With a 5% salt spray test of zinc-chromate(Cr+3), with 8 microns (.0005")of zinc plated thickness, what would one expect in hours to white and red corrosion?
David Sebastian- LaGrange, Illinois,USA
2001
A. According to the MFSA's "Quality Metal Finishing Guide", 8 microns is used for "moderate" service [mostly to dry indoor atmospheres but subjected to occasional condensation, wear or abrasion] for example "tools, zipper pulls, shelves, machine parts".
The booklet requotes ASTM B201-80 that one-dip colorless (clear bright) coatings should last 12 hours to white rust, two-dip colorless should last 24 hours, and iridescent yellow or bronze should last 96 hours. Trivalent coatings are clear bright, hexavalent are iridescent yellow or bronze.
I don't know if any specs give hours to red rust, but if they don't that would make sense to me considering that zinc is a sacrificial metal.
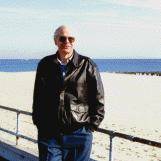
Ted Mooney, P.E.
Striving to live Aloha
(Ted can offer longterm or instant help)
finishing.com - Pine Beach, New Jersey
2001
Ed. note: Please note the date on this communication. Trivalent coatings have made great strides and now exhibit the same corrosion resistance as hexavalent.
A We are currently trialing some of the new chromium chloride based passivates becoming available in Europe, to replace yellow/colour passivates containing hexavalent chrome, as I think some of you may be aware about the EU End of Life directive concerning amount of Hexavalent chrome on components in the automotive industry. We've tried a couple so far but only on the lab scale, They operate at around 10% v/v conc @ 70 °C with a pH range of 1.8 to 2.2.
They give a slight iridescent to pale green colour depending upon how the light catches them when you examine them (they don't look like either standard clear trivalent passivates or full colour passivates but something in between, should be interesting re-educating customer inspection departments), you can also bake them after processing (so they say) with minimal effect on corrosion resistance.
We've processed items in one of these processes, de-embrittled after chromating for 4 hours @ 120 deg C and Neutral salt spray tested, giving comparable performance figures with our existing process route of Zinc plate (0.0005") De-embrittle, Colour Passivate and Silicate Seal. (100 to 200 hours to white rust)
Though we are still part way through our program, the next step hopefully is to present the info to our customers and see if we can fully trial the process on components.
The solution is more expensive to buy and operates at a higher temp, however it is Hexavalent chrome free so no more chrome reduction costs, we still don't have enough data to estimate the cost of conversion but area working on it, the supply houses (vendors) do supply cost comparison illustrations.
Regards
Richard Guise- Lowestoft, U.K.
2001
Q. I'm not sure if this is a non commercial fashion but the Cr+6 free yellow passivation replacement that you're referring to. Is it chromiting by Surtec or something else. We are serving automative industry in Europe and desperately looking for Cr+6 replacements.
Thanks,
Elif Kiray Eres- Istanbul, Turkey
2001
Q, A, or Comment on THIS thread -or- Start a NEW Thread