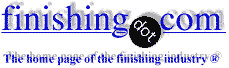
-----
Anodizing seal issue on bead blasted areas
Q. Hi Guys,
Darren here from New Zealand
We have both 6000 series and 7075 parts anodized, most of the parts a glass bead blasted on the outside of the part, we have about 70,000 parts anodized per year.
Before our product goes out we give it a rub down with WD-40
⇦ on
eBay
or
Amazon [affil link]
, that gives it a nice even look.
Early December we had some of our 7075 parts come back, once rubbed down with WD-40 the bead blasted surface would start to dry out and give a dry gray look, rather than a nice black as we are used to, applied WD-40 multiple times and it would always dry out within minutes. We have been running these parts for 10+ years and have never had this issue before.
I took some of these parts home and boiled them in DI water for 15 minutes and the issue goes away, parts are back to normal, so this would indicate a seal issue, but why only on the bead blasted surface? the non blasted surface didn't have this issue.
The above parts are machined on our big CNC. Parts that were machined on our smaller CNC, both 7075 and 6000 series do not present with this problem. One difference is the parts that are machined on the big CNC are etched for 90 seconds, the parts on the small cnc are etched for 4-5 minutes.
I believe the parts are sealed in Nickel acetate for 4 minutes, parts are semi-hard coated to 25 micron.
The anodizer changed the seal tank and the problem went away.
I would like to understand what was happening, why was it only the blasted surface that was causing an issue, why didn't the parts on the other machine have this issue? Would the etch time have any influence, what about contamination in the bigger machines coolant?
See picture of single stack, parts on left are good, parts on right have dried out, stack was wiped down with WD-40 at the same time:
This was one of the worst lot of parts, some would come back blotchy:
Thank you.
Darren Toms [fictitious]- Hamilton New Zealand
January 28, 2021
Tip: This forum was created to help build camaraderie through sharing tips, opinions, pics & personalities.
The operator & those readers who want that might not engage with anonymous posters.
A. The bead blasting changes the texture of the surface, then the pores build randomly (instead of straight perpendicular) and when magnified by the anodic film, then looks different. Also, the work hardening of the blasting affects the size of the pore, already almost too small to dye, and if borderline to small, as in hard coat, it will not seal. Your extreme hot water at home completed the seal.
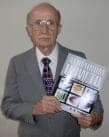
Robert H Probert
Robert H Probert Technical Services

Garner, North Carolina
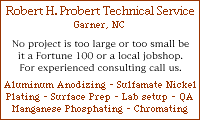
January 29, 2021
A. Hi Darren,
Frankly, I don't suppose problem of source is "etching duration". According to your survey, most likely problem is sealing bath but then you ask why did not occur in smaller CNC machine as rightly? One possibility we you can focus the coolants of machines. Do you use same coolant for both machines or different coolant? Also, what's the pH value of coolant? If you use different coolants for both machines, I'd advise you to replace coolants between each other and survey consequences.
Good Luck
- TURKEY Sakarya
January 29, 2021
![]() ![]() |
A. Dropping by to add from personal experience that glass bead blasting prior to black anodize has caused us problems in the past; in fact your photos are giving me flashbacks! Ours, though bad enough to reject for shipment, were not as badly blotched as yours, so as other commenters have noted, there are other areas for investigation and/or improvement in your process for sure. ![]() Rachel Mackintosh lab rat - Greenfield, Vermont January 30, 2021 Q. Thanks for the replies. - Hamilton New Zealand January 30, 2021 |
A. Frankly, I do not understand your problem's source. Long or short etching duration does not effect the sealing quality as you mentioned. In other words, sealing quality is independent from etching process. I think lack of one point in this situation as data. But if you say I am sure then I only advise you: if I were you I would always use small machine instead of big machine :)))
Alaattin Tuna- TURKEY Sakarya
February 1, 2021
A. 1. You say that "One difference is the parts that are machined on the big CNC are etched for 90 seconds, the parts on the small cnc are etched for 4-5 minutes", then my question is "Why do you use different etching time?"
2.Nickel acetate sealing time of 4 minutes is not enough for thickness of 25 µ.
- Singapore
February 2, 2021
Q. Hi,
The shorter etch time is because that particular alloy is quite grainy, if we etch to the standard time they come back very grainy once anodized. We import 7075 from two different mills. Both lots are having this seal issue.
We had some parts come back today that were from the smaller machine these parts are having this same issue, so that rules out the machine as the cause, the only other process that all parts go through at our end is bead blasting. I have purchased some alloy oxide to see if that helps at all.
To note, the worst of the parts that came in today had a purply colour to them.
- New Zealand Hamilton
February 15, 2021
February 16, 2021
Q. Hi guys,
We just had some more parts come in today with this same issue scattered through a few of the parts, I have notice the parts with the issue have a slight yellow tinge to them and had previously notice quite a purple colour to some of the bad parts.
The tinge seems to be on the blasted and non blasted surface.
Would this be related to the seal or dye PH as mentioned above by Rachel Mackintosh?
See attached picture:
- Hamilton New Zealand
A. Frankly speaking, the part shown on the last photo is not black enough, most probably due to the dye concentration too low (provided anodizing thickness is higher than 10 µm).
John hu- Singapore
February 17, 2021
Q, A, or Comment on THIS thread -or- Start a NEW Thread