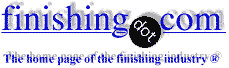
-----
DI Water is Etching Anodized Aluminum in the Cleaning Line
Q. Do I have an anodize seal or DI water rinse problem?
We are having some staining/etching issues with black anodize (organic dye) on 6061-T651 Aluminum after washing in a 5% concentrate cleaning solution (8 pH cleaner) and rinsing in DI water. Parts are being anodized per MIL-A-8625 Type II Class 2 Black.
We can hand-wash parts using a mild degreasing soap and hand rinse with DI water and not see any staining/etching. When we run the parts through our clean line, we see staining/ etching appear during the rinse stage.
We are currently using 18 MOhms DI water. I have heard that DI water this high quality can be corrosive because the water wants to replace the ions and cations that were stripped out. Could this be the case when cleaning black anodized parts?
The difference between the two parts is that the part on the left (part 1) ran our normal wash cycle and the part on the right (part 2), we added an extra rinse cycle.
The intent was to see if we were leaving a cleaning solution residue on the surface prior to drying. We thought that maybe the heat on the residue was causing the staining. This was not the case; we could see staining/etching on both parts prior to drying. Part 2 shows more staining/etching, as it had an extra rinse.
Our wash time, rinse, and dry time:
CL4 process
Detergent bath -> Rinse bath -> Rinse bath -> Dryer
Chemistry: pH neutral detergent, 18+ MOhm DI water rinsing
Bath temps: 122 +/- 5 degrees °F (or 50 °C)
Dryer temp: 200 +/- 5 degrees °F
Dwell times: 300 sec in each bath and in dryer.
Test part 1: entering dryer after final rinse (normal process)
Test part 1: post-dryer (normal process)
Any feedback would be appreciated.
- Boulder, Colorado
April 3, 2024
A. Hi Paul,
Your results from single vs. double rinsing seem to be showing that the DI rinse is attacking the part.
But I have to ask why you are rinsing for 600 seconds. 30 seconds in each rinse should be sufficient, and reducing the rinsing time by a factor of 10 would certainly greatly reduce any etching/staining the DI may be doing.
Luck & Regards,
Ted Mooney, P.E. RET
Striving to live Aloha
(Ted can offer longterm or instant help)
finishing.com - Pine Beach, New Jersey
Q. What would most anodizer's feel comfortable with time wise for the seal to stand up to a DI water bath?
I do not know why we rinse for 600 seconds, probably because that is what we have always done. We are in the light/optics business sector and must meet our customerr's cleanliness requirements for particles and molecular cleaning.
We have been treating the staining/etching issue as a supplier process problem. We do receive black anodized parts that do not etch going through our clean-line.
We also use this cleaning process to clean passivated stainless-steel parts. On occasion, we see corrosion problems when we wash passivated welded SS sheet metal parts. We see light oxide formation on parts of the weld. We blame the supplier for not doing a good job of cleaning the parts. I think that the time we expose the parts in DI water could be attributing to our failures.
- Boulder, Colorado
April 5, 2024
A. Hi again. I welcome other suggestions about seal time, but my understanding is that it should usually be about half of the anodizing time. There are various types of seals, but nickel acetate is probably the most common for black anodizing. You can check the anodizing seal quality via ASTM B136 rather than relying on your vendor's reports about seal time.
This site has thousands of informative dialogs -- you can try putting questions into the search engine with a lot of detail, like "sealing black anodize" for second opinions if no one else responds to your question.
Luck & Regards,
Ted Mooney, P.E. RET
Striving to live Aloha
(Ted can offer longterm or instant help)
finishing.com - Pine Beach, New Jersey
Q, A, or Comment on THIS thread -or- Start a NEW Thread