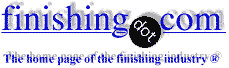
-----
Coating for Spillway Gate Chains
Q. We are designing new spillway gate chains for a project. These chains are large. One pin (13" lg. x 2.68" dia, 21 lbs) runs through eight side bars (17.625" x 4.5" x 3/4", 14 lbs) to make up one link. 130 pins in one chain length, 512 side bars. Total weight is about 5,600 lbs assembled.
About 1/2 of the chain length is typically submerged depending on headwater elevation, then when the gate is raised, these chains rise out of the water until the gate is lowered. The constant in and out of water is a pretty rough environment, so they corrode, especially when they are not greased. Maintenance manuals require greasing of the chains every four years (which isn't frequent enough imo). Average life of these chains when greased properly is about 20-30 years, but if they are not greased properly, then about 10-20 years. Projects where the chains are not submerged constantly have chains that have lasted over 70 years. I am trying to do my due diligence to see if there is a coating system that can extend the life of the chains (as long as grease is still applied periodically).
In the past we have prescribed a minimum 25 micrometers of electrodeposited Zinc, a yellow Dichromate passivate and an application of colorless Ultra-Seal. It has worked average. When the chains are not greased well, this coating system will start to degrade after 10 years or so. I believe the constant binding of the side bars on the pin also wear away the coating over time.
I want to have a coating system that will provide good protection and yet won't dramatically increase the price of the chain fabrication. What coating system would provide excellent protection and what coating system would provide good protection and still be economical?
- Nashville TN
June 16, 2022
A. Hi Paul. Manganese phosphate is designed to hold grease, and it's the 'break-in' coating on automotive parts, so it will not bind or gall. I think if followed by dri-lube process would be relatively affordable and I think it would hold up. Joseph Menke has a hard-to-find book on phosphatizing, but reviewing this paper of his should give you a good idea as to whether I'm on the right track or I missed something.
Luck & Regards,
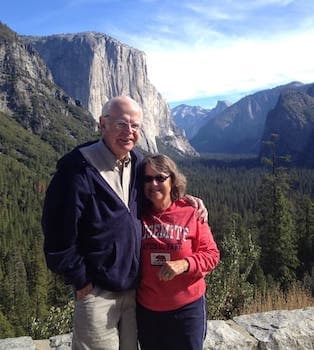
Ted Mooney, P.E. RET
Striving to live Aloha
(Ted can offer longterm or instant help)
finishing.com - Pine Beach, New Jersey
Q, A, or Comment on THIS thread -or- Start a NEW Thread