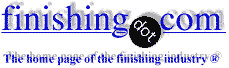
-----
Alkaline etch of aluminium prior to powder coating

Q. We are a low volume Audio-Visual accessories manufacture in the UK, producing products from steel and aluminium. These parts are mainly used in an indoor environment so do not require a high level of corrosion protection, the finishing of them is mainly for cosmetic reasons.
Currently some of our parts are powder coated by a supplier who have a mixed metal track system using an iron phosphate and fluoride additive pre-treatment.
We have had adhesion problems on aluminium parts in the past where on some parts, a slight knock will cause a small area of powder coat to come off. This seems to only happen in two situations:
1) On extrusions where the raw material looks in a poor condition when supplied.
2) On highly machined parts with very smooth surfaces.
Mechanically abrading the parts with a 120-grit abrasive to bare metal seems to cure this issue on the extruded parts but as the machined parts are irregular shapes, this is difficult to achieve economically.
This has led me to believe that the pre-treatment wash is not of sufficient time to deal with difficult aluminium components -- we have verified this by immersing the components in the wash solution for an extended period prior to running them through the standard process. This seems to also cure the problem but is not a process which can be performed on a production basis.
As I also get some parts anodised, an option my anodisers have suggested is that on the machined parts they can run them through their anodising pre-treatment line only (alkaline etch but no anodising), I would then drop them round to the powder coater who would run them through their standard process -- I would expect this to be within one week.
My question is, will the alkaline etch provide an improved surface for the iron phosphate and fluoride additive pre-treatment wash to do its job satisfactorily in the time (it seems to for the mechanically abraded components) and if so, will there be no adverse side effects caused by the alkaline etch?
Thank you and best regards,
- Birmingham, UK
July 25, 2022
A. Hi Darren.
Personally, I think a better thing to try than any of this is to see if your anodizers offer chromate conversion coating on aluminum; I'd bet they do. Then simply get some parts conversion coated by them, keep them clean during transit and while at the anodizer or powder coater, and then powder coat them 24 hours later without any other pretreatment and see how you do :-)
Luck & Regards,
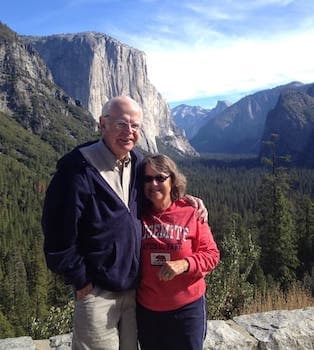
Ted Mooney, P.E. RET
Striving to live Aloha
(Ted can offer longterm or instant help)
finishing.com - Pine Beach, New Jersey
A. Add to Ted Mooney's advice. Keep the chromate conversion film very very thin. If the chromate film is too thick, the curing heat for the powder will out gas the moisture in the chromate and flake off the powder coat. This is also true of water base and solvent base paint, and 5541, hidden in the back, warns against applying the chromate too thick.
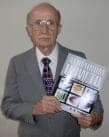
Robert H Probert
Robert H Probert Technical Services

Garner, North Carolina
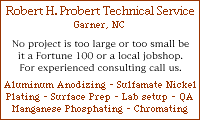
Q. Hello,
Thank you for the reply, unfortunately my anodiser doesn't offer any form of chromate conversion coating at all - there used to be a local anodising company that did (which I used) but they have since closed down. I have used a few different anodising suppliers since, but have had to keep swapping due to pricing and quality issues - that's another story. I could get a chromate conversion (which I would probably not use due to the environmental issues) or the chrome free versions but when I spoke to the technical department of a manufacturer of one of the chrome free versions, he seems to think that the powder coat pre-treatment would strip the coating back off.
I'm mainly trying to get around my powder coating problem initially using my current suppliers .I know sometimes you can try to do something that seems easily/cheaper only to get issues later on, but I wanted to know if it is a no-go. From my understanding, the alkaline etch will open up the surface of the aluminium, which I believe is a poor surface to be left as-is. I was hoping the powder coat pre-treatment / actual powder coat might neutralise this issue.
