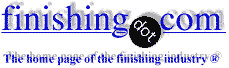
-----
Black Oxide with Supplemental Coating
February 17, 2020
[sorry not posted until April 3]
Q. My name is Tyler Borton and I am an engineer for an optics manufacturer. We currently have 3 specifications for black oxide. 1) Standard Black oxide 2) Black oxide with teflon (supplemental dry coating) and 3) Black oxide on Stainless. I am attempting to refine our specifications but am having a difficult time deciding all of the rules and testing requirements for each spec. Any feedback, guidance, or recommendations based on best practices in industry or literature would be helpful. Right now, here are my ideas.
1. Black Oxide
- We need a certain amount of parts, primarily made of brass, to be black in finish.
- This should be used for all materials other then carbon steel or stainless steel
- Spec should call for parts to come back uniformly black
- Spec should call for parts to come back with oil on them
- Spec currently calls for "increased corrosion resistance" but this should probably be removed as BO by itself provides no corrosion resistance
- Spec should call out for the parts being able to pass MIL-DTL-13924
[⇦ this spec on DLA] (is there another spec for non steel materials?) oxalic acid test for Class 1
- What should it say for being indelible or smut testing with the oil?
2. Black Oxide with Teflon
- We need a certain amount of parts that are made from carbon steels to be corrosion free, black, and dry.
- This should be used for carbon steels
- This should be changed from "with teflon" to "with a dry supplemental coating"
- What type of testing should we call out in the specification?
3. Black Oxide on Stainless
- We need a certain amount of parts made from stainless steel to be corrosion free, black and dry
- This should be used for stainless or corrosion resistant steels
- The spec should call out for the parts to be black, dry, corrosive free, and subject to testing per MIL-DTL-13924
[⇦ this spec on DLA]
Engineer - Greeley, Colorado, United States
Q. My production team (optics industry) is working to refine our methods for processing parts prior to assembly of our products. We have parts made of copper alloy, mild steel, and stainless that all get black oxide finish. I believe I want all of these parts to get a supplemental oil finish after they are black oxided, and I want this to come to us "dry to touch", however I am not quite sure how we should process these once they arrive. My questions/concerns are as follows.
1. I need them to pass a smut test, in which I believe I would need to remove the oil. What is the best way to do this prior to assembly?
2. There can not be out-gassing which is even more reason to remove any oil.
3. If the cleaning process involves a solvent, what recommendations are out there and can I use it for all 3 base metals?
Engineer - Greeley, Colorado, United States
April 3, 2020 2nd Request
A. Hello Tyler,
Having helped develop a black oxide process for MIM parts with some of the requirements you are looking for. I will say it is extremely difficult. The smut you get is from the oil applied by the processor, basically a sealing process of sorts; it helps with corrosion resistance, also color fastness. If you remove the oil you are degrading the corrosion resistance of the piece; also color will change somewhat. We experimented with oils we were using to get the results the customer wanted in a smut test. Another issue I imagine you have is when you pull a vacuum for the optics it results in outgassing. Bad for optic tubes...
If it must be black oxide, have your vendor experiment with different oils, waxes to (seal). Also ensure it is a Hot Black Oxide Process.
But I would try to get away from black oxide for this application. Black Zinc possibly? Price point is always a consideration, you must look at the whole picture. It costs more to process, but what does it save down the line?
Hope this helps!
Steve
- Colorado Springs, Colorado
Q, A, or Comment on THIS thread -or- Start a NEW Thread