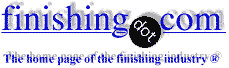
-----
Galvanizing Flux cleaning
October 18, 2018
Q. In Hot Dip (Batch) galvanizing its common to use a flux of ammonium and zinc chlorides. In many plants Fe gets carried into that solution from the prior pretreatment area, and ends up as iron hydroxide particles which eventually sink to the bottom of the flux tank.
Has anyone heard of using hydro-cyclone technology to separate that red mud from the flux liquid? Could it work, or is there insufficient difference in their densities to get good separation?
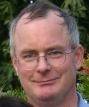
Geoff Crowley
Crithwood Ltd.
Westfield, Scotland, UK
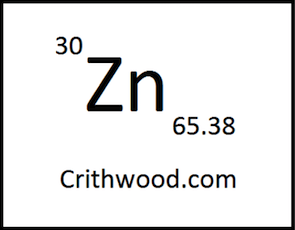
January 5, 2019
A. Geoff, I have a friend who has the equipment you mention. He says that it does not work. In the USA a filter press is used.
Regards,
Galvanizing Consultant - Hot Springs, South Dakota, USA
January 6, 2019
Mr. Geoff.
It's better to have continuous flux filtering system to reduce iron content from the Flux tank as well as reduce dross formation.
Gunatit Builders

Manjalpur, Vadodara, Gujarat
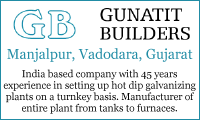
January 8, 2019
A. Iron in the flux does NOT cause dross. Since 1973 I have purified fluxes for iron and sulphate and the dross has never decreased. Sodium chloride in the flux likely causes dross. I say this because a pipes galvanizing plant noticed increased dross and the iron push down rods dissolved in the zinc when there was sodium chloride in the flux. Copper above about 0.25% in the zinc attacks the kettle. More dross and shorter kettle life.
Regards,
Galvanizing Consultant - Hot Springs, South Dakota, USA
January 9, 2019
A. Respectfully I have to disagree that "iron in the flux does not cause dross", but let me explain...
Iron in the zinc causes dross. Dross is iron-zinc alloy (Fe-Zn). To form dross, Fe is required, but there are many sources of the Fe. It can come from each of the following: The kettle; the kettle wall slowly dissolves in the zinc, and reports as dross. This isn't avoidable, but good temperature control and correct kettle steel spec reduces it.
The work being galvanized; even with short immersion times, steel immersed in zinc causes some dross to be produced. This is unavoidable, but minimal immersion time reduces it.
Tramp iron; by this I mean such as filings, drillings and the like that was not cleaned off the steel. This is avoidable.
Any Fe clinging to the work. Not all plants have driers, so liquid flux is present on some work. Even those that do have driers, the flux has its water evaporated, leaving whatever was dissolved in that flux as a solid on the steel's surface. Now the main constituents in flux are ammonium chloride and zinc chloride. They will be present on the steel in now solid form, as a crystal.
If there was also Fe dissolved in or carried as a solid in the flux solution, then this will end up in the zinc. It has nowhere else to go.
Is there a mechanism whereby Fe put into zinc doesn't form Fe-Zn alloy? If not, where does it go?
What form might that Fe be? It could be Fe metallic (forms dross without argument).
Fe oxide (FeO, Fe2O3, Fe3O4) does this form dross, or ash? Some will be reduced and combine to form dross.
Fe other complex:? as for oxides.
I have a long term (>20yr) correlation between Fe% in flux and zinc consumption. It's long enough to overcome the short term variation in consumption caused by varying steel types, shapes, market mix etc. It's in 2 plants. It's a strong correlation.
So I say that Fe in flux consumes zinc, some of that by dross formation.
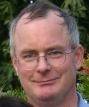
Geoff Crowley
Crithwood Ltd.
