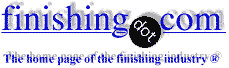
-----
Paint adhesion is poor on Welds
Q. I have a factory receiver hitch on a '23 4Runner and the paint came off the weld joining the bracket and the receiver tube.
A few weeks earlier, I had pulled a trailer (well within spec) using a weight distributing hitch (WSD). Did that WSD flex the receiver tube or weaken the weld in some way to cause that paint to flake off?
- Denver, Colorado
July 27, 2023
A. Hi S.,
A pic to mooney@finishing.com for posting here might help. Manufacturers routinely severely bend painted sheet metal to test adhesion, apply very sticky tape to try to pull the paint off, cut scribe marks in it to make sure it doesn't chip beyond the scribes, etc. The short answer is that the paint should not have come off, if that is your question.
But whether the hitch was overloaded and the welds compromised is not something I can say, nor can the paint.
Luck & Regards,
Ted Mooney, P.E. RET
Striving to live Aloha
(Ted can offer longterm or instant help)
finishing.com - Pine Beach, New Jersey
Thank you! That makes sense.
- Denver, Colorado
⇩ Related postings, oldest first ⇩
Q. I have a situation where cold rolled steel is being welded and then painted with electrolytic dip process (e coat), however, there is no paint adhesion to the welds. I have been told that this is due to a "silicon" component of the metal rising and hardening on the surface of the weld. I wish to understand how accurate the analysis is or whether it is a generalization.
Chris GardiniDell - Austin, Texas US
2000
Chris,
There are many reasons why paint fails to adhere at welded locations, here are several I would investigate.
I would first look at the weld process and find out what electrode is being used. If the process is using an electrode high in silicon then you may want to use an electrode containing less silicon. As an example, in Gas Metal Arc welding, if the process is presently using an ER70S-6 electrode that contains considerable amounts of silicon then you may want to change to an ER70S-3 electrode containing less silicon.
Next, take a close look at the cleaning operation, and find out whether fabricating soils are being entrapped between the metals and determine whether the surface is being cleaned prior to and after welding to remove oxides, scale and those tenacious carbon residues. Carbon and silicon are adhesion killers and should be removed by power brushing.
That's all I have for now, good luck.
- Warren, Michigan, USA
2001
Q, A, or Comment on THIS thread -or- Start a NEW Thread