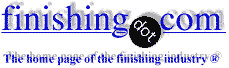
-----
Solutions to Problems that calcium causes in the electrodeposition of copperProblems galvanizing thin or very thick plates -- what are the limits?
Q. Hello. I am an architect in Oklahoma City. During my career, I've been told a variety of things about hot dip galvanizing. One contractor told me that if you try to hot dip galvanize steel less than 1/4" thick, it will twist up due to the heat. Years later, another contractor told me that was not true, and successfully hot dipped a fabrication of 1x1x.188 welded steel for me. Now I am being told by another contractor that he cannot hot dip a fabrication made of 1/8" plate because the welds will break. The fabrication is a cover for an exterior, ground mounted exterior light. Basically, it is a 3' cube with two adjacent faces missing, and all edges continuously welded and ground smooth. Am I getting duped again? If not, are there some rules of thumb to keep in mind about thickness and welds?
Michael E. Hoffner, AIA- Oklahoma City, Oklahoma
2006
Galvanizing of very thick plate is silvery and non-adhering
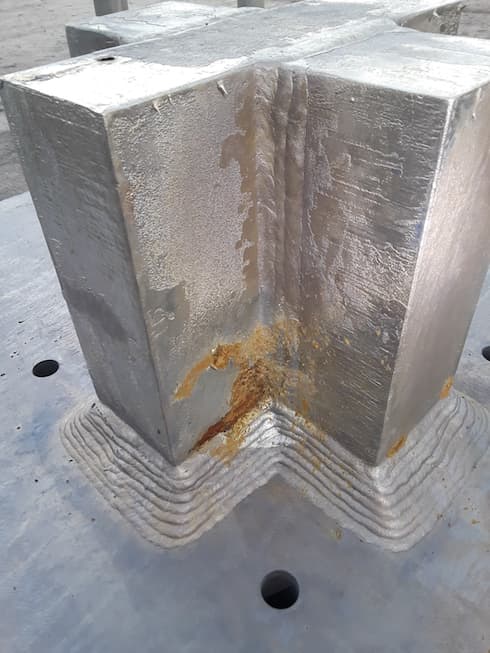
Q. Hello all. I am a CWI/QC at a steel fabrication company in Texas. I have 3" thick embed plates that are 3 foot square with shear keys on them made of 4" thick plate -- 2100 lbs. They are coming back from our galvanizer with bright silver thick galvanizing in a roughly circular pattern around the "core". The first 100 of these were passable if not great. As the next batch is getting started they had the same silvery pattern, but also bad adhesion and blistering at the inside corners. Is this just a need for longer time in the tank to get this mass up to temp?
Justin Lewis- Houston Texas
August 12, 2020
A. Sir, The presence of orange rust stain is interesting. It may be a pocket weld that has expelled some process solution, perhaps iron contaminated flux. How thick is the galvanizing? Is the peeled off coating brittle or bendable? This thick of steel may be more suited to powder zinc coating. Grit blasting prior to galvanizing may solve the problem.
Regards,
- Hot Springs, South Dakota
August 13, 2020
Q. Thank you Dr. Cook. There are several things that I believe can be logically ruled out. Neither the welds or contamination are not the problem. The same defect happens in the same four places on every piece and nowhere else...probability tells me to put weld quality aside and think about process and geometry. That said the adhesion in these corners bad, as you can guess (see image).
The thickness of the zinc in these areas is excessive. Blasting to achieve better adhesion sounds good, but these areas have basically zero gamma. I have heard different tank times for these from the galvanizer (between 25-40 minutes) but not being a galv expert, I can translate that into an application for that plate thickness or tonnage. Your thoughts are much appreciated!
Justin Lewis- Houston Texas
August 14, 2020
"Adhesion" is a difficult term in galvanizing, as it gets compared to adhesion in paint systems. Galvanizing "sticks" to steel by alloying to it. Some zinc migrates into the steel, and some iron into the coating. There are several layers of alloy of differing compositions in the thickness of the coating.
Coating thickness is affected by several factors: steel chemistry, immersion time, and surface roughness are the primary ones. Shotblasting doesn't affect "adhesion", but greatly affects coating thickness.
Areas that look like (in paint terms) an adhesion failure, as in your pictures, are not that the coating has become detached, rather that it didn't alloy, and was probably not there as a coating at all. Then again, it is possible to get some form of delamination of the coating, most commonly at one of the alloy layer interfaces where a fin of zinc, or zinc-iron alloy detaches, cleaving parallel to the steel surface, along the alloy layer line. This is almost always due to excessive coating thickness, and usually reasoned back to one of those causes listed above.
The immersion time in galvanizing refers to the time the steel is immersed in molten zinc. Its primarily affected by thickness. The steel needs to get to the zinc temp (usually c 450 °C), so thick steel takes longer. But that longer immersion time then affects the coating thickness, leaving a thicker coating. Coatings in the >800 micron range often suffer from problems of delamination, or being brittle alloy from chipping (resistance to mechanical damage).
Part of the roughness of this coating appears to be derived from the surface smoothness of the steel. Galvanizing will make a rough surface look worse! Gas cut (as these appear to be) will not achieve a smooth finish.
The brown stain in your first image looks to be two separate things. Chemical weep from a pinhole in the weld (as Tom Cook said) that's the lower part, deeper colour. The rest looks like flux/ash stain/deposit on the surface, probably able to be removed by wire brush.
My best guess as to the cause of the missing coating on lower image is surface not cleaned prior to immersion in zinc. Some contamination prevented cleaning in acid. If it's not chemically clean and free of oxides, it won't galvanize.
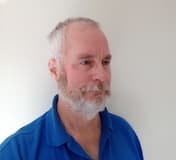
Geoff Crowley, galvanizing consultant
Crithwood Ltd.

