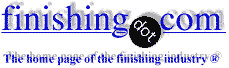
-----
How can I improve my DIY black oxide coating process?
Q. Hi everyone. I've recently been experimenting with at-home black oxide coating of iron and steel parts. The primary goal of this particular process corrosion protection with minimal use of potentially dangerous chemicals. Obviously this will limit the durability of the coating, but there are other processes for when more corrosion protection is required.
My last attempt was with some parts for a transfer case linkage of a Jeep. These will be exposed to the elements, so will be a nice test of the coating's durability for the parts that weren't painted. I don't expect it to hold up terribly long with the roads being salted soon, but the whole thing is going to be replaced soon either way.
Before picture of parts:
After picture of fasteners:
After of larger piece:
After of piece with brazing repair:
After of difficult piece:
After of fasteners with mineral oil coating:
The current process is this:
1. Use electrolytic rust removal to remove any built up rust and contaminants.
2. Ultrasonic cleaner bath with degreaser
3. Ultrasonic cleaner bath with white vinegar
⇦in bulk on
eBay
or
Amazon [affil link] (this also helps to remove the stubborn black deposits that can happen with the electrolysis process. Not sure what that stuff is)
4. Paint the parts with hydrogen peroxide saturated with non-iodized salt. This causes quick surface rusting. Heating the H2O2/NaCl solution and the parts can speed it up a bit.
5. Boil the parts in clean water for ~10+ minutes.
6. Repeat steps 4/5 until happy with the finish.
7. Dry the parts and coat them in white mineral oil (liquid paraffin).
Any thoughts for how to improve this? I have a few more specific questions too:
1. Anyone know some more details of the chemistry behind this? My limited understanding is that heating red rust (Fe2O3) in the absence of oxygen converts it to black oxide (Fe3O4). But it seems like that process itself will release oxygen, or it will also involve some of the iron in the substrate.
2. Any idea why some parts, or even just sections of a single part, are more difficult to rust and blacken?
3. Some similar processes recommend 'carding' after each boil. Usually using something like #0000 #0000 steel wool
⇦ on
eBay or
Amazon [affil link] to lightly remove the outermost layer of black oxide. From what I can tell, this is purely for appearances in the final product. Does it actually contribute to durability though?
4. I like mineral oil for coating because it doesn't dry or go bad, and doesn't have various additives or contaminants to worry about. Any other options to consider?
5. I've wondered about building an automated device that raises and lowers parts into boiling water. The idea is that sitting above boiling water will fairly quickly cause rusting (though not as fast as the H2O2/NaCl), then immersing in the water will convert the rust to black oxide, then repeat. Shouldn't be too hard to put together a valve to maintain the water level too. Any thoughts about this compared to my current process? Quite a bit more wasteful as far as energy goes, but in winter at least the extra heat and humidity is nice!
That's all I've got for now. Thanks for any input!
- Bowie, Maryland, USA.
November 16, 2019
Nadcap Chemical Processing Auditor - PRI, traveling
Process Engineer / Chemist - Denver Metal Finishing, Colorado
Q, A, or Comment on THIS thread -or- Start a NEW Thread