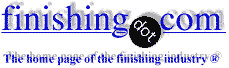
-----
Do I have to passivate after mag particle inspection?
Q. When performing magnetic particle inspection on a 15-5PH part, does one have to passivate it again if it has already been passivated prior to mag particle?
We have a group of parts that were manufactured and passivated. They then went through testing and are undergoing NDT (mag particle) again to ensure we did not have any structural damage during test. Some of these parts are Nickel plated which adds to the issue of having to re-passivate. Is re-passivation really required?
- Queens, New York
November 23, 2020
A. This is a great question. Like, really great. It seems totally reasonable to remove any residual iron after MPI. But if it can simply be washed off, why re-passivate. Thats how i read your question. I see stainless parts coming in for vapor degreasing, where mag particle was a prior op, (they run tests, ultrasonic clean, and then vapor degrease) but I've never bothered to track the flow as to whether they had been previously passivated or come back to us as a pasivate job (literally two separate shops divided by basically a saloon door lol but it's easy to be nosy).
I'm going to go ask some colleagues some obtuse questions tomorrow.
I do have a story of MPI fouling our vapor degreaser so badly with iron and moisture that its internal welds lost their passivation and started rusting, though! That's a cautionary tale on a bit of a different subject.
Post-MPI treatment troubleshooting is something I'm going to run into inevitably. Thank you for the prompt! Bookmarked, and will return!
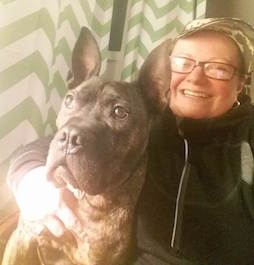
Rachel Mackintosh
lab rat - Greenfield, Vermont
November 25, 2020
Aloha Rachel!
Thanks for the information. This helps reaffirm my belief that if properly cleaned there should be no reason to re-passivate. Let me know if you come across any additional information.
- Queens New York
November 30, 2020
A. The MPI guy confirms that no, passivate is not a subsequent op post- MPI. The two step cleaning process is enough.
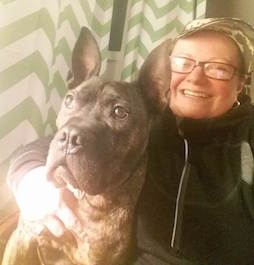
Rachel Mackintosh
lab rat - Greenfield, Vermont
December 1, 2020
A. I'll just throw in a reminder here of what passivation on stainless steel actually is: an acid treatment that removes surface iron and enables a surface layer to form that is primarily chromium oxide.
People ask me all the time if this or that is going to "damage the passivation", like solvent cleaning. Nope. You only need to worry if:
* Iron from an outside source is deposited on the surface
* A chemical attack (generally something high in chloride) eats through the chromium oxide layer, exposing new iron
* The chromium oxide layer is mechanically damaged, either accidentally like a scratch, or intentionally in a manufacturing or re-work process.
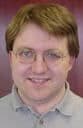
Ray Kremer
Stellar Solutions, Inc.

McHenry, Illinois
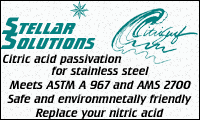
December 8, 2020
A. Hi Ray!
I think the big question here is whether, as you said, we've got free iron deposition from the mag particle inspection process. And then the secondary question of, does it (or CAN it) actually react with a previously passivated part, and under what conditions . Im totally co-signing this question as process improvement. At this point, the assumption in my shop is that the washing process post MPI is adequate, but if your lab work has brought up any hints that it does in fact deposit iron, and how to mitigate that, I'm all ears!
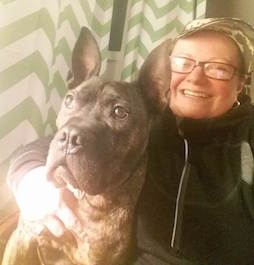
Rachel Mackintosh
lab rat - Greenfield, Vermont
December 10, 2020
Rachel,
I don't know much about MPI, but I assume the stuff is not particularly adherent and is designed to be rinsed off after testing easily enough. Most of the iron contamination you see in the industry is when steel materials have scratch or scrape contact with the stainless, either incidentally during transport or as part of the manufacturing/fabrication process.
Of course the proof is in the pudding, if the stainless readily rusts, then contamination from something is likely, if it does not, then there clearly wasn't a problem. Something like copper sulphate
⇦ on
eBay or
Amazon [affil link] testing could be done, perhaps, in order to satisfy doubters that the MPI material was sufficiently removed.
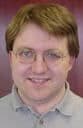
Ray Kremer
Stellar Solutions, Inc.

McHenry, Illinois
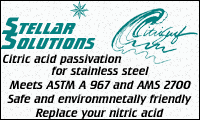
December 10, 2020
Q, A, or Comment on THIS thread -or- Start a NEW Thread