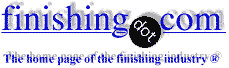
-----
Over-etched anodized parts and a ton of other problems
Q. Hi All. so my anodiser I suspect had a bright spark working for him when he worked on my parts.
My first problem is that I have different sized components, no bigger than 30 mm in diameter to 15 mm in diameter, but some components I believe have been over-etched and have come out extremely dull when compared to the rest of the batch and lack luster and also show signs of being "burnt" on the corners. So my first question is how do I get the components back to a shining finish and re-anodize them to match nice shinning parts. Do they have to be tumbled in ceramic media to save them? Please I have so many substandard parts that it's gotten expensive.
Next up is that in the orange dye section, I am having at the least 4 different shades of orange occurring in the same batch. What can be the cause of this. Also note that I send colour samples to match the colours as best as possible but I believe my blind grandma could do a better job.
I am also having an issue trying to get hold of good Bright green and Pink dye. I am trying to use Bright Dyes but the results are fairly poor. Please can someone assist with a good fastness with good UV resistance.
Last but not least is black. My black parts have come out dull and not really black but a fairly dark grey. Am I correct in saying that my anodizer is either over-etching and over-anodizing?
Owner of a company - South Africa
April 27, 2019
A. Since we don't know what your anodizer is doing , anything is really just a guess. But the combination of complaints sounds like what I've seen if the line tech leaves parts in the nitric acid pre-dye rinse too long; burnt appearance, dull/off-shade light colors, greying of dark colors.
As for new colors...
Look at the reliant 'outdoor colors' web page for chips because color, too, is so subjective. Pink tej is a great looking bright pink that I'm experienced with. Not sure if thats what you were thinking of. But you need to get the scorching/greying under control first or it's sadly irrelevant.
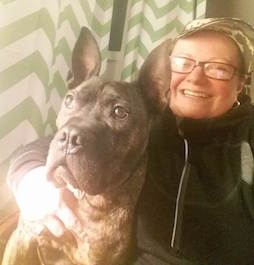
Rachel Mackintosh
lab rat - Greenfield, Vermont
April 29, 2019
May 1, 2019
A. Hi Graeme- Just noticed the problem description includes burning on the CORNERS. Missed that when I was scrolling through on my tiny-screened phone. One more thing that you should look into is whether they are racking multiple different sized parts on the same load, and not being able to maintain consistent current across the whole load. It would be interesting to see where the scorching is occurring on the load, but if you aren't seeing them come out of the bath yourself, and not until they've been processed and unracked- it's even more of a challenge to troubleshoot!
Sorry about that! Both my previous suggestion and this problem are potential sources of dye uptake problems!
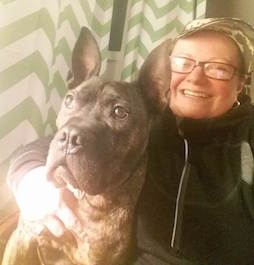
Rachel Mackintosh
lab rat - Greenfield, Vermont
Q. Hi there, it was said to me that the components were set up on the same tree. The larger components where the ones that came out dull. Anodizer is blaming material being different but I'm not buying it. Am I correct in saying that the size plays a major role in the anodizing process when they are mixed up components?
Graeme Lindner [returning]- South Africa
May 1, 2019
A. If the material is different in a single load, "current robbing" is a strong possibility. So your anodizer may be correct as to the cause. That being said, it does not absolve your anodizer from responsibility if he's aware of the differing alloys. For best results, only the same alloys should be ran in a load.
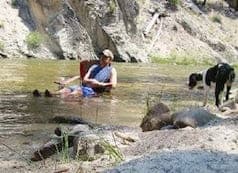
Marc Green
anodizer - Boise, Idaho
May 3, 2019
A. Do you know the thickness of the anodize? This also plays a role in the final color, you cannot get a black color with a low thickness anodize, and you can get different tones with different thickness for the rest of the colors.