Westfield, Scotland, UK
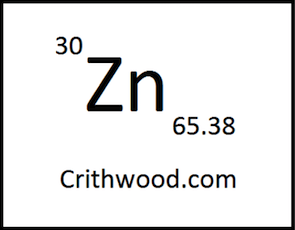
January 14, 2019
A. Geoff, Since 1973 nearly all the galvanizers have reported between 0.44% to 0.62% dross/production * 100%. The only reduction in dross has been attained by lowering the zinc temperature from 835 °F (working) to 815 °F and allowing the dross to settle for 12 hours. By doing so the dross needles grow in length and pure zinc can flow out of the scoop/bucket more easily and more completely. by this method dross has been reduced by 1/3. If near the bottom of the kettle is already near 815 °F, this method of reducing dross will not work; dross simply freezes up if the temperature is lowered. There needs to be 6 inches to 1 foot of high strength castable insulation under the kettle to save 40% of the kettle heating costs. A dross clam does not work. Wet kettle galvanizers usually report between 1% to 2% dross/production and higher for castings. Likely lead in zinc increases dross with castings. Recently a wet kettle galvanizer had 9.5% iron (Fe+2) in his flux and changed it out for new flux. The only change he noticed was a reduction of new top flux of 20%. His dross/production remained at 1.1%.
If you could post your dross/production and zinc/production versus iron in the flux, I would be quite interested. Keep in mind that to remove iron in flux, ammonium hydroxide is used and will increase the ACN of the purified flux. which shortens "cook-off" times which gives thinner zinc on the steel. The chemistry/physics hand book list the boiling points of Iron II and Iron III chlorides at about 300 °C, thus iron may exit the area with the smoke.
Galvanizing Consultant - Hot Springs, South Dakota, USA
January 16, 2019
"Since 1973 nearly all the galvanizers have reported between..." I assume you mean all those you have contact with, not all the galvanizers in the world? But I accept that this range is typical of what many report, and we also fit in that range.
"The only reduction in dross has been attained by lowering the zinc temperature..." Again I assume that refers to those operations you have data for. There are many thousands of plants worldwide (>5000 in China for example). Some have found other means of also affecting dross production than only temperature change, though again I accept that temperature change will cause a change in dross production, but I think you were referring to dross separation (from zinc) in the removal tool, rather than production of that dross in the kettle.
Of course what remains in the removal tool is all classed as dross, so allowing the separation of dross from zinc, recovering that zinc has the apparent effect of reducing dross production.
I have seen many plants where ineffective separation results in apparently high dross production.
"There needs to be 6 inches to 1 foot of high strength castable insulation under the kettle to save 40% of the kettle heating costs..."
There does need to be insulation there, but the purpose is not gas consumption reduction, it is to prevent heating the kettle at that area. That insulation does not need to be castable, many other forms work equally well, and cost less to supply and install.
I do not believe that 40% of total gas cost could be saved by having or not having this insulation. At a guess I'd believe a number like <5%
"A dross clam does not work."
Had you said that a spoon/shovel type removal tool is more effective, that would be more acceptable. A dross clam can work, but less effectively. Many thousands are made sold and used sufficiently well. It's not my preference, and we don't use them, but many do and effectively.
"Wet kettle galvanizers usually report.... "
I forget how many plants I've visited, but a few hundred. I've have yet to encounter anyone using this very old method, and I've never heard of any either. There might be some, somewhere, but surely very few?
Therefore the report of one of these experiencing no dross production reduction as a result of replacing his flux isn't really representative of anything. He has a problem somewhere with 1.1% dross, with the possibility to halve that by changing something.
"....to remove iron in flux, ammonium hydroxide is used..."
There are other ways to remove Fe from flux. Did you mean ammonia
⇦ on
eBay or
Amazon [affil link] and peroxide perhaps? That's the one that seems to be most common. Many companies in Europe and Asia are buying one of the various flux cleaning machines. These fully automated plant items consume ammonia and hydrogen peroxide, taking a quantity of flux from an operating tank, treating it to remove the Fe and then adjusting the flux back to proper chemistry and returning it to the tank. The human interventions are to clean the filter system (bag or press), and to supply chemicals. It is possible to get flux to an Fe level of less than 0.1%Fe
"...which shortens "cook-off" times... "
I've found no correlation between flux condition and "cook off time". It is more affected by heat transfer rate between zinc and steel in my opinion. But I agree shorter immersion time in total reduces zinc consumption by lowering coating weight.
