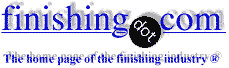
-----
Manual anodizing versus automation
Q. Hi Ted,
I have been asked to evaluate the pros and cons of automating a soft anodising line for the processing of aerospace components that we have previously processed manually with great success. The job was sub-contracted to an automated line. Some of the parts from the automated line were found to corrode in service, an issue that did not present itself when we anodised them manually. I am aware that the capital cost to us of this would be high, there would be manpower advantages, and perhaps cost savings in the long term. However, the quality cannot be maintained with the automated line that was seen with the manual approach. In yours, or the readerships, opinion, could I legitimately argue that the differences in quality could be due to the automation? Although perhaps in theory giving a more consistent product, it would be less able to cope with variations in alloy, contamination prior to cleaning, etc., that would occur with any process over time, that could be spotted and adjusted for by an experienced manual operator. Any thoughts on this would be welcome.
Thanks and best regards,
- A covid-free rock in the Irish Sea.
July 29, 2020
A. Hi Mark (I hope you see this; your email address is 'unroutable').
I spent most of my career automating plating & anodizing lines as a plating equipment engineer. But that doesn't really qualify me to answer your question ... because quality is a management issue, not a facilities issue.
Consider the many threads here over the years bemoaning how difficult color consistency is in anodizing, all the more so with the high strength alloys like 7075. And then Apple decides to make the iPhone 6 from 7075 and proceeds to make millions of identical units without regard to "variations in alloy, contamination prior to cleaning, etc., etc., blah-blah-blah" Clearly, Apple has an advantage over mom & pop, but their management philosophy was also key.
At the other end of the spectrum, I did some consulting for a plating job shop whose QA manager spent all day every day in his air-conditioned office in front of several computers running all sorts of SPC programs, and printing out reams of paper. In one case he was struggling to solve the question of why his automated nickel barrel line produced good parts, then random batches of largely bad ones ... whereas 15 minutes out on the line revealed to me that the barrel rotation device on the electrocleaner was poorly adjusted and some barrels did not rotate for electrocleaning, a situation that had gone on for many days :-(
Were the loader/unloaders poorly trained in not telling anyone, or poorly motivated to do so? Or was this observation up to the plating foreman? Or was the problem a lackadaisical maintenance department ... or an out-of-touch QA manager? Regardless, it was a management problem, not an automation problem.
The fact is, if your company's motivation for automation is quality improvement, automation can improve quality not reduce it. If the motivation is reducing labor hours, it will reduce labor hours but quality will probably suffer, not improve, partially because the remaining employees may feel they are chattel you haven't figured out how to dispose of yet. Automation can improve consistency and thereby improve quality, but responsibility can only be assigned to people, it cannot be assigned to machines. When the machine isn't producing quality parts, it's not the machine's fault, it's somebody's responsibility :-)
Luck & Regards,
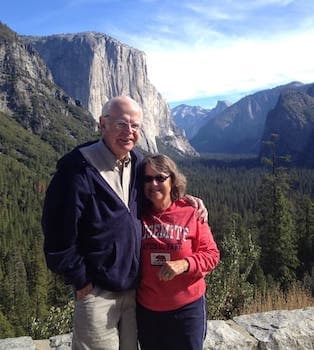
Ted Mooney, P.E. RET
Striving to live Aloha
(Ted is available for instant or longterm help)
finishing.com - Pine Beach, New Jersey
August 2020
![]() |
A. Mark - Green Mountain Falls, Colorado August 3, 2020 A. Mr Mooney's answer is, right on. My short answer would have been, "it depends on whether production or job shop." I recall being involved some years back when one of our Air Force overhaul facilities wanted to add automation in their proposed new shop. It was plainly a job shop, 100's of different kinds, shapes, alloys, thickness, etc. Automation was a disaster for them (at great government expense.) Another race car parts shop, with theoretical school boy engineers, set up automation, I was called in after the fact,I showed them they could increase production 5 times if they turned off the automation and run the hoists manually. Heed Mr Mooney, but be careful, think. ![]() Robert H Probert Robert H Probert Technical Services ![]() Garner, North Carolina ![]() August 4, 2020 A. The temptations of automation are obvious. Higher throughput, reduced labour costs, consistent product etc. ![]() Geoff Smith Hampshire, England August 4, 2020 |
A. We have two independent anodizing lines; one of the "automation" type, other one "manual". Automation line was installed by Italian company 3 years ago. Manual line was installed more than 10 years. By the way I have been working at this plant more than 10 years :)
So I have enough experience for comparison both lines. Absolutely, I prefer automated line in spite of some disadvantages and risks. I full agree with Ted. Up to me, key word is here "maintenance" (mechanical, electrical, chemical). If you pay attention to these triple maintenances and good survey the automation system, then you will see quality anodized products, more homogeneous production, less water/chemical consumption, cleaner rinse/process baths, etc. To get rid of human power in anodizing/plating jobs is very important to me.
- TURKEY Sakarya
August 6, 2020
August 18, 2020
Thanks to you all for taking the time to answer my question.
I have put a report together, (hopefully balanced), with my thoughts and your advise. at our site we would not be able to just simply plug an automated line into our current operation. It would have to go in different part of the site, require it's own energy and water supplies, as well as it's own rinse cleaning and effluent treatment equipment. So the savings that some envisage evaporate very quickly on those grounds alone.
As to quality, from all your comments, it appears that there is not much to be gained relative to our current manual operation.
So, my gut is to stay manual, and make good use of our well trained platers.
Thanks again
Mark
- A still covid free rock.
Q, A, or Comment on THIS thread -or- Start a NEW Thread