Yohands Rey- Chihuahua, Mexico
May 8, 2019
A. Excellent points, Yohands! You are certainly correct that differing thicknesses will give differing orange tones, and that substantial anodizing thickness is required for good black anodizing (probably 0.0005" or more). But my own limited personal experience is that the color is a rather obvious purple rather than gray when the anodizing is too thin. Are there some dyes which yield gray in place of black if the anodizing is too thin?
Regards,
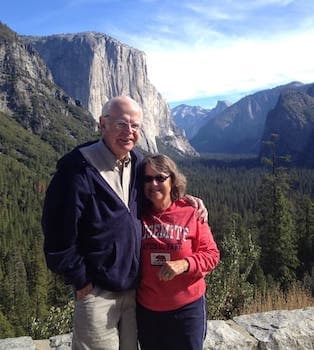
Ted Mooney, P.E. RET
Striving to live Aloha
(Ted can offer longterm or instant help)
finishing.com - Pine Beach, New Jersey
May 2019
A. I'm with Mr. Green on the different alloys, for instance, 7xxx series, if anodized together with 6xxx will develop a film that is thicker than the 6xxx parts in the same batch, that is on top of the film on the 7xxx being more porous and absorbing more dye thus having a much richer tone than the 6xxx parts, and at the same time 6xxx will pass less current resulting in thinner film that expected, resulting in a fainter color shade.
Depending on the cleaning/etching process used for that batch, it might have been possible to catch the "wrong" alloy parts and pick them off to run separately if the anodizer was aware of the possibility, 7xxx and 2xxx will develop dark/black film if etched in hot caustic, and 6xxx will not, or just a slight hint of gray (depending on etching time), here the operator could spot the "wrong" alloys and pick the parts off to run them separately.
But it is my strong opinion, as anodizer, that it is 100% customer responsibility to supply this information with the parts, and if the customer doesn't know, then say so, because when you process hundreds or thousands of parts a day, there simply is no time to deal with these issues, once the parts are racked, they stay there till the lot is complete, deracking, reracking, etc., running on a separate rectifier, or even in a separate lot takes extra time, and the customer 99% of time will not want to pay the extra for that effort.
There are several different black dyes, the one I'm currently using doesn't produce the purplish hue, it gradually goes from light gray to jet black, and minimum thickness that a full black tone can be achieved with regular Type II anodizing with this dye is around 12 micron, below that the part looks sort of like "black chrome", it is black but somewhat translucent, more so when the surface is wet. Usually cheaper black dyes will require thicker film coating, heating, longer immersion etc.
- Riga, Latvia
May 9, 2019
Hard Anodizing On a Budget
May 17, 2020Q. Good Morning All
So we are nearing the time that we will be setting up our own small scale industrial setup and we are wanting to do some hard anodizing. So I have a couple of challenges with regards to this setup.
1:Power supply
I am wanting to use a welding machine to be my main power supply, In fact I am wanting to use a 200 Amp tig welding machine. From what I understand , its crucial that I get the Amps per square foot to 35 amps but the tig welder is constant amp and not variable voltage. I want to anodize 2-3 parts each 1.4 square foot each. I am looking for 45 microns of finish (we are looking for the grey of 6061 and nothing else really). So if I do my sums right I get 36 mins at 35 amps per square foot. Is it necessary to change the voltage? If so, what voltage would I would looking at. Rectifiers here in South Africa are very expensive and I am doing a semi-industrial application.
2: Tank Cooling
How do I make an effective heat exchanger to cool the tank. I was thinking of having a PVC circulating line with antifreeze that will be cooled via a refrigeration unit? I have heard that people use lead pipe to be directly put into the tank and use it as the cooling element? And secondly how do I calculate the heat input into the anodizing Tank?
3: Can I use the same tank to do Type II and Type III anodizing, I would simply set the controller for the bath temp to be warmer? Would the acid concentration be a factor?
4.Heating Elements
with regards to heating elements can I use standard geyser elements or is something specific required?