In jobbing galvanizing, it is very difficult to correlate coating weight to anything, due to the high steel chemistry variation swamping the small change brought by other factors.
Dross will form at typical galvanizing temperatures from any source of Fe. The zinc isn't selective in which Fe it attacks, but the rate of attack is dependent on the chemistry of the steel (Si, P, etc.), hence the special chemistry for kettles. But suspension wire and the work being galvanized form some dross, as does any other Fe in the liquid zinc, however it got there, via flux of otherwise.
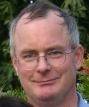
Geoff Crowley
Crithwood Ltd.
Westfield, Scotland, UK
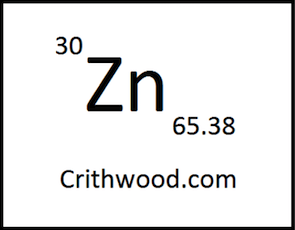
Thanks for the very interesting dialog, gentlemen! Who'd have guessed that people who have spent their whole working lives in a narrow metal finishing discipline don't feel they need lectures on it :-)
Carry on, the rest of us are learning from it!
Regards,
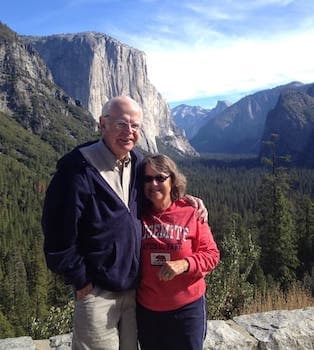
Ted Mooney, P.E. RET
Striving to live Aloha
(Ted can offer longterm or instant help)
finishing.com - Pine Beach, New Jersey
January 2019
Geoff, I am trying to determine the negative effects of iron (Fe+2) or iron (Fe+3) in the flux. You have indicated that you have data that shows that lower iron in the flux gives lower zinc usage (%GZU) and I certainly agree. My question is: Do you have data that shows lower iron (Fe +2 or Fe+3) or both reduce dross? If so, please post it.
In the USA I know of four wet kettles. Not because they want a wet kettle but because they do not have enough space. I know of only one galvanizer who has a flux purification machine from Europe and it does not work well. Currently there is a flux purification machine being developed in the USA, and installed in two plants. Initial results look good.
I will email you my latest article called "Dynamic Testing of Hot Dip Galvanizing Flux." These tests take about one hour of kettle time and I hope you may be able to do the tests.
I expect that you and I agree on many more things than what we do not agree on.
Regards,
Galvanizing Consultant - Hot Springs, South Dakota, USA
January 16, 2019
January 17, 2019
On Fe in flux affecting dross: What we have is a long term trend that correlates Fe in flux (doesn't differentiate between valence states of the Fe) and dross ratio (Dross/tonnes steel coated expressed as %).
I don't want to post the data here, but could share it otherwise. Would take a little work to extract into useful format.
An important point we have come to learn is that considering both top ash production and dross make, is that looking at a month in isolation can be quite misleading. In this industry there are too many variables influencing outcomes, and some of these are short term. For example, I guess no-one could warrant that their drossing has the same level of thoroughness each time they do it. And different galvanizers have different ideas on drossing frequency. Some dross at set tonnage galvanized, others on a time based interval, some a mix of these. It's often convenient to use time (to move the operation out of production time, and to allow a rest period for stirred up but un-removed dross to settle to the bottom again). We tend to do it on Friday nights, minimum fortnightly, but weekly if tonnage is higher. And then there's technique: if a lot of zinc is left in the removed dross, then the % dross appears artificially high. Lean dross, crystals of the Zn-Fe complex only, is best, but not so simple to achieve. Examination of the finished lump or ingot of the dross usually shows "bleeds" of zinc on the sides where effective separation of zinc and dross has not been achieved.
