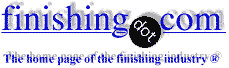
-----
Why Anodizing Uses a Hollow Copper Work Bar
Quickstart:
In production anodizing and plating, it is usual to suspend one or more plating racks from a copper bar or aluminum & copper structure that spans from one side of the tank to the other. This bar is often called a work bar or flight bar.
The tank is equipped with copper or brass contacts (often called saddles or v-blocks) mounted on the rims of the tank and bussed to the power supply. The bar sits down on these saddles. The bar carries the anodizing or plating current from the saddles to the racks; the racks in turn are conductive, carrying the current to the workpieces.
Q. Curious as to whether it matters if a copper flight bar for anodizing work is hollow?
That is to say, if the copper flight bar is like a pipe, but with closed ends, versus a solid piece of copper all the way through, will this potentially affect anything like carrying capacity?
I've usually seen solid pieces of copper or aluminum for flight bars.
Employee - Illinois
July 1, 2025
Tip: This forum was created to help build camaraderie through sharing tips, opinions, pics & personalities.
The operator & those readers who want that might not engage with anonymous posters.
A. Hi Matthew
The DC current used in anodizing and plating runs through the conductor, not on its skin as in some AC applications. So the reason for using a hollow bar is because more strength can be gained from a hollow tube than from a solid bar of the same weight.
For plating and anodizing purposes, a rule of thumb is that the current carrying capacity of copper is 1000 Amps/sq.in, and 500 Amps/sq.in. for aluminum.
But the work bar must also be strong enough for the span and the weight of the racks. Often this means that a hollow tube meets the load carrying and current carrying needs better than a solid bar; it's not unusual.
Luck & Regards,
Ted Mooney, P.E. RET
Striving to live Aloha
(Ted can offer longterm or instant help)
finishing.com - Pine Beach, New Jersey
Q, A, or Comment on THIS thread -or- Start a NEW Thread