5. Degreaser
Do I need a degreaser of can I just use the caustic etch? I have very limited space to lay out the tanks and if I can eliminate one that would be great.
6. Sealing
If I want to seal type III and Type II, do I need two separate solutions (cold and Hot Seal) Keep in mind I would like to anodize small parts to type II with colour.
7: Brightening
From what I have read, you can brighten your parts with a hot tank of phosphoric acid solution which is not a nice way as it's a little fuming. Is there a low temperature brightening solution out there?
- South Africa
May 2020
A. Hi Graeme. Limited budget or not, if I were you I'd retain an anodizing consultant or put off the project until you have more experience under your belt. An experimental lab can "make do" in ways that a production facility, even a very low production facility can't.
1. I personally can't imagine a welding machine as the power supply for hard anodizing -- have you ever seen this?
2. Yes, lead pipe can be directly put in the tank for cooling, but depending on how low a temperature you can hold in your cooling loop, it might be an awful lot of lead pipe. Every Watt/BTU you put into the tank with your power supply must be removed by cooling.
3. Although far from ideal, yes, it is possible to do Type II and Type III in the same tank with the same solution.
4. Sorry, "geyser" doesn't mean anything to me. But yes, electric heaters can be used.
5. Limited space, on top of unrealistic budget and limited experience, may be the straw that breaks your back. Are you planning on a de-smut/de-ox tank?
6. It's not impossible to seal everything in one tank, but it sounds like you may be building a house of cards. Each shortcut is a problem; stacking up shortcuts may prevent success.
7. I'm not sure exactly what you have in mind for 'brightening'. A bright dip tank contains nitric acid as well as phosphoric acid, and they are one heck of a lot more than 'a little fuming' -- it's horrible stuff; don't use it :-)
Regards,
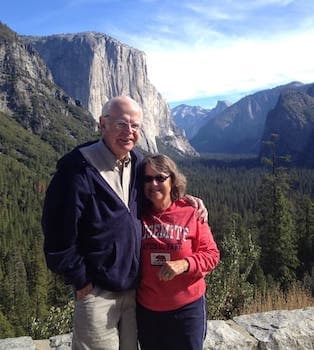
Ted Mooney, P.E. RET
Striving to live Aloha
(Ted can offer longterm or instant help)
finishing.com - Pine Beach, New Jersey
May 24, 2020
1. The voltage required to hold 35 ASF (you'd better start at 24 ASF) varies as the coating thickness resistance builds up, you must be able to keep increasing the voltage as the thickness builds. I have done a lot of anodizing with a welding generator, BUT NO HARD COAT!!
2. An external plate/frame exchanger is the "state of the art". The BTU requirement calculation is available in books.
3. I have many clients who do II and II in the same tank.
4. You will not need a heater if you do Type II on Monday and Tuesday, and Type III on Wed thu and Fri, By the next Monday it will be warmed back up, Do II at 72 °F, Do III at 32 °F
5 Etching before removing the organic spoil makes a messy pattern in the metal. NO, you must clean first; cleaning is more important than etching.
6. One seal will work on clear soft and hard, BUT, if you are sealing dye, you need a separate sealer for the clear.
7. From your above general questions I can tell that you are not technically ready to take on the complexity of bright dipping.
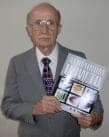
Robert H Probert
Robert H Probert Technical Services

Garner, North Carolina
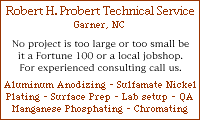
May 24, 2020
adv.
Hi Graeme, for the small fee we provide consultation how to do anodizing and hard anodizing in ambient temperature and with less amount of sulfuric acid. Contact us for more information.
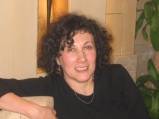
Anna Berkovich
Russamer Lab

Pittsburgh, Pennsylvania
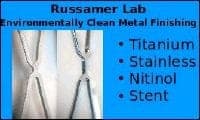

Q, A, or Comment on THIS thread -or- Start a NEW Thread