Best regards,
Darren
- Birmingham, UK
Q. Hello.
Sorry, I've re-read your reply -- you're talking about powder coating without running the parts through the wash/pre-treatment?
I've already thought about this and it is possible, but the way the track system is laid out, there is not a lot of room between the wash and the powder coating booths to load the conveyor. Also, I know they do not like running the line non-standard.
Thanks,
Darren
- Birmingham, UK
A. Hi again Darren. You can't do what is logistically impractical given whatever situation you find yourself in. Still, we have other readers, so a point that I want to make even if it is not applicable to you is that iron phosphate or 'mixed-metal treatment' is not the conventional nor best treatment for aluminum; it's a compromise done when you must handle both steel and aluminum.
Chromate conversion coating, or more recently trivalent chrome conversion coating, is the treatment of choice for aluminum, and the standard approach. The only thing that is 'iffy' or strange in your case is that, since your powder coater doesn't offer it, you'd have to have it done elsewhere, monitor the delay between conversion coating and powder coating, and keep the parts clean during that interval.
Luck & Regards,
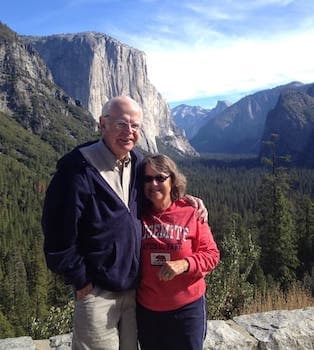
Ted Mooney, P.E. RET
Striving to live Aloha
(Ted can offer longterm or instant help)
finishing.com - Pine Beach, New Jersey
July 27, 2022
Hello Ted,
Thanks for the reply again.
I going to look at some powder coat suppliers that use a track system with chromate/non chrome aluminium pre- treatments local to me (within 20 miles) - I might check them out. I prefer track system coaters to job shops as I don't think the smaller places normally produce an acceptable finish when you drop round 500 of the same part to coat (areas not coated, impurities in the surface, etc). Like you say, it might be just easier and cost effective getting someone to do everything correctly than trying to do a half job. It's a pity because my local powder coater is only a few hundred yards away and produces a very nice finish -- some supplies talk up their finish quality, but when it comes to it there always seems to be issues.
Q. It would be nice if anyone can come back if the alkaline etch would be detrimental when powder coating though -- if only for the knowledge gained.
On a separate note -- does bead blasting the aluminium first help with adhesion as some of my local job shops seem to think that is all you need to do when powder coating aluminium (no other pre-treatment)?
Thank you again for taking the time to respond,
Darren
- Birmingham, UK
A. Hi again. Alkaline etching will likely have no ill effect, nor should bead blasting. Both slightly increase the surface area and thereby the "tooth". They don't sound like bad ideas; but they do, to me, sound like band-aids. Nothing wrong with trying them in my opinion if it is logistically impractical to precede the powder coating with chromate conversion coating.
Luck & Regards,
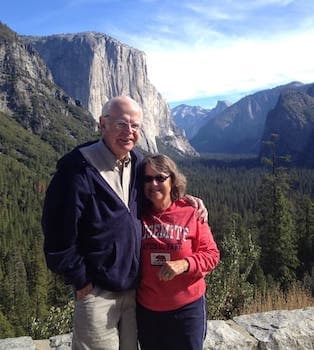
Ted Mooney, P.E. RET
Striving to live Aloha
(Ted can offer longterm or instant help)
finishing.com - Pine Beach, New Jersey
July 27, 2022
Hello Ted,
I think I can summarise the preparation for powder coating aluminium from best to worst as:
Best: Chromate conversion pre-treatment + powder coat
Intermediate: Mechanical abrasion/bead blast/ alkaline etch + powder coat
Worst: No preparation + powder coat
Each of the above may work on a product dependent on the application/environment.
Thanks to everyone for the help.
Darren
Business owner - Birmingham, UK
Q, A, or Comment on THIS thread -or- Start a NEW Thread