On flux cleaning machines.
Ours was from the USA, but there are quite likely more available in Europe. I know the USA company we bought from sells plenty of them worldwide including USA. (They are an advertiser on this site). They have refined its construction since we bought, but our version is less robust and user friendly than it could be, (minor complaint) but the principles and chemistry are pretty much the same from all suppliers of these devices.
Most use some level of automation, with redox and pH probes, timers and a control device (PLC usually). A cycle of operation is programmed and the machine works away unattended until the filter system gets full of iron hydroxide and needs cleaned out. This red mud (very similar to that experienced in the alumina refining industry) is messy sticky dirty stuff to work with, and the best machine will be the one that not only does the chemistry, but makes handling this mud easier.
I concur that we agree on more than we disagree, but its the points of disagreement where there's more to learn. At least I learn more there; I'm sure all do. And if our public discussion helps the industry generally (as Ted M has said) then that's a good thing too.
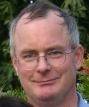
Geoff Crowley
Crithwood Ltd.
Westfield, Scotland, UK
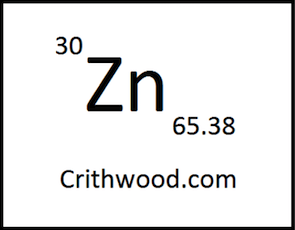
! Initial results for my new Dynamic Flux Tests are EXCELLENT. If you do these tests (about one hour required), then post them on finishing.com and I will comment. Words or photos are the best way for me to understand your results of the tests. Thank You.
Dr. Thomas H. CookGalvanizing Consultant - Hot Springs, South Dakota, USA
January 31, 2019
February 4, 2020
Q. Hello,
My name is Maryam and I work as quality control manager in a galvanizing factory. We are setting up a system for flux purification. We are currently using hydrogen peroxide to purify the flux from iron +2. I have some questions:
1. Is it reasonable to use ozone instead of hydrogen peroxide? Which is better and why?
2. What is your suggestion for agitating the flux in the tank? Is the air blowing good idea or not?
3. How to calculate the appropriate percentage of H2O2 and NH3?
4. When we should add ammonia to the Flux? I mean how long after adding H2O2?
Thank you very much for sharing your knowledge and experience.
Fara Gostar Bistoon (FGB) - Karaj,Iran
Cleaning the flux in the production tank isn't a good idea, it makes a mess of the tank with the iron hydroxide left in there. There's enough forms there anyway, and its a pest, creating dross when it gets to the zinc.
Air agitation works a little but not much. It has the side effect of stirring up the settled iron hydroxide on the bottom of the tank.
There are machines available to treat the flux outside the production tank, and with these you can get Fe below 0.1% Some use a filter process, some bag filters, but they all use the peroxide / ammonia system. Good machines come with redox and pH probes that control the whole process allowing you to start the machine and come back later to clean up. Some can be left running for days such that they're almost automatic.
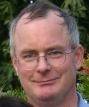
Geoff Crowley
Crithwood Ltd.
Westfield, Scotland, UK
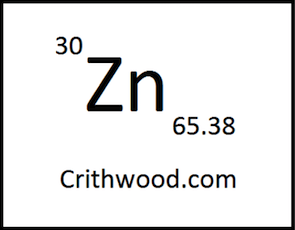
March 4, 2020
A. Hydrogen peroxide works only when the pH is 5 or above. The NH4OH must be added first. Ozone works at nearly any pH. The trick is to separate the clear liquid from the "tomato soup." Three volumes of NH4OH is used with one volume of H2O2. Above about 2% iron, recovery is quite low.
Regards,
Galvanizing Consultant - Hot Springs, South Dakota
March 6, 2020

Q, A, or Comment on THIS thread -or- Start a NEW Thread