Bathgate, Scotland, UK
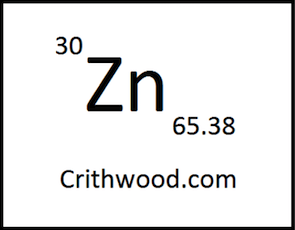
September 8, 2020
Q. Thank you, Geoff for the insight.
In trying to eliminate the possible causes of defects on top of the plate that you've listed, I've taken a look at the bottom. I finally got around to tilting up one of these for a photo of the bottom side. The silvery circle in the center of the photo is found on all of these plates. Taken with the silvery circular areas above one can define an imaginary silvery sphere. This circle in particular is smaller in diameter and is from the third run of plates representing increased immersion time and significant improvement in adhesion in the corners.
Since the steel needs to get to ~450 °C to accomplish the needed alloying this piece's geometry poses a particular problem. In explaining to our NCR vendor and others, I have likened it to grilling an oddly thick steak, which is thin around the edges and has an abruptly thick center 4 times thicker than the surrounding edges. The edges are going to be well done while the center is still raw. The circle of a different color in the photo is found on all of these pieces.
So the cause question would seem to be 'why didn't the circular area not reach the correct temperature?' And the answer would seem to be 'because the stout shear key forms a large heat sink directly above it'.
So my process question to the experts is:
'Will increased immersion time to accomplish adequate alloying near the core of this piece, cause a problem of too much immersion time (too thick coating?) for the thinner parts?'
...and THANKS! for your continuing input :D
Justin Lewis
- Houston Texas
Justin
thanks for further explanation of the issue.
I think you're right about the steak being under-done in the thick part - a good analogy. That chunky section (X in cross section) standing above the plate is indeed a big heat sink, and probably does case a difference in achieved temperature of the base plate. Quite why a circle is a bit mysterious, but likely just the geometry. It's common enough to see differences in colour in galvanizing, between dull grey to shiny silver, even on the same piece of steel. The explanation doesn't always satisfy those seeking aesthetics from a coating only ever thought to be functional!
What would be interesting is to measure some coating thicknesses on this - especially between the circle area and the surrounding area. I suspect you will find little difference.
You mention immersion time on the pretreatment areas... "Caustic time". Presumably a degreaser with a NaOH base - the most common in galvanizing. The job of that bit is just that degreasing - getting any traces of oil off. Oil sources can include a few quite peripheral processes, such as anti-spatter sprays that welders use, markings left by steel stockholders, layout markings, cutting fluids, drilling lubricants. Anything that prevents the acid "pickling" the steel. Two acids are common, both dilute, being hydrochloric and sulfuric (sulfuric). The choice is often as a result of availability, and commonly Nth America uses H2SO4 more than Europe, and Europe mostly HCl. Whichever, both are dilute therefore a water based solution, that is prevented getting at the steel by the various surface contaminants mentioned. They must all come off. If not you get bare patches that look often, exactly like your patch.
Be wary of just increasing the immersion time. If your objective is to eliminate the circle on the underside, I'd ask "why?". Does it not have sufficient thickness of coating? (If not that is indeed a problem to solve). If it does, then its an aesthetic issue, and probably meets the standard you asked for in galvanizing. (You did specify what standard to galvanize to??)
If you think that longer immersion time will fix the bare patch issue, I disagree. That looks far more like unclean steel. (oily?, paint? other?) If it's not clean out of the acid, there's no chance.
In a part like pictured with what appears to be flaking off the X piece, just above the weld, is there any coating at all? A thickness meter will tell you. Is that black steel we're seeing with no zinc? Or is it an area with say 10-20µm thickness whereas the surrounding has 200µm or more?
If the former (black, thickness = 0), then it's a pretreatment issue. If (less likely) its thin (alloy only) then its a different issue, with a more elusive answer!
There's another possibility often call "airlock". Which way were these hung? It's possible to hang (suspend) steel items in a way that either collects zinc which can't drain out, or holds air underneath, so that when the item is immersed, no zinc touches that bit holding the air. The air gets a little compressed (liquid zinc density about 6.8kg/litre, and distance below surface might be a metre?), but is still enough to prevent galvanizing. This manifests as a bare patch similar to your mark. The hint to this is in your most recent picture where there's a sign of a sort of "tide mark" in an inverse pyramid shape, whose apex is at the bare patch. If in the suspension orientation there's scope for airlocks or zinc traps, then figure out another way to suspend it.
Hope this helps.
Geoff
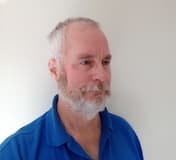
Geoff Crowley, galvanizing consultant
Crithwood Ltd.

Bathgate, Scotland, UK
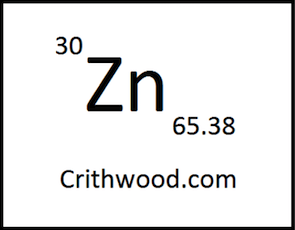

Q, A, or Comment on THIS thread -or- Start a NEW Thread