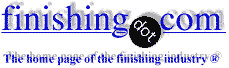
-----
Powder Coating Galvanized Substrate

for Engineers, Shops, Specifiers
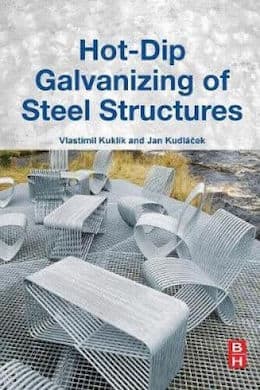
avail from eBay, AbeBooks, or Amazon
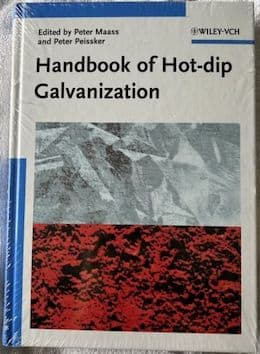
avail from eBay, AbeBooks, or Amazon
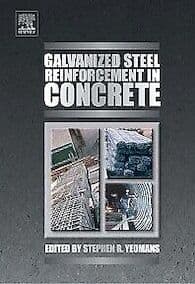
avail from eBay, AbeBooks, or Amazon
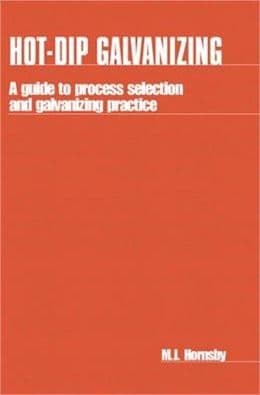
avail from eBay, AbeBooks, or Amazon
avail from Amazon
"User's Guide to Hot Dip Galvanizing for Corrosion Protection in Atmospheric Service" by NACE (1997 only rarely avail.)
avail from AbeBooks, or Amazon
(as an Amazon Associate & eBay Partner, we earn from qualifying purchases)
Hello,
I am a senior estimator in Myrtle Beach, S.C.
We are interested in learning about possible "adverse affects"that may occur with powder coat systems on galvanized piping. After reading many of your interesting articles on this matter, we feel confident with this application on galvanized surfaces, but we are uncertain with the specifications for pretreatment material type(s).Additionally, are there any known problems with surface bonding even if a specified chemical is used as the selected method for pre-treatment? What should a contractor look for on the finished product when determining compliance with bonding? Finally, what are the primary materials used by manufacturers for protection of the galvanized material surfaces? (i.e. Oil, wax, clear coat, etc.)
We would appreciate your sharing of information on this subject.
Thanks for your interesting Web Site !
Sincerely,
construction service- Myrtle Beach, South Carolina, USA
2000
A. Second part first! Most galvanisers do not protect although some may use a chromate dip to provide some white rust protection. A customer could doubtless specify any protection requirements, subject to quantity!
If the piping has a "rough" thick Zn surface, phosphoric acid etch cleaner followed by a chromate-resin dry-in-place pretreat will give 2000+ hours salt spray under powder. If gassing is a problem specify anti-gassing powder. The pretreat above cannot be degassed at high temp. without adverse effects.
Alternative is to use a dedicated hexavalent chromate process after acid etch. Rinse and dry gently. Then ramp up temp for the degassing cycle before coating. Either method should give excellent performance. Although zinc phosphating can be used it is quite difficult to get a really good fine grain complete coating. My UK experience shows that the first 2 methods will pass
BS 6497 (architectural spec for HDG/powder) and zinc phos won't. R
Walterisation (UK) Ltd - Croydon, UK
Q, A, or Comment on THIS thread -or- Start a NEW Thread